Formlabs Launches SLA Printers, ESD Resin for Optimizing 3D Printing Workflow
The Form 3+ and Form 3B+ were designed to provide speed, quality and workflow efficiency.
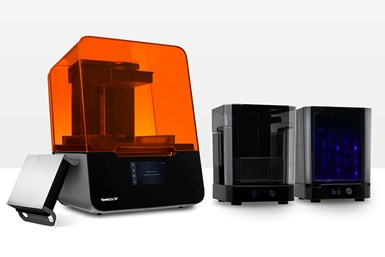
Formlabs’ Form 3+ printer is designed to produce functional, high-quality prototypes and end-use parts in record time. Photo Credit: Formlabs
Formlabs is launching its Form 3+ and Form 3B+ 3D printers, its fastest 3D printers to date featuring low force stereolithography (SLA) technology. The company says these printers feature enhanced hardware components and software updates that significantly improve print speed, print quality, support removal and provide an overall better user experience.
The Form 3+ and Form 3B+ are said to leverage powerful, higher-intensity lasers and new material settings to optimize laser exposure and print up to 40% faster than earlier models.
The launch of Form 3+ and Form 3B+ includes a next-generation Build Platform 2, which uses quick release technology and a flexible print surface to instantly release parts from the build platform, the company says. It is said users can quickly and easily remove parts from the print surface in seconds without tools, eliminating the need to scrape parts off the build platform, ultimately streamlining postprocessing efficiency and avoiding damaging parts.
Formlabs is also launching ESD Resin, the company’s first static-dissipative material, developed for applications that require ESD-safe parts to protect objects and electronics which are sensitive to unregulated static discharge. This resin is said to open up new 3D printing applications in electronics manufacturing, automotive and aerospace industries with a tough, high-quality, ESD-safe material.
Related Content
-
Louisville Slugger Uses Formlabs Technology to Accelerate Innovation
Louisville Slugger relies on Formlabs’ Form 3 stereolithography 3D printer to create both prototypes and manufacturing aids for designs of the composite and aluminum bats swung by youth and collegiate players.
-
Students Use Micro Metal 3D Printing for ISS Microgravity Experiment
Qualified3D printed lattice parts for the students using microstereolithography (micro SLA), which seemed to be the only process able to produce the parts with sufficient accuracy.
-
3D Systems’ PSLA 270 Creates Midsize, Production-Grade Parts Combining SLA Print Reliability
IMTS 2024: The PSLA 270 is engineered to deliver larger end-use parts more rapidly than similar platforms, bringing tremendous advantages for a breadth of industrial and health care applications.