Airtech’s Dahltram Resins Qualified for Use on All CEAD AM Flexbot Platforms
The AM Flexbot is one of CEAD’s AM solutions, using Comau robots directly controlled by Siemens Sinumerik. It offers an option to combine 3D printing and milling into one automated process.
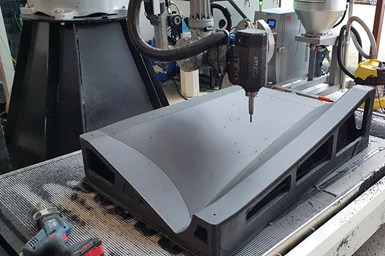
The company says Dahltram resins in use on AM Flexbot platforms offer high performance and flexibility across industries. Photo Credit: Airtech Advanced Materials Group
Airtech Advanced Materials Group partnered with CEAD to expand its offering with a line of technologically advanced and reliable resins for use in additive manufacturing (AM). In a newly developed partnership, CEAD — a technology supplier of 3D printing equipment for large-scale composite AM — has qualified Airtech’s Dahltram resins for use on CEAD’s AM Flexbot platforms. With good process knowledge, application requirements and production performance, Dahltram resins in use on AM Flexbot platforms offer high performance and flexibility across industries, the company says.
The AM Flexbot is one of CEAD’s AM solutions, using Comau robots directly controlled by Siemens Sinumerik. It offers an option to combine 3D printing and milling into one automated process. The company says it is well suited for moldmaking and tooling applications to achieve the required surface finish. It is said the versatile system provides multiple options which can be integrated to configure the system to customers’ specific needs.
Airtech Dahltram resins are suitable for multiple print platforms, offering production flexibility with end-use material validation. The company says it has continued to demonstrate efficacy in composite fabrication with extensive autoclave cycle testing across various platforms with all materials offered. The company also says it has extensive mechanical characterization data showing the Dahltram resins are well suited for composite fabrication, as well as metal fabrication and direct-to-part applications.
This partnership is the latest in Airtech’s continued efforts to drive innovation, development and testing in the AM market.
Related Content
-
To Improve Performance of Compression Molded Composites, Add 3D Printed Preforms
9T Labs' Additive Fusion Technology enables the manufacture of composite structures with as much or as little reinforcement as is necessary, using 3D printed continuous fiber preforms to add strength just where needed.
-
Video: Reinforcing (and Joining) Parts After 3D Printing
Reinforce 3D has developed a method that can be applied to strengthen 3D printed parts by feeding continuous fiber and resin through them. The technique also enables joining parts of various materials and manufacturing methods.
-
3 Unique Elements of LFAM to Consider in Design
While similar to desktop fused filament fabrication (FFF), large format additive manufacturing (LFAM) in polymer composite poses several unique challenges as a result of its scale.