Bell Textron, Ingersoll Machine Tools Produce 3D Printed Rotor Blade Trim Tool
Collaborative effort successfully manufactured a 22-foot-long vacuum trim tool for production of main rotor blade components.
Share
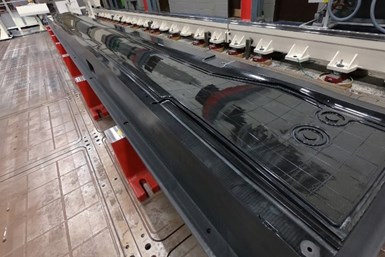
Finished machined and vacuum-sealed tool.
Ingersoll Machine Tools Inc. and Bell Textron Inc. successfully utilized a large-format 3D printer to manufacture a 22-foot-long vacuum trim tool for production of main rotor blade components. The effort utilized Ingersoll’s hybrid large-format MasterPrint gantry-type 3D printer and five-axis milling machine housed at Ingersoll’s headquarters in Rockford, Illinois.
“We are continuously testing and advancing MasterPrint in our Development Center,” says Chip Storie, Ingersoll CEO. “Among Ingersoll’s short-term objectives is for MasterPrint to 3D print molds for aerospace that preserve the geometrical properties and tolerances, vacuum integrity and autoclave resilience normally obtained with traditional technology, but with the cost and time reduction only additive manufacturing (AM) can offer.”
This production tooling effort 3D printed 1,150 pounds of ABS material with 20% chopped carbon fiber fill. The printing process was completed as a single part in a continuous 75-hour operation. After printing, the mold surfaces and tooling location features were machined to finished dimensions by exchanging the print module for the five-axis milling head which is changeable on the MasterPrint machine. The machining was completed in one week and the final part achieved full vacuum tightness. The Ingersoll machine utilizes the Siemens 840D CNC control system for controlling both the machining and the 3D printing.
Critical time savings was achieved through the 3D print fabrication and efficient five-axis machining operations. The additive and subtractive manufacturing processes were seamlessly co-engineered in the native CAD software format, the company says. The traditional build cycle for a typical mold in aluminum such as this using standard methods is typically 4 to 5 months. This manufacturing process was completed in a matter of weeks.
Utilizing this rapid manufacturing equipment will enable Bell to greatly accelerate its development of tooling for many applications, the company says.
Related Content
-
Video: For 3D Printed Aircraft Structure, Machining Aids Fatigue Strength
Machining is a valuable complement to directed energy deposition, says Big Metal Additive. Topology-optimized aircraft parts illustrate the improvement in part performance from machining as the part is being built.
-
Sustainable Furniture Company Model No. Maintains Product Focus with Switch from DIY to Industrial 3D Printers
The startup founded in 2018 has matured in its product offerings as well as its manufacturing equipment, moving from homegrown 3D printers to industrial large-format machines.
-
3D Printing Brings Sustainability, Accessibility to Glass Manufacturing
Australian startup Maple Glass Printing has developed a process for extruding glass into artwork, lab implements and architectural elements. Along the way, the company has also found more efficient ways of recycling this material.