GE Additive Partners With Sydney University on Manufacturing-Focused Research Facility
The Sydney manufacturing hub is a new manufacturing-focused research facility that will work alongside industry to deliver cutting-edge R&D in additive manufacturing and materials processing.
Share
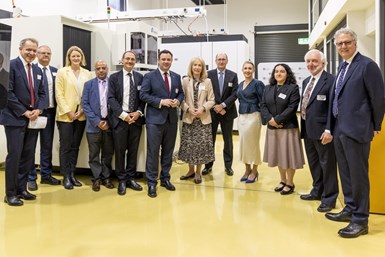
The launch of the Sydney Manufacturing Hub included the with Minister for Jobs, Investment, Tourism and Western Sydney and Minister for Trade and Industry the Honorable Stuart Ayres. Photo Credit: Bill Green/University of Sydney
The University of Sydney has opened a $25 million facility in the heart of Sydney’s Tech Central to drive innovation and foster industrial output, including a collaboration with GE Additive.
University officials say the facility is a foundational node for complementary facilities that support the NSW government’s projects at Western Sydney Aerotropolis and Western Sydney parklands. Located in the engineering precinct of the University of Sydney's Darlington campus, the Sydney Manufacturing Hub is a new manufacturing-focused research facility that will work alongside industry to deliver cutting-edge R&D in additive manufacturing (AM) and materials processing.
The facility is geared to enable concept-to-production demonstration capabilities, including advanced pre- and postprocessing of materials for faculty, students small and medium-sized companies, and, if needed, larger companies to experience and leverage metal 3D printing and advanced manufacturing — often for the first time.
The hub provides capabilities for design, topological optimization and the 3D printing of metals, ceramics and polymers, as well as postprocessing heat treatment, advanced characterization and more. It’s all designed to pave the way for new technology in industries such as aerospace, autonomous vehicles, biomedical, defense, maritime and robotics.
University of Sydney Vice-Chancellor Professor Mark Scott AO says the university has continued to demonstrate its capability as an R&D leader in the region by working closely with both the public and private sector. Scott says. “This is evidenced not only through the establishment of this new research facility but also via our collaborative projects in Greater Sydney, particularly the Western Sydney Parklands and Aerotropolis,” Scott says.
The facility will provide specialized consulting, fabrication activation and training to its industrial partners, providing both guided and autonomous access to the facilities for the purposes of testing, research and fabrication. One partner is GE Additive, which entered into a strategic five-year agreement with the University in 2020 to advance Australia’s manufacturing capability. The University of Sydney and GE Additive are collaborating on R&D topics focused on materials with experimental work performed at the new facility.
The hub is designed to accommodating GE Additive’s state-of-the-art metal printing technologies and will serve as a technology demonstration center for GE Additive across Australia and New Zealand, including hosting workshops, training and collaboration sessions for industry.
Related Content
-
Titanium Golf Club Line Leverages AM to Boost Clubhead Performance
Japanese lifestyle golf brand Designer utilizes Farsoon 3D printing to optimize the design and production of its latest titanium golf club line.
-
4 Weeks from Design to Molded Part for Medical with Metal 3D Printed Tooling
Mold builder Westminster Tool applied the Trueshape process from Mantle to produce tooling to take a medical device from prototype mold to full-scale production in a matter of weeks.
-
IndyCar's 3D Printed Top Frame Increases Driver Safety
The IndyCar titanium top frame is a safety device standard to all the series' cars. The 3D printed titanium component holds the aeroscreen and protects drivers on the track.