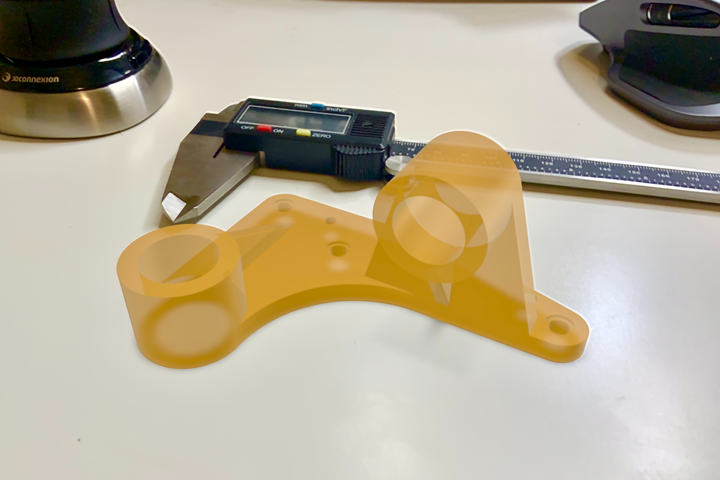
The bracket in the foreground is a “massless” prototype placed on the table via augmented reality. PolySpectra’s new AR tool allows users to view their STL files in the real world before hitting “print.” Photo Credit: polySpectra
3D printing transformed the speed of physical prototyping, opening up avenues of innovation that were previously inaccessible to product developers. But increased design iteration can also lead to increased material usage, and maybe even greater waste. PolySpectra founder Raymond Weitekamp believes that the next evolution for prototyping will be even more rapid and even more capable — but less physical as well. His company’s Massless tool offers an intermediary step between fully digital designs and 3D printed prototypes through an augmented reality (AR) interface that allows for previewing an STL in the user’s physical space before hitting “print” or “buy.”
“Web AR capabilities are already available on phones, tablets and computers,” Weitekamp explains. “This is a way to manifest a 3D dimensional object in physical space,” without investing printer time, materials and other resources into producing early-stage prototypes and parts still in development.
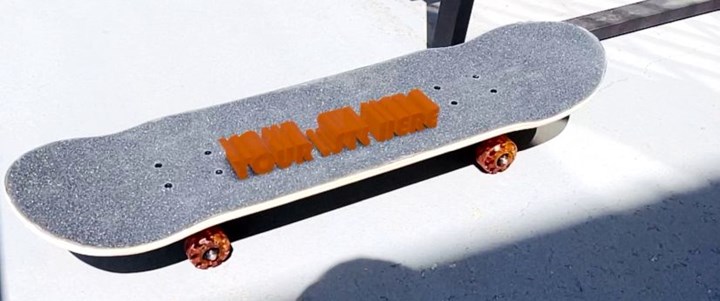
Massless allows users to place virtual objects into their real environment and view them at their actual size. Here, an AR rendering that reads “YOUR .STL HERE” sits on top of a skateboard. (The wheels are 3D printed from polySpectra’s COR Alpha resin — and they are an example of a “massless” product the company produces and sells on demand rather than keep in inventory.)Photo Credit: polySpectra
Prototyping Through Augmented Reality
Massless is a free online tool that allows users to upload their own STL files and see them rendered into physical space through a smartphone or tablet. Files can be uploaded from these mobile devices or from a PC; in the latter case, the user will receive a QR code to scan with the device camera to activate the AR experience. The AR viewer places the object on a flat surface visible in the camera, and allows the user to manipulate it within this physical environment.
Click here to try it for yourself with the Additive Manufacturing Media logo, or any handy STL file.
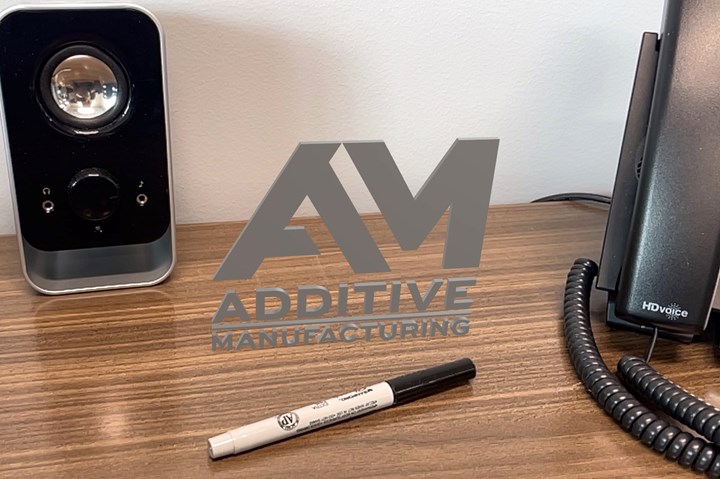
With its open gaps between the letters, we won’t be 3D printing this version of the AM logo any time soon. Still, the AR tool made it easy to assess the size and shape of this massless object compared to other items on my desk.
