One notable exhibit at the recent Rapid + TCT 2021 tradeshow made a point that should have been unsurprising. With the proven, working mold tool on display in its booth, ExOne illustrated that binder jetting — the additive manufacturing technology for which the company is known — can be used to make an injection mold. Indeed, the company was sharing plastic ice cream scoops that had been molded with this tool, which was made of bronze-infiltrated stainless steel. North American Mold of Auburn Hills, Michigan, designed the mold; the company has partnered with ExOne to prove out binder-jetted tooling for both injection mold and blow mold applications.
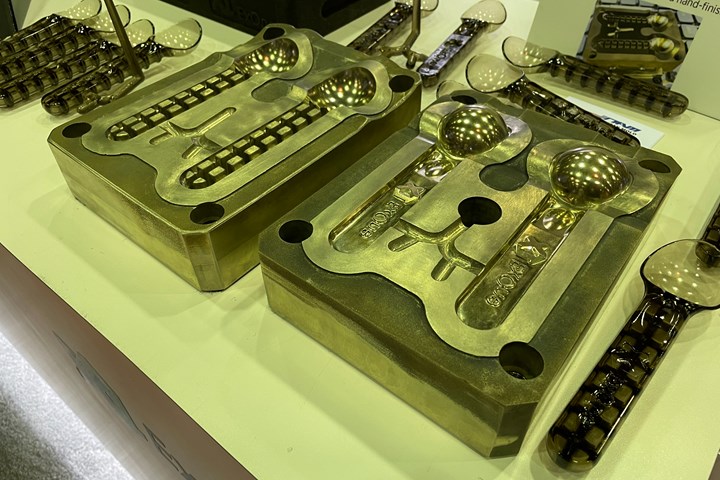
This injection mold was made via binder jetting from 420 stainless steel infiltrated with bronze.
ExOne recently launched what it is calling its X1 Tooling portfolio, offering 3D printed tooling at reduced cost and lead time compared to conventionally made tooling for applications including molding, forming and composites layup.
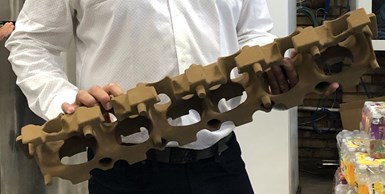
Binder jetting to make tooling is not new — 3D printing sand is well established for making tooling used for metal casting. This 3D printed sand core used to form an engine block water jacket was made by Humtown Additive.
Here is why the mold tool should have been unsurprising: Binder jetting has been making tooling all along. Sand 3D printing via binder jetting is a now-established method of making complex tooling in fast lead times for metal casting. And technology developed recently for infiltrating and coating sand 3D printed forms extends the application range beyond casting to include various “hard” tooling applications as well. ExOne chief technical officer Rick Lucas notes that this new development in part relies on metal infiltration, a proven capability that is a poor fit for many binder jetting applications involving production parts rather than tools.
“Infiltration of one metal into another metal is a technique that allows us to achieve finer dimensional control during sintering,” Lucas says. The added metal essentially fills space between particles of the primary metal, holding the resulting part’s volume and dimensions as the metal particles fuse into a fully dense form during sintering. A part subject to 20% shrinkage during sintering might see less than 1% shrinkage with an effective infiltration material added. But this is frequently not an acceptable solution for end-use parts. “Major OEMs seeing the promise of binder jet for production parts made clear: They needed the known, well-understood material properties that came from a pure alloy,” Lucas says. Binder jetting found its successes in production parts in large measure because ExOne found different avenues to dimensional control for single-material components.
The company has been focused on production because binder jetting delivers distinctive strengths here. Binder jet is a metal AM process with no phase change (that is, no melting and resolidifying), so material structure and stresses are controllable. In addition, binder jet’s ability to nest parts in three dimensions means a single 3D build might produce a large batch of parts. It was covid-19, in part, that redirected this focus for the metal AM capability. ExOne CEO John Hartner says, “As the covid pandemic has continued wreaking havoc on supply chains, we’ve had more and more manufacturers ask us: ‘Can you 3D print our tooling?’” In a word, yes, he says. The company was never far from recognizing a potentially expanded role for binder jetting for tooling; it has used hard tooling made with sand in its own production, and infiltration similarly offers a way to obtain precise hard tooling in metal quickly and economically.
