Research Partners Building World’s Largest Sand Binder Jetting Printer
3D printing provides flexibility to produce large turbine components near offshore wind projects, lowering transportation costs and offering environmental benefits.
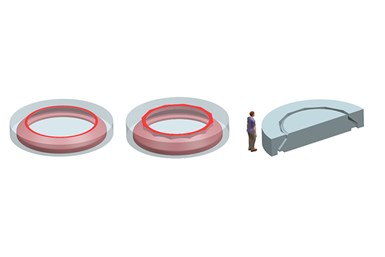
The ACC printer will be designed to print molds for key components of wind turbines, with sizes up 9.5 meters in diameter and 30 to 60 tons in weight. Image: GE Renewable Energy
GE Renewable Energy, Fraunhofer IGCV and voxeljet AG have created a research partnership to develop the world’s largest 3D printer for offshore wind applications in order to streamline the production of key components of GE’s Haliade-X offshore wind turbine. The Advance Casting Cell (ACC) 3D printer under development will benefit from financial support from the German Federal Ministry for Economic Affairs and Energy.
The printer is being designed to be capable of printing molds to cast components for the nacelle of the GE Haliade-X that can each weigh more than 60 metric tons, thereby reducing the time it takes to produce this pattern and mold from 10 weeks or more to just two weeks. In addition, the use of the 3D printer is expected to reduce the product’s carbon footprint by eliminating the need to transport the large parts from a central manufacturing location. The partners expect to launch the project during the end of 2021 with initial printer trials starting during the first quarter of 2022.
The project involves the development of a new, large-format 3D printer capable of producing sand molds for casting the highly complex metal parts of different shapes and sizes that make up an offshore wind turbine nacelle. The modular 3D printing process — which is based on voxeljet’s core binder jetting technology — can be configured to print molds for castings up to 9.5 meters in diameter and 60-plus tons in weight, dimensions.
“The 3D printed molds will bring many benefits, including improved casting quality through improved surface finish, part accuracy and consistency,” says Juan Pablo Cilia, senior additive design engineer at GE Renewable Energy. “Furthermore, sand binder jet molds or additive molds provide cost savings by reducing machining time and other material costs due to optimized design.”
The Fraunhofer Institute for Casting, Composite and Processing Technology IGCV is responsible for casting and materials technology issues as well as digital process monitoring. “We are taking a close look at thermal management during casting, and we will evaluate the ideal proportions of the printing materials,” says Dr. Daniel Günther, head of molding processes and molding materials at Fraunhofer IGCV. “Also, we will develop and test new approaches to process monitoring as part of the project.”
Related Content
-
3D Printed Cutting Tool for Large Transmission Part: The Cool Parts Show Bonus
A boring tool that was once 30 kg challenged the performance of the machining center using it. The replacement tool is 11.5 kg, and more efficient as well, thanks to generative design.
-
Do Distributors Dream of Digital Inventory? Würth Additive Group Does
It’s more than a dream for Würth Additive Group and its parent company, in fact. Along with supplying additive equipment, the group is now developing solutions for sourcing 3D printed parts in a reliable, elastic digital inventory model.
-
What Holds AM Back in Automotive Production? GM Additive Lead Describes Advances Needed
“If AM were cheaper, we would be doing more of it,” says GM’s Paul Wolcott. Various important factors relate to cost. However, the driving factor affecting cost is speed.