Desktop Metal Qualifies 420 Stainless Steel for High-Volume Additive Manufacturing
Desktop metal single pass jetting technology enables mass production of high-strength, end-use parts in 420 stainless steel for applications across medical, defense, aerospace and consumer products.
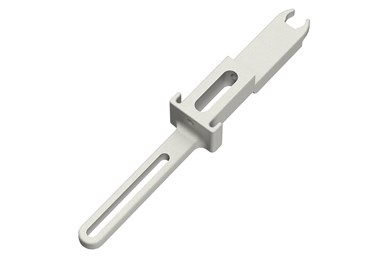
One application example is a locking articulation bar in the medical/surgical field. Photo Credit: Desktop Metal
Desktop Metal has qualified Grade 420 stainless steel (420 SS) for use on its Production System platform, which utilizes single pass jetting (SPJ) technology and is designed to achieve the fastest build speeds in the metal additive manufacturing (AM) industry. Manufacturers can now leverage SPJ technology for the mass production of high-strength, end-use parts in 420 SS for demanding applications in industries such as medical, aerospace, defense and consumer products.
A martensitic, heat-treatable, stainless steel, 420 SS is characterized by its high strength and hardness as well as its corrosion resistance to the atmosphere, foods, fresh water and mild acids when in a fully hardened condition. The 420 SS is a common material used extensively across a variety of applications such as surgical and dental instruments, ball bearings, gear shafts, pump and valve components, fasteners, gauges, hand tools and high-end cutlery.
“Engineers continue to seek out metal additive manufacturing as a leading option to drive innovation in design and manufacturing,” says Jonah Myerberg, Desktop Metal CTO and co-founder. “We believe our qualification of 420 SS and other high-strength alloys will accelerate the deployment of our AM 2.0 solutions among customers looking to successfully mass produce critical parts at scale.”
Desktop Metal’s materials science team has qualified and fully characterized 420 SS printed on Production System technology that meets MPIF 35 standards for structural powder metallurgy parts set by the Metal Powder Industries Federation. Parts printed in 420 SS on the Production System platform eliminate the use of tooling and minimize material waste, as well as represent a significant decrease in production time and part cost compared to conventional manufacturing methods, the company says.
Examples of key applications include a locking articulation bar in the medical/surgical field, a valve nozzle adapter in aerospace, and twin screw extruder mixing elements in high-volume manufacturing.
Related Content
-
Neighborhood 91 Expands, With Metal Powder Works and HAMR Now Open
Ribbon cuttings for the Pittsburgh campus's newest tenants coincided with the announcement that a DOD-funded resilient manufacturing program will also be developed at the site.
-
This Year I Have Seen a Lot of AM for the Military — What Is Going On?
Audience members have similar questions. What is the Department of Defense’s interest in making hardware via 3D printing over conventional methods? Here are three manufacturing concerns that are particular to the military.
-
Quadrus: Powder Management Tactics for Tungsten Rhenium and Other AM Alloys
The expert in additive manufacturing of high-value parts for the Defense Department often must change from one exotic material to another in its powder bed machines. Cleaning is a core competency. Here are lessons of this company’s system for working with an ever-changing mix of 3D printed alloys.