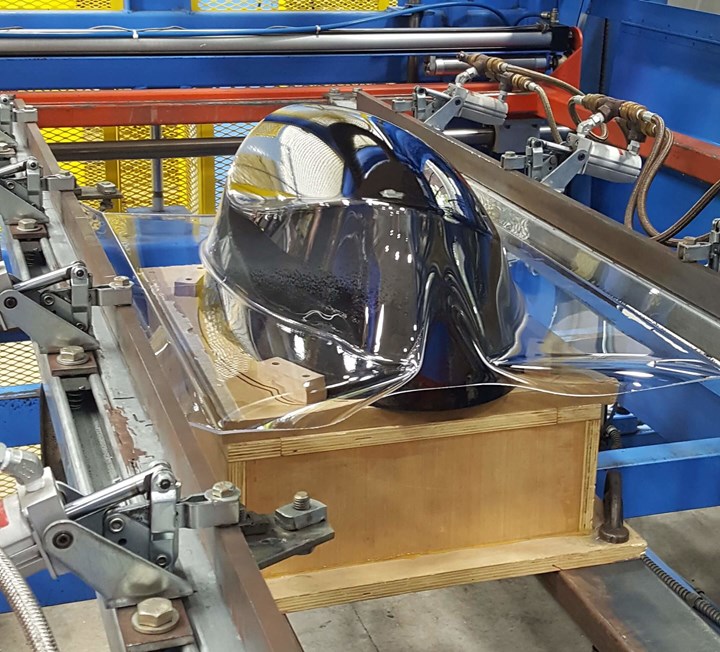
The tool in this thermoforming operation was made by infiltrating and coating 3D printed sand. Photo courtesy of ExOne.
Now, the new X1 Tooling portfolio arguably covers the broadest range of tooling needs of any AM capability. Among other additive processes, reinforced polymer 3D printing is effective for tooling for composites and laser powder bed fusion is effective for mold tooling. Binder jetting spans both these applications. With 3D printed sand, including infiltrated sand, the portfolio includes competitive tooling solutions for casting, composites (both layup and sacrificial wash-out tools) and thermoforming. In 3D printed metal, the portfolio includes solutions for plastics molding and robotic end-of-arm tools. In addition, the interest of larger manufacturers in 3D printed tools in H13 has led to a fast-tracking of the development of binder jetting in this tool steel. This capability is likely to lead to hard steel tooling for casting and other metal part molding.
The potential tooling size range is arguably broad as well, company representatives note. One part of the binder jetting process in metals is sintering, in which the 3D printed form is made hard and solid through its particles fusing together under heat. ExOne notes the fusing can be leveraged to increase potential size. To make a very large tool, sections of the tool 3D printed separately can be allowed to fuse into one within a large furnace.
Related Content
America Makes Announces IMPACT 2.0 Project Call Worth $6.6 Million in Funding
The deadline for the first set of project proposals is May 29.
Read MoreAM 101: What Is Binder Jetting? (Includes Video)
Binder jetting requires no support structures, is accurate and repeatable, and is said to eliminate dimensional distortion problems common in some high-heat 3D technologies. Here is a look at how binder jetting works and its benefits for additive manufacturing.
Read MoreStratasys and Desktop Metal to Combine in Approximately $1.8 Billion All-Stock Transaction
Merger looks to deliver industrial polymer, metal, sand and ceramic solutions from design to mass production.
Read MoreLooking to Secure the Supply Chain for Castings? Don't Overlook 3D Printed Sand Cores and Molds
Concerns about casting lead times and costs have many OEMs looking to 3D print parts directly in metal. But don’t overlook the advantages of 3D printed sand cores and molds applied for conventional metal casting, says Humtown leader.
Read MoreRead Next
Impressions and Trends from RAPID + TCT 2021: AM Radio Bonus
Peter Zelinski, Stephanie Hendrixson and Julia Hider discuss what they saw, heard and learned at RAPID + TCT 2021 in a special episode of the AM Radio podcast plus slideshow.
Read MoreCommercializing Sand 3D Printing in the New Tech Belt
Youngstown-area Humtown Products supplies both conventional and 3D printed sand cores and molds to foundries around the world. But sand tools for castings may be only the beginning.
Read More10 Examples of 3D Printed Tooling
Additive manufacturing can aid conventional manufacturing through the production of tooling. This article showcases 10 clever uses of 3D printed tooling.
Read More