Why GM’s Electric Future Is Also an Additive Future
Production capacity isn’t the only reason that additive has been slow to make inroads into the automotive industry. There is a larger barrier to entry—one that General Motors and Autodesk are working to overcome.
Share
For this automotive seat bracket, engineers at General Motors and Autodesk used the latter company’s cloud-based generative design technology to consolidate what had been an eight-component assembly into a single piece. This proof-of-concept, 3D-printed seat bracket is 40 percent lighter and 20 percent stronger than the original part. Photos: Autodesk
On May 3 of 2018, General Motors (GM) made an announcement that pierced the news cycle. The auto giant had entered into a “multi-year alliance” with the San Francisco Bay-area software company Autodesk, and engineers from each company had jointly created a proof-of-concept, 3D-printed seat bracket that was 40 percent lighter and 20 percent stronger than the original part.
[UPDATE: Find our more recent articles on additive manufacturing for electric vehicles and about GM’s advances in additive manufacturing]
The news generated a media blitz. Dozens of publications, from this one to WIRED Magazine, reported on this oddly shaped, table-lamp-sized seat bracket—and for good reason. Not only was the bracket stronger and lighter than its traditionally manufactured counterpart, but GM’s engineers—aided by Autodesk Fusion 360’s cloud-based generative design technology—consolidated what had been an eight-component assembly into a single piece.
For more than a century, weight reduction for automotive parts—when sought at all—has been an incremental process. Lightweighting a single part by 40 percent is unheard of. The same can be said for consolidating the bracket’s eight assembly components into one piece. General Electric’s 3D-printed LEAP engine fuel nozzle is the most famous example of an assembly consolidation made possible by AM. A corollary breakthrough for the automotive industry, where parts are produced annually by the hundreds of thousands, would be auspicious news indeed.
Adding mileage to GM’s announcement was a photo of the seat bracket itself—a gracefully designed lean metal object with interconnected sweeping lattice structures. It’s a functional sculpture, aesthetically crossed between a robotic hip joint and Art Nouveau.
Yet for all of this innovation, it’s hard to ignore that GM’s 3D-printed seat bracket is still a proof-of-concept part. Now entering a second round of design iterations (to achieve even greater weight savings), the part is likely to be tested first in high-end motorsports vehicles before it winds up in GM’s consumer fleet.
But between the lines of GM’s press release there is another story, and it foretells changes coming to the industry very soon that are very large. While each of the Big Three automakers races toward an all-electric future where generative design and additive manufacturing dominate, General Motors is betting that victory is achieved not only through faster printers, but through a reimagined digital workflow. The bet that General Motors seems to be making is that, by the time its engineers perfect a new process flow between generative design, setup for additive manufacturing and simulation testing—a process they’re refining right now with Autodesk engineers who are embedded with GM—the value proposition and throughput capacity for metal AM will enable mass production.
If GM is right, this is how the internal combustion engine ends. Not with a bang, but with 150 AI-fueled design iterations of a 3D-printed seat bracket.
Engineers in the Keep-Out Zone
Perhaps more than any other automaker, GM has embraced additive manufacturing since 3D printing’s inception. The company says that it purchased the first available “rapid prototype machines” in the 1980s and has since installed more than 50 machines that have produced hundreds of thousands of 3D-printed prototype parts in the last decade alone. But it’s been under the direction of Mary Barra, CEO since 2014, that the company’s leadership has strengthened relationships with top AM industry players. Two years ago, GM sent a handful of its design engineers to Silicon Valley on an exploratory mission into additive technologies. Some of those engineers were embedded for two weeks at Autodesk’s Pier 9 Technology Center in San Francisco, where they took a crash course on how to use and integrate Autodesk’s Fusion 360 generative design capabilities into GM’s operations.
The benefits of this relationship between GM and Autodesk are mutual. This October, Autodesk announced that it had consolidated all of its Fusion 360 tiers for generative design, advanced simulation and five-axis machining into a single product. Whether that was a coincidence, coming as it did on the heels of the two companies formalizing a multi-year collaboration this past January, is hard to say. But based on conversations I had with design and engineering leaders at both GM and Autodesk, the integration of generative design through final simulation was exactly what GM was seeking.
But generative design entails a different kind of thinking. It involves not modeling geometry directly, but setting inputs around constraints so software can propose the geometry.
