Trumpf Qualifies Equispheres’ Powders for 3D Printing Systems
It is said the characteristics of Equispheres’ powders will enable Trumpf’s customers to achieve better quality parts at higher build rates.
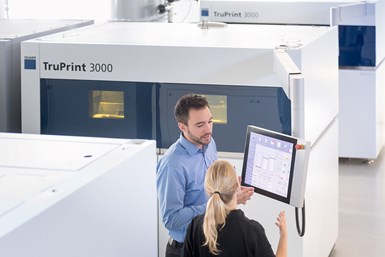
Trumpf’s TruPrint 3000 series 3D printing system. Photo Credit: Trumpf Group
Trumpf has qualified Equispheres’ AlSi10Mg powders for its TruPrint 3000 series of 3D printing systems. The companies say the qualification process confirmed that Equisphere’s aluminum materials could achieve up to a 33% faster build rate on the TruPrint system than standard aluminum powder.
It is said Trumpf will release two parameter sets for the Equispheres materials. The basic parameter set achieves 13% faster throughput than Trumpf’s standard parameters. There will also be a “productivity” parameter set that provides a 33% faster build rate, while maintaining similar tensile properties.
“We are very pleased that Trumpf has quantified the improved performance that results from the pairing of its advanced additive manufacturing equipment and our unique powder. This combination will offer TruPrint users significant productivity increases,” says Evan Butler-Jones, vice president – product & strategy for Equispheres. “This work confirms that our powders contribute to substantially better build rates when used on modern, high-quality additive manufacturing systems.”
The characteristics of Equispheres’ powders is said to enable Trumpf’s customers to achieve better quality parts at higher build rates. “By identifying this type of high-performing material and preparing the optimal parameters, we give our clients a competitive edge,” says Tobias Kiesow, a Trumpf application engineer. Kiesow notes that Equispheres’ materials also demonstrate higher density in the finished part.
Trumpf said the qualification testing was conducted at 60-micron layers and achieved build rates of 164 cm³/hr. on a dual-laser system. The company says it also expects to release parameters for using Equispheres aluminum powders on its other 3D printing systems.
The companies say that as additive manufacturing makes headway in mainstream manufacturing, there is an increased focus on production speed. “These materials and the parameters we’ve developed will help clients achieve that higher productivity level,” Kiesow says.
Trumpf’s TruPrint 3000 3D printing system uses powder-bed-based laser melting to produce parts with a diameter of up to 300 mm and a height of up to 400 mm. In the dual-laser configuration, two 500 W lasers scan the machine’s entire build chamber in parallel.
“This qualification is a significant step forward for our materials,” Butler-Jones says. “It gives part manufacturers a path to receive the maximum benefit from our superior feedstock and the support of applications engineering teams at both Trumpf and Equispheres.”
Related Content
-
Beehive Industries Is Going Big on Small-Scale Engines Made Through Additive Manufacturing
Backed by decades of experience in both aviation and additive, the company is now laser-focused on a single goal: developing, proving and scaling production of engines providing 5,000 lbs of thrust or less.
-
Video: 5" Diameter Navy Artillery Rounds Made Through Robot Directed Energy Deposition (DED) Instead of Forging
Big Metal Additive conceives additive manufacturing production factory making hundreds of Navy projectile housings per day.
-
3D Printed NASA Thrust Chamber Assembly Combines Two Metal Processes: The Cool Parts Show #71
Laser powder bed fusion and directed energy deposition combine for an integrated multimetal rocket propulsion system that will save cost and time for NASA. The Cool Parts Show visits NASA’s Marshall Space Flight Center.