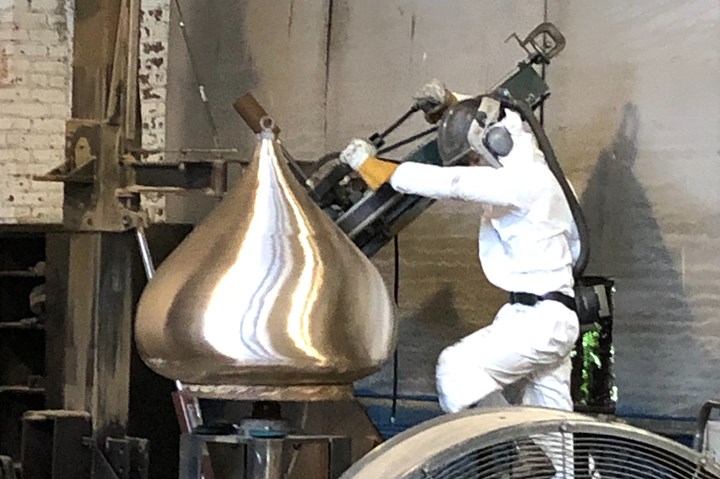
A final polish is applied to a Hershey-Kiss-shaped bell commissioned for Hershey Park in Pennsylvania. The bell was cast by The Verdin Co. using a 3D-printed mold pattern created by Cincinnati Inc. Photo credit: The Verdin Co.
There’s a reason why only a handful of people in the world know how to produce a properly tuned bell, and the reason has to do with harmonics. Picture a church bell ringing: When the clapper strikes the bell, the first sound that you hear is a composite of different tones produced by a complex series of harmonics called partials. These partials are generally recognized as the hum, the prime, the minor third, the perfect fifth and the nominal.
The harmonic frequencies of these five partials are influenced by two principal factors: the shape of the bell — the outer shape versus the inner shape — and the thickness of the bell wall that varies from top to bottom. What makes the process of tuning a bell so complex is that each of these five tones overlap. If you are trying to tune the nominal tone, you can’t help but to flatten the minor third, for example. The partials cannot be tuned entirely independently from one another.
This makes the shape of the bell incredibly important. If a bell’s shape results in one of the partials being over or underrepresented, there is no way to bring it back in line with the others through tuning. And, in order to achieve a precise bell shape, the tolerance for its mold pattern has to be incredibly tight.
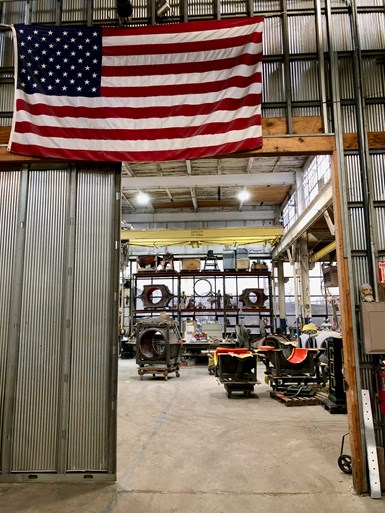
A peek inside one of the finishing rooms at The Verdin Co., established in 1842 in Cincinnati, Ohio. Today, Verdin is one of just a few bell foundries in the world. Photo credit: Brent Donaldson
The Verdin Co. in Cincinnati, Ohio, is one of the largest and, at nearly 180 years old, oldest bell foundries in the world. In recent decades, the company has been creating permanent mold patterns made from cast aluminum — mold patterns that can be reused again and again rather than creating one-offs and starting the process from scratch each time. That method — extremely labor intensive — has been around for hundreds of years. Too involved to explain here, this sand casting process requires building an inner and outer mold entirely by hand, starting with a sweep of an existing bell’s inner and outer profile. After the inner and outer molds are created, they are placed together and molten metal is poured into the space between them. After cooling, the mold is then split apart and the pattern is removed. It is then polished or machined for a final surface finish.
The problems with this method are its high cost, the guesswork involved that sometimes results in scrapped patterns and the long lead times to acquire the raw material.
Back in late 2018, these factors were on the mind of Tim Verdin, the sixth-generation president of the Verdin Company, when he read about large-scale, 3D-printed molds being used in the construction industry for concrete casting. Verdin learned that not only did the company that printed these molds happen to be nearby, it also happened to be a business that has also been around since the 19th century — Cincinnati Inc.
