Burloak Adds Capacity, Services with California Manufacturing Facility
Company also forms agreement with Carpenter Technology to collaborate on future product design and development opportunities.
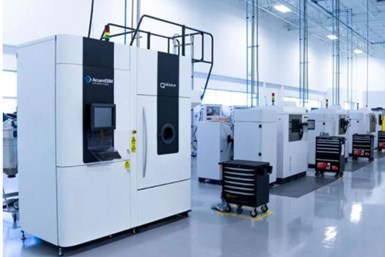
Burloak Technologies Inc. establishes second additive manufacturing center in Camarillo, California.
Burloak Technologies Inc., a division of Samuel, Son & Co., has established its second additive manufacturing (AM) center in Camarillo, California. With the addition of this facility, Burloak is said to be North America's first multisite AM services provider, offering full Design for Additive Manufacturing (DFAM) expertise at scale.
The new 25,000-square-foot (2,300-square-meter) facility augments the manufacturing capacity available at the company's 65,000-square-foot (6,000-square-meter) AM Center of Excellence in Oakville, Ontario. Between the two facilities, Burloak says it offers the industry's most complete set of AM capabilities and technologies, including laser powder bed fusion, electron beam powder bed, metal binder jet and powder, and wire directed energy deposition technologies. In addition, Burloak offers engineered plastic solutions for PEEK, Ultem, PCTG, carbon fiber and nylon-based materials using selective laser sintering and high-speed extrusion technologies. These are combined with a full range of proven materials and postproduction services, including design, engineering, CNC machining, heat treatment and finishing capabilities, the company says.
Formerly operating as CalRAM, the facility, assets and equipment have been acquired from Carpenter Technology Corp. In addition to this transaction, Burloak and Carpenter Technology have formed an agreement to collaborate on future product design and development opportunities, and Carpenter Technology will become the preferred powdered metals supplier for certain DFAM projects led by Burloak.
"DFAM expertise, combined with scalable manufacturing capacity, is often the missing link for customers seeking to embrace additive," says Colin Osborne, Samuel's president and CEO. "The establishment of our multisite capacity, along with our expanded relationship with Carpenter Technology, further demonstrates our commitment to closing this gap. By leveraging the expertise Samuel has in large-scale manufacturing, along with Burloak's deep additive experience, we offer customers the easiest, most direct path to develop and scale even their most complex additive manufacturing projects."
Related Content
-
Machine Tool Drawbar Made With Additive Manufacturing Saves DMG MORI 90% Lead Time and 67% CO2 Emission
A new production process for the multimetal drawbar replaces an outsourced plating step with directed energy deposition, performing this DED along with roughing, finishing and grinding on a single machine.
-
ActivArmor Casts and Splints Are Shifting to Point-of-Care 3D Printing
ActivArmor offers individualized, 3D printed casts and splints for various diagnoses. The company is in the process of shifting to point-of-care printing and aims to promote positive healing outcomes and improved hygienics with customized support devices.
-
With Electrochemical Additive Manufacturing (ECAM), Cooling Technology Is Advancing by Degrees
San Diego-based Fabric8Labs is applying electroplating chemistries and DLP-style machines to 3D print cold plates for the semiconductor industry in pure copper. These complex geometries combined with the rise of liquid cooling systems promise significant improvements for thermal management.