Desktop Metal Qualifies 316L for Mass Production on Shop System
Shop System binder jetting is said to enable cost-effective batch production of high-quality 316L stainless steel parts via additive manufacturing.
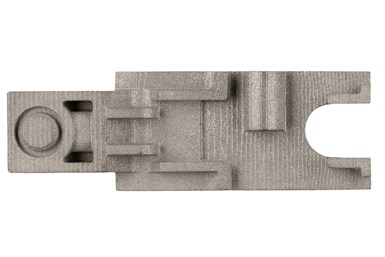
Medical device closure printed with 316L on Desktop Metal’s binder jetting Shop System.
Desktop Metal has qualified the use of 316L stainless steel for its Shop System, which is said to be the world’s first metal binder jetting system developed for machine shops to produce hundreds of thousands of parts with no tooling required.
With an expanded materials portfolio, users can leverage affordable, high-quality binder jetting technology to print end-use parts in 316L stainless steel with throughput, print quality and productivity unattainable via legacy additive manufacturing (AM) processes, the company says.
The 316L is an austenitic stainless steel known for its corrosion resistance, high ductility and excellent mechanical properties at extreme temperatures. The company says it is well-suited for demanding environments and applications, such as parts exposed to marine, pharmaceutical or petrochemical processing, food preparation equipment, medical devices, surgical tooling and consumer products such as jewelry.
The Desktop Metal materials science team validated that 316L stainless steel printed and sintered using the Shop System meets MPIF 35 standards set by the Metal Powder Industries Federation. Featuring an advanced single-pass print engine, the Shop System offers a turnkey solution for producing complex, end-use metal parts in a fraction of the time and cost of conventional manufacturing and comparably priced legacy AM technologies, the company says.
The Shop System is said to include all the equipment machine shops need to begin binder jetting — from printing through sintering — and is designed to scale throughput with a range of build volume configurations. In addition, Desktop Metal software for build preparation and sintering simulation, in combination with metal powders and process parameters optimized to deliver exceptional part quality and repeatability, are said to make it easy for businesses to get up and running with binder jetting in days instead of weeks or months.
Related Content
-
VulcanForms Is Forging a New Model for Large-Scale Production (and It's More Than 3D Printing)
The MIT spinout leverages proprietary high-power laser powder bed fusion alongside machining in the context of digitized, cost-effective and “maniacally focused” production.
-
3D Printing Molds With Metal Paste: The Mantle Process Explained (Video)
Metal paste is the starting point for a process using 3D printing, CNC shaping and sintering to deliver precise H13 or P20 steel tooling for plastics injection molding. Peter Zelinski talks through the steps of the process in this video filmed with Mantle equipment.
-
3D Printed NASA Thrust Chamber Assembly Combines Two Metal Processes: The Cool Parts Show #71
Laser powder bed fusion and directed energy deposition combine for an integrated multimetal rocket propulsion system that will save cost and time for NASA. The Cool Parts Show visits NASA’s Marshall Space Flight Center.