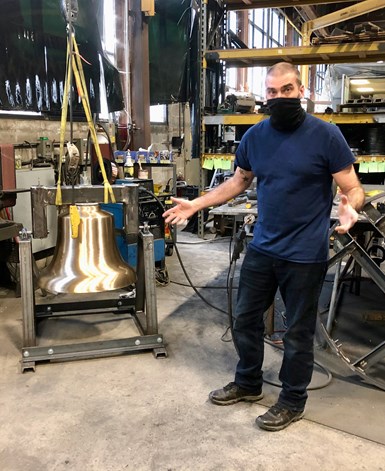
Tim Verdin, the sixth-generation family president of The Verdin Co., shows off a bell in its final assembly stage of production. Photo credit: Brent Donaldson
For this story I talked to both Tim Verdin and Alex Riestenberg, Cincinnati Inc.’s additive manufacturing product manager, who would end up spearheading what has become an ongoing collaboration — a collaboration that involves high-precision, large-scale fused filament fabrication (FFF) printing and centuries-old sand-casting techniques. As far as Verdin and Riestenberg know, this strategy of 3D printing highly precise bell mold patterns for sand casting operations had never been tried. So, naturally, they had questions: Could large-format additive manufacturing (LFAM) achieve tolerances as low as ±0.010 inch for uniquely shaped molds such as these? What’s the best orientation for printing the part? What kind of support structures would be necessary, or would support structures cause the part to go out of tolerance? Would the patterns be durable enough? And how can a smooth finish be achieved though the ridged layering of carbon fiber ABS material?
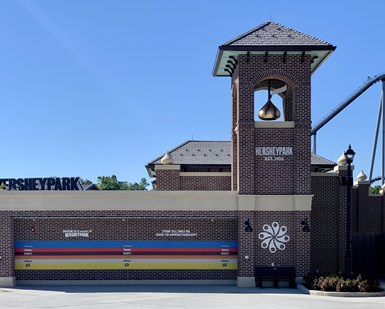
The Hershey Kiss Bell, started as a 3D-printed mold pattern, today hangs at Hershey Park in Pennsylvania. Verdin also created the World Peace Bell, the largest free-swinging bell on the planet, which resides in Newport, Kentucky. Photo credit: The Verdin Co.
It took several weeks of experimenting, but Riestenberg and Verdin have been able to answer all of those questions and more. And now, another historic American company bears the fruit of their efforts: The iconic Hershey’s Kiss bell at Hershey Park began its life as a carbon fiber slurry being extruded on a Cincinnati Inc. Big Area Additive Manufacturing (BAAM) machine.
The Experiments Begin
When Verdin and Cincinnati Inc. began working together, Riestenberg had never seen a casting pattern before, while Tim Verdin had never seen a large 3D-printed part. The two decided to begin experimenting with 3D-printed mold patterns for a half-dozen standard bells, each roughly two feet in height.
The Hershey Kiss bell mold pattern during printing at Cincinnati Inc. The pattern was printed with a carbon fiber ABS material and required a tolerance of ±0.010 inch. Photo credit: Cincinnati Inc.
The first challenges to overcome involved design considerations for the print itself: If oriented right side up during the print, much of the bell pattern’s inner cavity would require support structures. Verdin had informed Riestenberg that, for the tuning considerations mentioned previously, achieving a smooth surface finish for the inside of the bell mold pattern was more critical than it was for the outside. Verdin also explained that his company takes the unusual step of casting its bells upside down, for reasons that he would like to retain as a Verdin secret. And so, the decision was made to likewise print the mold patterns upside down (most of them, anyway — the Hershey Kiss mold pattern being one exception), and minimize the surface area that would have to interface with support structures.
Deposition rates and layer heights were also dialed in over the course of these first experimental prints. Because the BAAM machines use the same frame and motion control as Cincinnnati Inc.’s laser cutting system, material flow is the main driver of precision — the system is capable of achieving layer accuracy to within 0.005 inch. In most cases, Riestenberg says, this high level of accuracy is overkill for bell patterns, which are printed oversized then machined or polished to net shape.
