GKN Aerospace Successfully Tests Lightweight Turbine Rear Structure
The company says an innovative design and manufacturing of shorter, lighter turbine rear structure can contribute to lower carbon emissions.
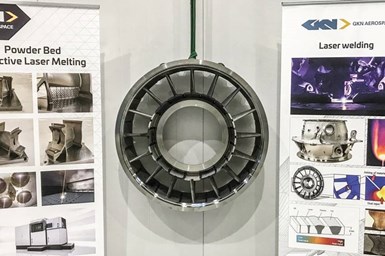
The lighter weight turbine rear structure can contribute to the engine’s lower carbon emissions. Photo Credit: GKN Aerospace
GKN Aerospace engineers in Trollhättan, Sweden, have successfully tested a new lightweight turbine rear structure (TRS) as part of the Clean Sky-2 engines research program. The purpose of a TRS is to manage the flow from the engine’s low-pressure turbine and maximize the axial thrust. It is a key component in improving the efficiency of an aerospace engine, the company says.
The company says the innovative design and additive manufacturing (AM) method results in a shorter and lighter structure compared to a traditional TRS. This was achieved by using a novel metallic alloy with higher temperature capability, as well as both metal casting and 3D-printed technology. The optimized balance between aerodynamic performance, weight and mechanical properties is said to demonstrate a significant (14%) weight reduction potential which contributes to the engine’s lower carbon emissions.
The complex component was manufactured with laser-welded assembly methods and AM technology at GKN Aerospace’s Global Technology Center in Sweden. Collaboration partners include the regional manufacturing technology center PTC/Innovatum, while aerodynamic validation took place at a test facility at Chalmers University, funded by Vinnova through the SE NFFP program. Brogren Industries (SME) — also funded by Vinnova in the national SE Innovair programme Intdemo Motor — provided supporting activities.
“At GKN Aerospace, we put a sustainable future of aviation at the heart of our business and collaboration in the aerospace ecosystems is key to achieve this,” says Henrik Runnemalm, vice president for GKN Aerospace’s Global Technology Center in Trollhättan, Sweden. “ The new TRS demonstrator is a great example of how national, regional, EU and industry-funded activities are coordinated toward final validation of an innovative concept that will contribute to our NetZero journey.”
Related Content
-
This Drone Bird with 3D Printed Parts Mimics a Peregrine Falcon: The Cool Parts Show #66
The Drone Bird Company has developed aircraft that mimic birds of prey to scare off problem birds. The drones feature 3D printed fuselages made by Parts on Demand from ALM materials.
-
Velo3D Founder on the 3 Biggest Challenges of 3D Printing Metal Parts
Velo3D CEO and founder Benny Buller offers this perspective on cost, qualification and ease of development as they apply to the progress of AM adoption in the future.
-
3D Printed "Evolved Structures" for NASA Exoplanet Balloon Mission: The Cool Parts Show #61
Generative design creates stiff, lightweight brackets for EXCITE mission monitoring planets orbiting other stars. The Cool Parts Show visits Goddard Space Flight Center.