GM says that it has reduced a total mass of 5,000 pounds across 14 of its vehicle models since 2016. Citing material and technology advancements, the company says that most of those models shed more than 300 pounds. The 2019 Chevrolet Silverado alone is 450 pounds lighter than the 2018 model. Kevin Quinn, GM’s director of additive design and manufacturing, says that it’s only a matter of time before generative design and additive manufacturing are the primary technologies driving these lightweighting efforts. Using the seat bracket as an example, Quinn compares traditional lightweighting to how the company is approaching the future.
“Traditionally, we would start with the last version’s model, maybe tweak it a little bit and come up with two or three design iterations,” he says. “We might achieve a five percent mass saving and make it a little stronger.” But generative design entails a different kind of thinking. It involves not modeling geometry directly, but setting inputs around constraints so software can propose the geometry. He says this starts with the “hard points” for the bracket design, the regions of the part where material is necessary and needs to conform to specific requirements. “Areas where the bracket attaches to the floor, for instance, or where the seat buckle attaches to the bracket,” he says. “So you set those hard points and say, ‘I have to have material here, in this shape, on the entire side, and that attachment point has to be this big.’”
Static load requirements are then programmed where those hard points attach to other parts or assemblies. Engineers then input data for the surrounding components, such as the floor, the seat and the plastic trim bezel that covers part of the bracket. These are the keep-out zones, the areas where the software knows that material is not allowed. Finally, designers input data regarding the additive setup itself, primarily around build orientation, support structures, and any extra material that might be needed to enable postprocessing such as five-axis machining.
Throughout all of these steps, engineers can manipulate materials to test for performance across each new iteration.
“You're not getting rid of the engineer in this process,” Quinn says. “What you're doing is giving that person a broader design space and more options to consider. In the traditional design scenario, maybe we iterate from the last version of that seat bracket and maybe we get two or three different iterations to choose from. Using generative design for the seat bracket, we asked ourselves what the most important criteria was. We could’ve chosen stiffness, but we said our number one priority is to get the lowest mass that we could test in our simulation model—because it’s got to still pass our requirements when we run into through crash simulations and other tests.”
The Coming Fleet of EVs
On October 2 of last year, General Motors’ executive vice president Mark Reuss said that GM believes its future will be 100 percent electric. The statement, which did not include a timeline, put GM in line with other traditional auto manufacturers that are publicly committing to an electric future. And committing they are. Last year, Ford announced its plans to invest $11 billion in electric vehicles (EVs) by 2022 and increase its fleet of hybrids and EVs to 40. The company vowed to cut $14 billion in costs, predominantly from the production of sedans and internal combustion engines. Volkswagen is investing $20 billion in electric vehicle technology and says that every model across its multi-brand lineup will include an electric powertrain option. Porsche’s CEO expects that its vehicle models will be all-electric by 2030. And Volvo is moving even more quickly, stating that “every new Volvo introduced” from 2019 forward will be hybrid or electric only.
International commitments to reduce emissions and ban gas- or diesel-powered engines are intensifying pressures on automakers. Great Britain, France, Germany and India are taking a range of actions that including banning the internal combustion engine within the next 25 years and investing heavily in charging infrastructure. In Norway, about 40 percent of cars sold today are already zero-emission vehicles, and the country aims to increase that number to 100 percent by 2025. China, the world’s largest car market, recently passed a cap-and-trade credit program for electric cars that progressively punishes automakers who continue to sell gas- or diesel-powered vehicles. And while the United States is, at the time of publication, on the verge of rolling back the federal Corporate Average Fuel Economy standards, American automakers may have traveled too far toward a low-emissions and EV future to turn back.
Consider that General Motors currently offers just one hybrid electric car, the Chevy Volt—which GM will stop producing by the end of 2019—and one extended range all-electric vehicle, the Chevy Bolt EV. As this article went to press, GM announced that it was realigning its manufacturing capacity and closing several plants in the U.S. and abroad. Explicit in the announcement was that the company intends to invest heavily in EVs. Indeed, by 2023, the company plans to offer “at least 20” electric battery and fuel cell vehicles to its global lineup, including two new models in the next 15 months.
What does all this mean for additive manufacturing? What is the connection between EVs and AM? The answer—or one of the answers—is mass.
Charging infrastructure notwithstanding, the two major obstacles to electric vehicle ubiquity in the U.S. have been cost and the limited range on a single charge. Lightweighting by printing parts is seen as the key to overcoming both of these obstacles. Still, for GM’s seat bracket, the generative design process resulted in 150 iterations of the part, and narrowing the selection down to a single part wasn’t simply a matter of choosing the lightest option. Aesthetics, manufacturability and the results of simulation tests all played a role in the process. The design that GM selected out of those 150 iterations was light, but not the lowest weight option.
