Spee3D High-Velocity Phaser Nozzle for Faster Print Speeds
The company says the nozzle uses compressed air or nitrogen to deposit material four times faster than the speed of sound at much higher energy.
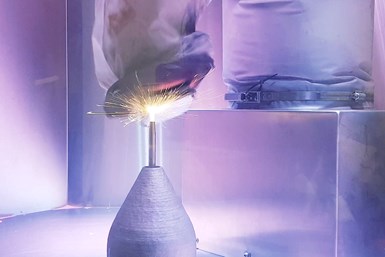
Photo Credit: Spee3D
Spee3D says its Phaser Nozzle is an ultra high-energy nozzle designed to work with the company’s cold spray metal 3D printers, a wide range of hard-phase materials and with a significant increase in deposition velocity. It is said the nozzle can create parts in just minutes to withstand severe conditions, high stress, immense shock loads and abrasive environments.
According to the company, its cold spray metal 3D printers are already some of the world's fastest, most robust, deployable additive solutions to manufacture full-density, solid metal parts in just minutes. It is said the nozzle uses compressed air or nitrogen to deposit material four times faster than the speed of sound at much higher energy. Also, this process is said to achieve high particle velocity to enable more deformation of particles during the deposition process. As a result, harder materials can be made, including stainless steel, titanium, high-strength aluminum and nickel-based carbides. These materials are in addition to Spee3D’s standard copper, aluminum bronze and aluminum materials.
It is said the cold spray process is high-speed, consistent and able to produce high-quality applications every time. The company says this technology is used worldwide and proven reliable by customers including the Australian Army, EWI, Penn State Applied Research Laboratory and other global organizations that require fabricating parts in harsh expeditionary field environments. With the Australian Army, the company has tested and validated metal 3D printing as a military capability with the latest field trial being the longest and toughest to date taking place in remote Northern Territory, alongside the Koolendong exercise.
Related Content
-
VulcanForms Is Forging a New Model for Large-Scale Production (and It's More Than 3D Printing)
The MIT spinout leverages proprietary high-power laser powder bed fusion alongside machining in the context of digitized, cost-effective and “maniacally focused” production.
-
Postprocessing Steps and Costs for Metal 3D Printing
When your metal part is done 3D printing, you just pull it out of the machine and start using it, right? Not exactly.
-
AM 101: What Is Binder Jetting? (Includes Video)
Binder jetting requires no support structures, is accurate and repeatable, and is said to eliminate dimensional distortion problems common in some high-heat 3D technologies. Here is a look at how binder jetting works and its benefits for additive manufacturing.