Esprit Collaboration with CETIM Aims at Binder Jetting Technology
Esprit’s additive suite products improve interoperability between software and machines for binder jetting.
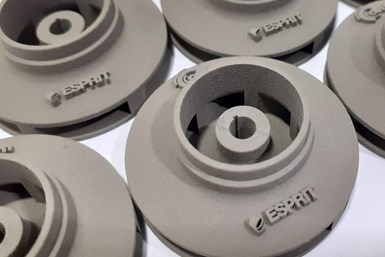
By preparing data in Esprit Additive Suite products, CETIM was able to build a job made of six impeller parts with a binder jetting machine.
Esprit CAM, a computer-aided manufacturing software that supports a variety of CNC machines, has expanded its partnership with France’s Technical Centre for Mechanical Industry (CETIM) to include additive manufacturing (AM). CETIM was established in France in 1965 in order to improve companies’ competitiveness through mechanical engineering, transfer of innovations and advanced manufacturing solutions.
AM creates parts in 3D, breaking out limits and supplementing historical manufacturing processes. AM technology is made of several sub-technologies. Esprit has supported two of those, direct energy deposition (DED) and powder bed fusion (PBF), with products that have been tested and validated by industrial partners.
In 2020, Esprit continued to develop products to expand its support of additive technologies. It released a new feature which adds support to several new slice formats such as 3MF and Binary CLI, improving interoperability between software and machines. Binder jetting uses a liquid binding agent to bind powder particles one layer at a time until the final product is complete or printed.
In collaboration with CETIM, Esprit teams validated the support of a third AM technology — binder jetting. By preparing data in Esprit Additive Suite products, CETIM was able to build a job made of six impeller parts with a binder jetting machine from Sweden’s Digital Metal.
“We used the Esprit Additive PBF product to slice the 3D model and produce a compatible file format that would be readable by Digital Metal’s machine,” says Clement Girard, Esprit’s additive product manager. “All data preparation was done using a version of Esprit Additive PBF that’s still in development.”
Although Esprit Additive support for binder jetting technology is not yet commercially available, this success demonstrates what’s possible when both teams collaborate closely.
Related Content
-
3D Printed Lattices Replace Foam for Customized Helmet Padding: The Cool Parts Show #62
“Digital materials” resulting from engineered flexible polymer structures made through additive manufacturing are tunable to the application and can be tailored to the head of the wearer.
-
3D Printed "Evolved Structures" for NASA Exoplanet Balloon Mission: The Cool Parts Show #61
Generative design creates stiff, lightweight brackets for EXCITE mission monitoring planets orbiting other stars. The Cool Parts Show visits Goddard Space Flight Center.
-
Implicit Modeling for Additive Manufacturing
Some software tools now use this modeling strategy as opposed to explicit methods of representing geometry. Here’s how it works, and why it matters for additive manufacturing.