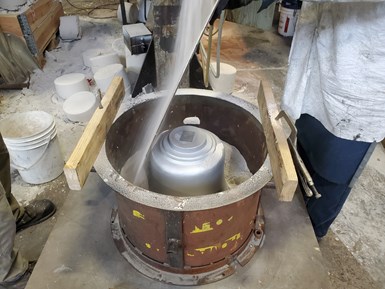
A 3D-printed bell mold pattern is placed inside a flask being filled with sand mixed with an epoxy resin. Once the sand hardens and the pattern is removed, the remaining cavity inside the flask will be filled with molten bronze to form a new bell. Photo credit: The Verdin Co.
“The plastic looks like pancake batter when it's being extruded,” Verdin says. “But what they do for us is they print our stuff to where the furthermost inner diameter and the furthermost outer diameter — the outside of those layer ridges — that is where I want my tolerances to be.” After the pattern is printed, Verdin’s team coats the entire pattern in a thinned out version of Bondo, the polyester putty from 3M that is typically used as an automotive body filler. Verdin uses a belt sander or a polisher to spin the pattern and sand it back until the very tip of the layer ridges begin to poke through. “Then I know that that's the point where I need to stop,” Verdin says. “And then we'll hit it with a couple of layers of primer and we're ready to go.”
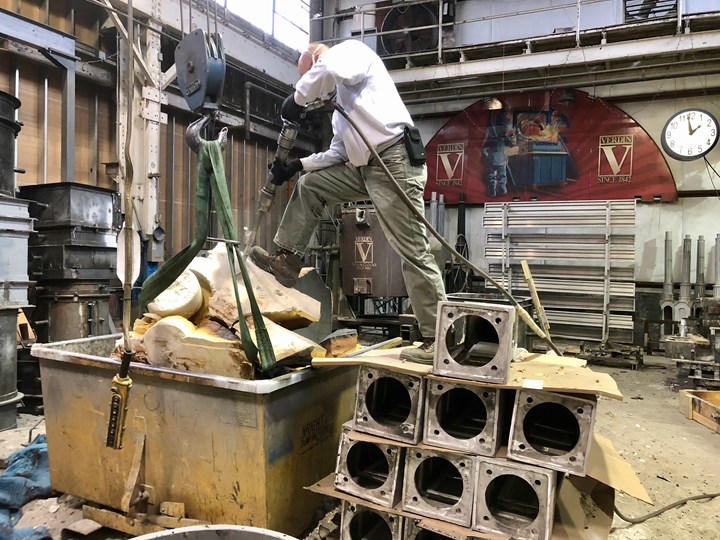
Straddling a mountain of sand casting material, a Verdin employee uses a jackhammer to free a recently cast bell from the sand and epoxy mixture. Photo credit: Brent Donaldson
The reason that the patterns are printed with oversized dimensions relates directly to the complexities involved with tuning a bell: the shape and thickness of the bell determine the notes that each harmonic partial will produce. Using oversized patterns, the bell walls are cast with extra thickness that will be removed with a manual lathe during the tuning process. “We want the patterns to be oversized, but you don't want to make it too far oversized because then it's a bunch of labor to trim it down,” Verdin says. “And you can't make it undersized because that makes the pitch of the bell too flat. I can't sharpen the bell, I can only flatten it. So that was one of our major concerns going into this. Like, yeah, I believe you when you say you can print a bell pattern for me. But can you print it to the tolerances that I need?”
“Those were the challenges in the beginning that we overcame,” Riestenberg adds. “But, as we went through the process, each new bell pattern became better and better — to the point where we were just pumping them out.”
It turns out that that ability — to pump out 3D-printed bell patterns — could produce remarkable benefits over traditional aluminum mold patterns for The Verdin Co.
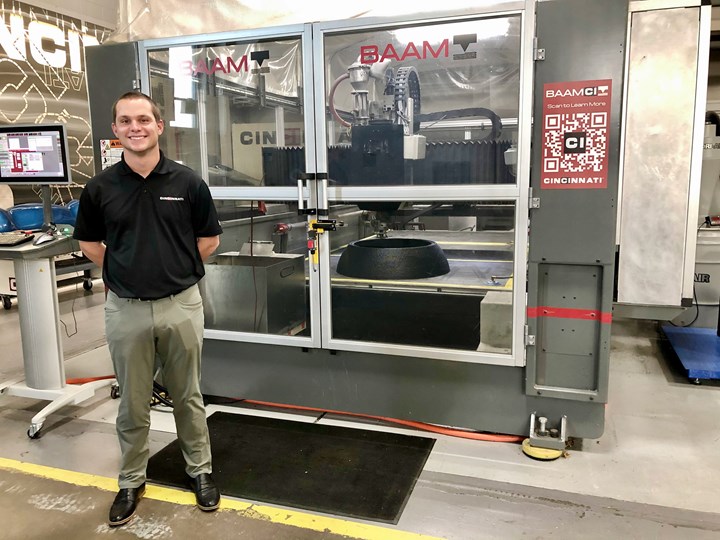
Alex Riestenberg, Cincinnati Inc.’s additive manufacturing product manager, stands in front of a BAAM machine at the company’s headquarters.
