EOS M 290 1kW Metal AM System Engineered for Materials, Applications That Demand Higher Intensity
The EOS M 290 1kW metal printer features a one-kilowatt laser with the flexible, midsize frame to deliver the power needed to maximize production of industrial applications for copper and copper alloy, with more materials coming.
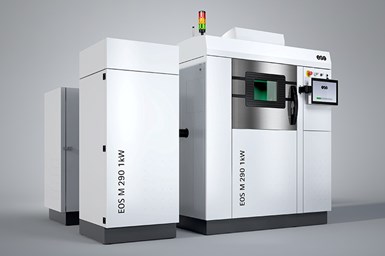
EOS M 290 1kW metal printer. Source: EOS
EOS’ M 290 1kW metal printer, part of the EOS M 290 family, is specifically designed for copper and copper alloy 3D printed applications. This laser powder bed fusion (LPBF) metal additive manufacturing (AM) platform was designed with serial production in mind, as a variant of its robust industry standard, but equipped with a 1 kW laser to handle the most challenging copper applications.
The EOS M 290 1kW was developed by EOS’ AMCM group to support the design and manufacturing of copper inductor applications and is well suited for a wide range of industries, including space, energy and mobility/transportation. These industries typically leverage copper and copper alloys, where the challenge of 3D printing copper applications (like heat exchangers and inductors) is overcome with the powerful laser and other technologies and materials working in tandem. At launch, EOS Copper CuCp and EOS Copper CuCrZr materials are fully qualified on the system, and additional materials will be added to the machine compatibility portfolio later in 2024.
“Our award-winning EOS M 290 is one of the most widely used metal AM machines in the world, and now the family is growing,” says Monica Smith, EOS metal product line manager. “Interestingly, the EOS M 290 1kW was developed by EOS’ AMCM group as part of its custom AM portfolio. The call to further commercialize this platform was exceptionally strong due to market demand, so now we are slip-streaming it into EOS’ broader portfolio.”
The high beam quality of the 1kW laser spot and the excellent detail resolution are well suited for producing highly complex components that require high intensity. With the 1,000 watts made available through this system, it is uniquely tailored to process copper applications.
The EOS 290 1kW features a build volume of 250 × 250 × 325 mm (9.85 × 9.85 × 12.8"). It has a powerful 1,000-W laser with a production volume rate of up to 55.4 (cm³/hr.), a scanning speed up to 7.0 m/sec. (23 ft./sec.) and a focus diameter of approximately 90 µm.
One early adopter of the technology was GBZ Mannheim GmbH & Co.KG, a specialized manufacturer of inductors and other highly engineered components to the automotive industry. “Additive manufacturing and the new 1 kW technology allow us to design and manufacture copper inductor applications that are more capable, durable and now produced in one piece with no soldering points,” says Thomas Corell, managing director at GBZ Mannheim. “The core elements of inductor applications are now integrated in a single build, and the results are much higher optimization of the cooling channels, lower power consumption during the product life cycle, and we are seeing great reproducibility on the production side of things.”
Related Content
-
8 Cool Parts From Formnext 2023: The Cool Parts Show #65
New additive manufacturing technologies on display at Formnext were in many cases producing notable end-use components. Here are some of the coolest parts we found at this year’s show.
-
New Zeda Additive Manufacturing Factory in Ohio Will Serve Medical, Military and Aerospace Production
Site providing laser powder bed fusion as well as machining and other postprocessing will open in late 2023, and will employ over 100. Chief technology officer Greg Morris sees economic and personnel advantages of serving different markets from a single AM facility.
-
Additive Manufacturing Versus Cavitation
The design freedom possible with laser powder bed fusion (LPBF) metal 3D printing is making it faster and easier to produce complex anticavitation devices for valves.