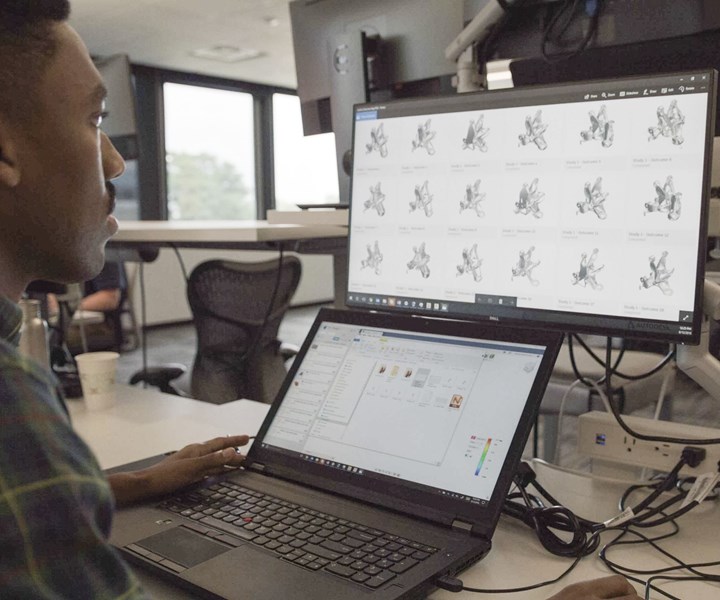
The generative design process for GM’s seat bracket resulted in 150 design iterations of the part. Those iterations are the result of setting inputs around constraints so Autodesk’s software can propose the geometry. This started with the “hard points” for the bracket design—the regions of the part where material needs to conform to specific requirements. Other inputs included static load requirements, input data for the surrounding components (aka the keep-out zones where material is not allowed) and data regarding the additive setup itself, primarily around build orientation, support structures and any extra material that might be needed to enable postprocessing.
The connection between EVs and AM exists in part because an entirely new vehicle type affords the opportunity for a new, more versatile, more streamlined approach to manufacturing. To fully capitalize on future technology developments, changes in habits and thinking need to happen first. And those changes are why, at least for the foreseeable future, Mike Grau is embedded with General Motors.
A New Workflow for Automotive
Grau is one of Autodesk’s project and team managers for its advanced consulting team in the Americas. He’s also one of Autodesk’s engineers who, for the last year, has been stationed at the General Motors Technical Center in Warren, Michigan. Grau, whose background is in simulation and CAD for the auto industry, thinks that even if additive machines could handle volume requirements for automotive, today’s engineers would still find it hard to break free from workflow routines they are used to. It’s Grau’s job to work with GM’s engineers to refine the process of designing a CAD model, creating the setup for additive manufacturing, then converting that model to import into simulation.
“You need to have an overview of the entire workflow,” Grau says. “It's not really one discipline you need to be a specialist in. My role is managing the project and helping GM to create and explore these different disciplines—to create a flawless design workflow going from CAD to additive to simulation.”
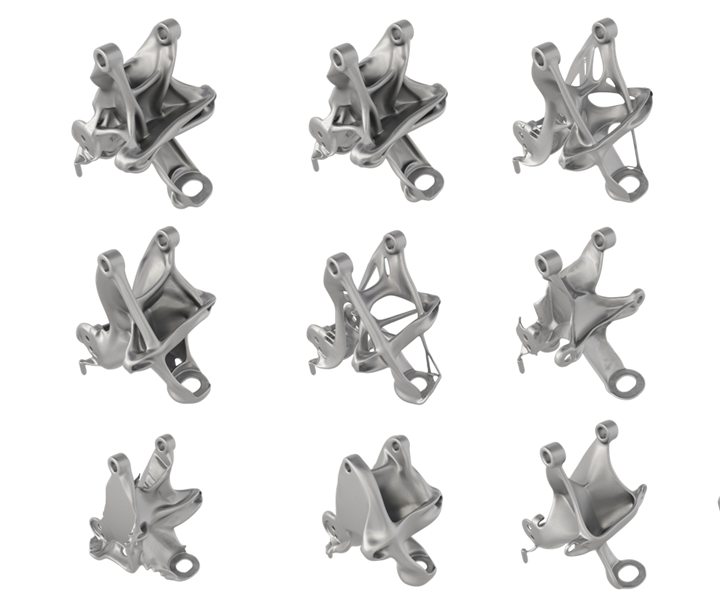
A closer look at some of the 150 design iterations for GM’s 3D-printed seat bracket. Kevin Quinn, GM’s director of additive design and manufacturing, says that engineers will be critical to the generative design for additive manufacturing process. “What you're doing is giving that person a broader design space and more options to consider. Using generative design for the seat bracket, we asked ourselves what the most important criteria was… (And) we said our number one priority is to get the lowest mass that we could test in our simulation model.”