The Cost of a Kiss
Riestenberg says that he looked into the cost savings for 3D printing the Hershey Kiss bell pattern versus the traditional method. The Kiss bell ended up being roughly 38 inches in diameter. The cost for that amount of 6061-aluminum alloy that Verdin had been using for its permanent patterns would have been $19,960. The lead time would have been eight to 10 weeks, and the finish machining would have taken roughly 48 hours.
The cost of the carbon fiber used to print the final Hershey Kiss bell pattern, meanwhile, was $700, and — not counting the finishing and sanding process — took only five hours to print.
The benefit of 3D-printed mold patterns for Verdin extend beyond special one-off projects, Verdin says. First, 3D-printed patterns enable experimentation with different bell shapes and tones than aluminum patterns. Experimenting with unique shapes and tones is almost cost prohibitive with aluminum patterns. “The benefit we have with 3D printing,” Verdin says, “is that I can do lots of different shapes and sizes relatively inexpensively, because all I have to do is just change my drawing, send it over to them and they're off and running.”
A bell mold pattern being printed upside down at Cincinnati Inc. Photo credit: Cincinnati Inc.
But, more crucial to Verdin is that much of its business when it comes to bell casting is related to bell renovation. “I think the reason that we are one of the last bell foundries still standing is because of our ability to innovate and expand to branch out with what we do,” Verdin says. “For instance, if you have a 120-year-old series of chime bells, one bell is broken and you're trying to make a new bell to match it, 3D printing is great because I can print the pattern and not have to completely start from scratch,” Verdin says. “Same thing with a chime of 14 bells and someone who wants to add two bells to that chime.”
And, while they may not be as “permanent” as the aluminum patterns, Verdin also believes that the 3D printed patterns are more than sufficiently resilient, predicting that they will last for hundreds of uses. The combination of resiliency and adaptability of large-format 3D printing is convincing him that it will remain a part of Verdin’s production process.
“I think a company like ours, you get so used to doing things one way,” Verdin says. “You convince your employees that this is the only way to do it, because this is the way we’ve always done it. But just because you've done it this way for 100 years doesn't mean that that's the best way to do it anymore.”
Related Content
Next-Gen Horse Trailers to Be Built With Robotic 3D Printing
Double D Trailers is currently developing a prototype horse trailer that will be made with large-format additive manufacturing. The technology brings potential benefits for labor, weight and design features to this subset of recreational vehicles.
Read More3 Unique Elements of LFAM to Consider in Design
While similar to desktop fused filament fabrication (FFF), large format additive manufacturing (LFAM) in polymer composite poses several unique challenges as a result of its scale.
Read MoreEvaluating the Printability and Mechanical Properties of LFAM Regrind
A study conducted by SABIC and Local Motors identified potential for the reuse of scrap reinforced polymer from large-format additive manufacturing. As this method increases in popularity, sustainable practices for recycling excess materials is a burgeoning concern.
Read MoreBetter, More Compact Radio Frequency Devices Through 3D Printing
3D printing technology company Fortify is applying its photopolymer process and material developed with Rogers Corporation to serve the expanding RF market.
Read MoreRead Next
Hoosier Pattern's 3D-Printed Sand Enables Complex Castings
Rapid 2018: Hoosier Pattern’s 3D-printed sand helps foundries produce complex castings and enables low-volume production and prototyping in a range of industries.
Read MoreComparing Conventional and 3D Printing Processes for Sand Casting
New research shows surprising benefits for 3D-printed molds and cores over traditional casting processes.
Read More3D-Printed Tooling Offers Durability for Precast Concrete
As an alternative to wooden tooling, 3D-printed forms for precast concrete are proving to be more durable and better able to support a large-scale renovation project.
Read More