The goal of manipulating an AR object as opposed to a physical one is not to bypass 3D printing and prototyping, but rather to eliminate obvious problems and challenges in a virtual stage. “This won’t replace physical prototypes to check exact dimensions or snap fit,” Weitekamp says, “but it will help you evaluate whether this design is what you actually want.”
This could mean even faster, cheaper iterations for product designers and manufacturers. It could also mean an avenue to more custom and on-demand product manufacturing; if consumers can “see” an object in their home before ordering it, they may forgo visiting a brick-and-mortar store to view it in person as part of the buying process. That seller’s inventory can thus become digital, with no need to actually produce anything until the moment it is needed.
Massless Prototyping for Responsible 3D Printing
This push to augmented reality might seem at odds with the other parts of the polySpectra business, which develops materials for additive manufacturing based on a UV-activated chemistry Weitekamp discovered during his postgraduate research and provides printing services for parts made from these high-performance materials. Its first commercially available product is COR Alpha resin for digital light processing (DLP), suitable for challenging applications including medical and aerospace parts, and the company was recently awarded funding from the Department of Energy to advance 3D printed tooling along with printer manufacturer Fortify.
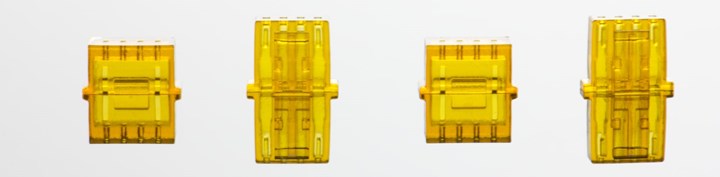
COR Alpha resin is suitable for applications ranging from molds to brackets to skateboard wheels to microconnectors like the ones pictured here. Photo Credit: polySpectra
But polySpectra is not just in additive manufacturing to sell parts or material; Weitekamp sees these resins fitting into very specific niches, and massless prototyping is a way to help ensure they are being used in the best, most responsible way possible. That means better products faster — by virtue of better design and prototyping tools — as well as distributed and on-demand manufacturing.
Prior to the chemistry discovery, Weitekamp’s work was mostly in renewable energy and so it has remained important to him to approach additive manufacturing from a sustainability perspective. He sees a three-pronged approach to pursuing reduced energy usage through AM:
- Embrace digital and “massless” design, validation and shopping so that less waste is produced.
- Use 3D printing to create items with “less mass” that are lighter and more efficient, through design and high-performance materials.
- Embrace less movement. (“30 percent of the energy usage in the United States is for transportation,” Weitekamp says.) Distribute manufacturing to make products and parts closer to where they are needed and reduce energy embedded in shipping.
Massless prototyping may be just the first step, but it could help to advance this overall mission. For now, it’s about raising awareness through a free, widely accessible and virtual option.
“Augmented reality won’t solve energy consumption, but it will get people to think twice about making something,” he says.
Related Content
Copper, New Metal Printing Processes, Upgrades Based on Software and More from Formnext 2023: AM Radio #46
Formnext 2023 showed that additive manufacturing may be maturing, but it is certainly not stagnant. In this episode, we dive into observations around technology enhancements, new processes and materials, robots, sustainability and more trends from the show.
Read MoreConcept Sneaker Boasts One-Piece 3D Printed TPU Construction
The Reebok x Botter Concept Sneaker Engineered by HP premiered at Paris Fashion Week, hinting at manufacturing possibilities for the future of footwear.
Read MoreNext-Gen Horse Trailers to Be Built With Robotic 3D Printing
Double D Trailers is currently developing a prototype horse trailer that will be made with large-format additive manufacturing. The technology brings potential benefits for labor, weight and design features to this subset of recreational vehicles.
Read MoreHow 3D Printing Aids Sustainability for Semiconductor Equipment: The Cool Parts Show Bonus
Hittech worked with its customer to replace fully machined semiconductor trays with trays made via DED by Norsk Titanium. The result is dramatic savings in tool consumption and material waste.
Read MoreRead Next
To Scale Additive Manufacturing, Separate Design and Production
Spokbee’s online marketplace is designed to ease the launch and sale of customizable, 3D printed products. Its flexibility comes from cloud-based CAD and a distributed network of service bureaus for production.
Read MoreRekkie AR Ski Goggles Made Possible With 3D Printing: The Cool Parts Show #53
When the electronics enclosure key to these AR goggles proved difficult to mold, 3D printing allowed the inventors to keep the complexity — while also making improvements for assembly and user experience.
Read More3 Types of 3D Printed Tooling for Injection Molding: AM Radio #16A
3D printed tooling for injection molding, including mold inserts, components and end of arm tooling, were on display at the Plastics Technology Expo.
Read More