Uniformity Labs Qualifies Stainless Steel Powder for Binder Jetting System
The stainless steel powder is qualified on Desktop Metal’s Production System to deliver double the green strength of existing stainless steel powders over the entire build envelope.
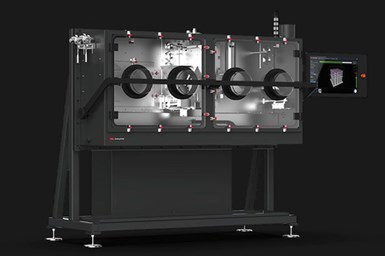
Desktop Metal’s P-1 is designed to bridge the gap between benchtop development and mass production, offering excellent part quality with enhanced process flexibility. Photo Credit: Desktop Metal
Engineered materials company Uniformity Labs has developed an ultra-low porosity 17-4PH stainless steel powder UniJet SS17-4PH performance for use on the Desktop Metal Production System. The material is designed to enable users to achieve serial production with the required repeatability and productivity.
According to Uniformity Labs, during the qualification on Desktop Metal’s Production System, the physical and mechanical properties of UniJet 17-4PH powder were evaluated and the results were outstanding. The highly uniform powder bed layering of UniJet 17-4PH delivers double the green strength and an average of 20% less shrinkage than other stainless steel powders qualified for use with Desktop Metal’s Production System. Along with the high powder bed uniformity, these factors mean better sintered part geometric accuracy and less breakage of green and brown parts during post-print handling and depowdering, resulting in high process yield at high throughput.
One of the key advantages of UniJet 17-4PH is its apparent and tapped densities, resulting in green parts with many more contact points between particles and higher density (10% reduction in relative porosity) than other standard binder jetting powders. This produces green parts with nearly twice the magnitude of transverse rupture strength across all layer thicknesses. Such green parts, alongside the very high flowability of Uniformity powder, make fabricating more complex thin-walled or heavier green parts with larger aspect ratios viable by minimizing breakage during depowdering of large, high-aspect ratio and geometrically complex parts with fine features and channels.
The company says the UniJet 17-4PH powder on the Production System consistently achieved about 25% less shrinkage in X, 19% less shrinkage in Y and almost 20% less shrinkage in Z axes than standard binder jetting powder across all layer thicknesses. The powder repeatably delivers 99-100% final part density for material properties. UniJet 17-4PH powder yielded parts with, on average, three times lower standard deviation in green density than standard binder jetting powder. This roughly translates into three times better absolute geometric tolerance in sintered parts fabricated from UniJet powder using Desktop Metal’s Production System.
The highly flowable powder improves throughput by enabling repeatable fast layering at thicker layers. At a 75-micron layer thickness and with 20% reduced shrinkage (more parts fit on the bed), users can achieve a net throughput benefit of approximately 25% relative to standard binder jetting powders for Desktop Metal’s Production System. That is said to offer a substantial cost reduction which can enable parts manufacturers to begin planning for the adoption of metal AM at scale.
At 110-micron layer thickness — while still delivering all the benefits in green strength, uniformity of powder bed and sintered density relative to standard inert gas-atomized binder jetting powders printing at 65-micron layer thickness — the throughput improvement can be more than 80%.
“The application of Uniformity UniJet 17-4 PH stainless steel for BJT delivers mechanical and process excellence for our customers who require materials that perform to the highest standards across each step of the production process,” says Adam Hopkins, Uniformity Labs founder and CEO. “Our powders deliver superior mechanical properties, printing yield and process stability, delivering repeatable production scale binder jetting.”
The powder enables more users to benefit from Desktop Metal’s high-speed metal 3D printing system for mass production. “This latest addition to our material portfolio allows us to binder jet 17-4 PH stainless steel materials critical to producing complex designs,” says Ric Fulop, Desktop Metal founder and CEO. “Binder jetting powders processed with Uniformity Labs’ technology enables unmatched mechanical properties and can further improve the economics of printing.”
- Read about Uniformity Labs’ collaboration with Desktop Metal for the qualification and delivery of ultralow-porosity binder jetting powders, which are said to enable production of high-precision parts that exhibit excellent material properties and surface finish.
- As part of the ongoing partnership, Desktop Metal and Uniformity Labs developed a fully dense, sinterable 6061 aluminum which is available exclusively to Desktop Metal customers.
Related Content
Multimodal Powders Bring Uniform Layers, Downstream Benefits for Metal Additive Manufacturing
A blend of particle sizes is the key to Uniformity Labs’ powders for 3D printing. The multimodal materials make greater use of the output from gas atomization while bringing productivity advantages to laser powder bed fusion and, increasingly, binder jetting.
Read MoreChuck Jaws Achieve 77% Weight Reduction Through 3D Printing
Alpha Precision Group (APG) has developed an innovative workholding design for faster spindle speeds through sinter-based additive manufacturing.
Read MoreFreeform: Binder Jetting Does Not Change the Basics of Manufacturing
Rather than adapting production methodologies to additive manufacturing, this Pennsylvania contract manufacturer adapts AM to production methodologies. In general, this starts with conversation.
Read MoreSinter-Based Additive Manufacturing Finds a Place Alongside MIM, Press and Sinter at APG
Powder metallurgy company Alpha Precision Group (APG) is applying a particular class of metal 3D printing technology for both rapid iteration in development and flexibility in production.
Read MoreRead Next
Bike Manufacturer Uses Additive Manufacturing to Create Lighter, More Complex, Customized Parts
Titanium bike frame manufacturer Hanglun Technology mixes precision casting with 3D printing to create bikes that offer increased speed and reduced turbulence during long-distance rides, offering a smoother, faster and more efficient cycling experience.
Read MoreCrushable Lattices: The Lightweight Structures That Will Protect an Interplanetary Payload
NASA uses laser powder bed fusion plus chemical etching to create the lattice forms engineered to keep Mars rocks safe during a crash landing on Earth.
Read More3D Printed Polymer EOAT Increases Safety of Cobots
Contract manufacturer Anubis 3D applies polymer 3D printing processes to manufacture cobot tooling that is lightweight, smooth and safer for human interaction.
Read More