Farsoon’s LPBF Systems for Large-Scale Metal Additive Manufacturing
The FS621M Pro-4, FS621M Pro-6 and FS621M-U-4 systems are said to offer huge potential in aerospace applications by lowering operational cost and enabling true industrial-scale series manufacturing.
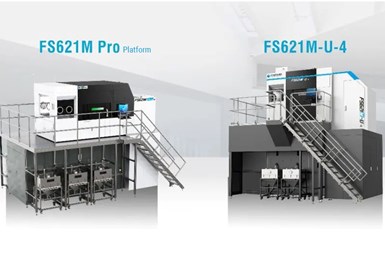
Farsoon’s FS621M Pro Platform and FS621M-U-4 multilaser, large-format metal additive manufacturing systems. Photo Credit: Farsoon
Farsoon’s latest metal additive laser powder bed fusion systems (LPBF) include the FS621M Pro-4, FS621M Pro-6 and the FS621M-U-4, which are available to the AMEA and U.S. market for pilot customer application. These multilaser, large-format metal platforms are targeted for high-speed production of high-quality large-scale additive manufacturing (AM).
These new systems are said to offer huge potential in aerospace applications by lowering operational cost and enabling true industrial-scale series manufacturing.
The large-frame FS621M has a build volume of 620 × 620 mm² with a height of 1,100 mm. This metal system is said to offer unparalleled production for large-scale applications that favor higher Z axis.
Farsoon further developed the FS621M Pro and FS621M-U-4 platforms for even higher build volume fabrication and batch production capabilities with materials such as titanium alloys, aluminum alloys, nickel-based superalloys, stainless steels and maraging steels.
The FS621M Pro Platform features a build volume of 620 × 808 × 1,200 mm with a 30% extension in Y direction compared to the standard FS621M. It can be equipped with 4 × 500-watt or 6 x 500-watt lasers to boost productivity for series manufacturing.
Farsoon’s FS621M-U-4 features a build platform size of 620 × 620 mm and a vertical axis of 1.7 meter (a 54% increase in Z height compared to the standard FS621M). It has a build volume of 653 Liters – one of the largest in the metal laser sintering market, the company says. The Z height and fiber lasers are said to enable many new possibilities in large-scale industrial applications.
The advanced multilaser scanning strategy is designed to enable high calibration accuracy in overlapping areas, ensuring uniform mechanical properties and surface finish of the parts throughout the build platform. In addition, the build process control, real-time recording and monitoring capabilities ensure optimal build quality.
To further enhance productivity and quality, the FS621M Pro Platform and FS621M-U-4 can be equipped with a permanent filter module enabling long-term operation for extremely large builds. The powder handling processes of the two 621M systems share a common powder container design, offering continuous feeding of powder to the build and the ability to easily exchange and monitor powder quality.
Related Content
-
3D Printed NASA Thrust Chamber Assembly Combines Two Metal Processes: The Cool Parts Show #71
Laser powder bed fusion and directed energy deposition combine for an integrated multimetal rocket propulsion system that will save cost and time for NASA. The Cool Parts Show visits NASA’s Marshall Space Flight Center.
-
How Machining Makes AM Successful for Innovative 3D Manufacturing
Connections between metal 3D printing and CNC machining serve the Indiana manufacturer in many ways. One connection is customer conversations that resemble a machining job shop. Here is a look at a small company that has advanced quickly to become a thriving additive manufacturing part producer.
-
DMG MORI: Build Plate “Pucks” Cut Postprocessing Time by 80%
For spinal implants and other small 3D printed parts made through laser powder bed fusion, separate clampable units resting within the build plate provide for easy transfer to a CNC lathe.