KBM Advanced Materials Develops GRCop-42 Powder Supply
RocketPowder was developed to meet the needs of the GRCop-42 supply chain.
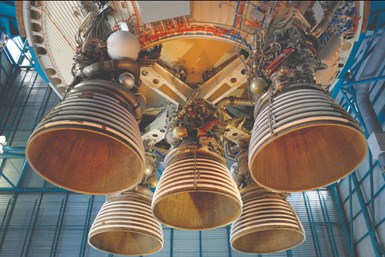
Photo Credit: iStock
KBM Advanced Materials has developed a powder supply for NASA standard GRCop-42 copper-alloy, which is made from copper, niobium and chromium. The material is well suited for space and hypersonic applications due to its high heat transfer and increased strength versus pure copper.
As a distributor of metal powders for the 3D printing and advanced manufacturing industry, KBM sources specialty powders for customers from multiple suppliers. Noticing the significant challenge to source GRCop-42, the company took on the task to develop its own reliable powder supply. KBM has formed a technical and production partnership through which a new, stable, repeatable process was developed for this specialty alloy. Taking over 9 months to perfect, this process and production relationship ensures customers will have reliable access to GRCop-42 for their own production needs.
KBM CEO Kevin Kemper is confident ‘RocketPowder’ will fill a need in the marketplace. “Our customers were continually asking for GRCop-42, to the point that we said if we can’t source it, we’ll find a partner and invest in developing a production process ourselves,” Kemper says. “This wasn’t an easy task as meeting specifications was a challenge, but we are confident we have a repeatable and reliable process, and the right production partner to provide quality powder for the highly critical needs of our space and hypersonic customers.”
The company expects to deliver multiple tons of RocketPowder per month, which will be processed, tested and packaged in Ohio, providing easy distribution for customers across the U.S. By taking final processing in-house, KBM is creating a traceable, domestic supply chain of GRCop-42. This alloy has already been shipped to a major advanced manufacturing OEM who is currently qualifying the powder.
KBM Advanced Materials specializes in financing, selling and distributing metal powder for additive manufacturing, metal injection molding and other advanced manufacturing markets. KBM has an e-commerce marketplace that bridges the inventory gap between a dispersed customer base and larger metal powder producers. This business model offers a simpler and more efficient solution to the metal powder supply chain, the company says.
- Listen to this episode of AM Radio to hear how KBM partnered with the AMGTA and Sintavia to develop a process to passivate metal condensate in a removable resin, thereby enabling safe transport and recycling.
- Read this article for more details on the AMGTA - Sintavia – KBM process to safely transport and recycle metal powder condensate waste.
- Learn more about KBM launching its metal powder distribution operations by creating a convenient e-commerce platform for customers, providing digital manufacturing with a digital marketplace for physical materials.
- This article details KBM’s creation as a distribution network aiming to be an "inventory bridge" to connect metal powder suppliers to customers in additive manufacturing, metal injection molding and more.
Related Content
-
How Norsk Titanium Is Scaling Up AM Production — and Employment — in New York State
New opportunities for part production via the company’s forging-like additive process are coming from the aerospace industry as well as a different sector, the semiconductor industry.
-
Possibilities From Electroplating 3D Printed Plastic Parts
Adding layers of nickel or copper to 3D printed polymer can impart desired properties such as electrical conductivity, EMI shielding, abrasion resistance and improved strength — approaching and even exceeding 3D printed metal, according to RePliForm.
-
AM 101: What Is Binder Jetting? (Includes Video)
Binder jetting requires no support structures, is accurate and repeatable, and is said to eliminate dimensional distortion problems common in some high-heat 3D technologies. Here is a look at how binder jetting works and its benefits for additive manufacturing.