Wayland Additive’s Calibur3 for Stress-Free Metal Parts
Rapid + TCT 2022: The system features the NeuBeam hot part process rather than a hot bed process, which means it can efficiently create parts that are free of residual stresses because the high temperatures are only applied to the part and not the bed.
Share
Read Next
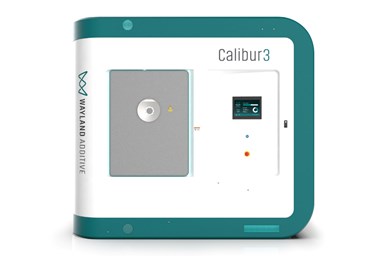
Wayland Additive’s Caliber3 metal 3D printer. Photo Credit: Wayland Additive
Wayland Additive’s Calibur3 metal additive manufacturing (AM) system which features the NeuBeam process is said to introduce a step-change in performance and capability from other metal AM machines. The company says the NeuBeam process is an entirely new, groundbreaking powder bed fusion (PBF) process that offers the opportunity to 3D print metal parts that cannot otherwise be produced due to current metal AM process limitations.
It is said the potential for new applications is greatly increased because NeuBeam offers the opportunity to use a much wider range of metal materials. It also enables the production of larger parts without having to worry about residual stress or gas cross flow and without having to pre-sinter the powder bed, the company says. The printable area of the first version of the Calibur3 system is 300 × 300 × 450 mm.
NeuBeam is a hot part process rather than a hot bed process. According to the company, this means it efficiently creates parts that are free of residual stresses because the high temperatures are only applied to the part and not the bed, ensuring free-flowing powder postbuild (no sinter cake) and stress-free parts with reduced energy consumption. In addition, the process is said to overcome many of the limitations for manufacturing large components — no residual thermal stresses, no gas cross flow and a much simplified powder removal process than existing eBeam systems.
The company says the process is capable of producing fully dense parts in a wide range of materials, many of which are not compatible with traditional eBeam or laser PBF processes, such as refractory metals and highly reflective alloys. As a result, the process is said to demonstrate vastly improved metallurgy, without many of the compromises that existing metal AM processes necessitate.
Related Content
-
DMG MORI: Build Plate “Pucks” Cut Postprocessing Time by 80%
For spinal implants and other small 3D printed parts made through laser powder bed fusion, separate clampable units resting within the build plate provide for easy transfer to a CNC lathe.
-
Video: 5" Diameter Navy Artillery Rounds Made Through Robot Directed Energy Deposition (DED) Instead of Forging
Big Metal Additive conceives additive manufacturing production factory making hundreds of Navy projectile housings per day.
-
Possibilities From Electroplating 3D Printed Plastic Parts
Adding layers of nickel or copper to 3D printed polymer can impart desired properties such as electrical conductivity, EMI shielding, abrasion resistance and improved strength — approaching and even exceeding 3D printed metal, according to RePliForm.