Grau says that simulation for generatively designed parts still poses a major challenge. “We can create a great structure. We can create beautiful, latticed, lightweight products, but it’s very tricky to put them in a crash simulation,” he says. “And that is not an Autodesk problem. That's an industry problem. It's pretty much a physical and mathematical problem. The aviation industry more often runs static stress analyses because a plane doesn't crash, ideally.”
This is key to why the aerospace and aviation industries have adopted additive and generative design faster than automotive, according to Grau. “In an automobile you have multiple load cases that are not considered by the aviation industry. When you talk about crash simulation, [federal] requirements, squeak and rattle requirements, all the designs you create in that workflow have to be ready to pass simulation tests,” he says. “That makes it much harder for us to create workflows that can be integrated by OEMs.” Grau adds that Fusion 360’s new additive- and simulation-specific features are meant to vastly speed up the workflow process, something that both companies are learning and refining together.
“What we’re doing now is taking example designs from GM and running these designs through a new workflow,” Grau says. “So we set up the generative part, create the first generative outcome, then we optimize this outcome for an additive manufacturing process. We then take that back and run nonlinear or crash simulations on these parts.” Grau and the GM engineers will look at multiple materials and multiple safety factors, including the location and magnitude of load constraints. “What we’re learning from GM around design is helping us to optimize the workflows in our software. And the GM engineers benefit from us because they learn how our software works. It is really a constant development of workflows together. A symbiosis.”
The 3D-printed seat bracket on the right is 40 percent lighter than its conventional counterpart on the left, and reduces an assembly of eight pieces down to just one. The workflow used to create this GM part holds promise for the future of automotive manufacturing.
Grau acknowledges that lightweighting through generative design and additive manufacturing will be relegated to high-performance motorsports vehicles in the short term. So, when will generative and additive be ready for consumer automotive production?
“I don't have to speculate,” he says. “It is already there. The only thing holding us back, at least for the most part, is the efficiency of the process to get there. Until now the design and simulation processes have taken a long time. They’ve involved a lot of manual work by the engineer. While additive is still evolving, the software needs to adapt and shape the process. But we're engineers. We can do it.”
Additive Manufacturing for Electric Vehicles
Electrification brings a blank slate to the vehicle manufacturing process, providing inroads for additive manufacturing to potentially fill production needs. Explore AM for EV
Related Content
3D Printing with Plastic Pellets – What You Need to Know
A few 3D printers today are capable of working directly with resin pellets for feedstock. That brings extreme flexibility in material options, but also requires greater knowledge of how to best process any given resin. Here’s how FGF machine maker JuggerBot 3D addresses both the printing technology and the process know-how.
Read More3D Printed Titanium Replaces Aluminum for Unmanned Aircraft Wing Splice: The Cool Parts Show #72
Rapid Plasma Deposition produces the near-net-shape preform for a newly designed wing splice for remotely piloted aircraft from General Atomics. The Cool Parts Show visits Norsk Titanium, where this part is made.
Read MoreAt General Atomics, Do Unmanned Aerial Systems Reveal the Future of Aircraft Manufacturing?
The maker of the Predator and SkyGuardian remote aircraft can implement additive manufacturing more rapidly and widely than the makers of other types of planes. The role of 3D printing in current and future UAS components hints at how far AM can go to save cost and time in aircraft production and design.
Read MoreBeehive Industries Is Going Big on Small-Scale Engines Made Through Additive Manufacturing
Backed by decades of experience in both aviation and additive, the company is now laser-focused on a single goal: developing, proving and scaling production of engines providing 5,000 lbs of thrust or less.
Read MoreRead Next
Watch: Additive Manufacturing Workshop for Automotive Video Available
Watch the full program of the inaugural Additive Manufacturing Workshop for Automotive, and learn how automotive manufacturers are using 3D printing in production.
Read MoreAdditive Manufacturing Is Succeeding in Production! Here Are Examples
We are no longer predicting that additive manufacturing will be used in production — because it already is. Find real stories of 3D printing for full production at AM's leading edge in this collection.
Read MorePostprocessing Steps and Costs for Metal 3D Printing
When your metal part is done 3D printing, you just pull it out of the machine and start using it, right? Not exactly.
Read More