The Ohio State University’s metal additive manufacturing lab has 35 engineering students involved in laser powder bed fusion, binder jetting, ultrasonic additive manufacturing and other metal AM processes, though not as part of any AM degree program.
The students are employees of the lab. They are mostly undergraduates.
And the lab itself has what would seem to be as many or more metal AM modalities than any other university facility. In addition to the capabilities listed above, others include electron beam melting (EBM), powder-fed directed energy deposition (DED) and wire arc additive manufacturing (WAAM).
All of this has come since 2017. Former Director of Additive Manufacturing Ed Herderick led the facility through its conception and launch, and was leading it when I visited earlier this year. Unknown to me, I was visiting at a transitional moment. Herderick left the position; new director John Middendorf has been announced. What follows is based on my conversation with the previous director. Herderick says the university invested in none of its metal AM machines — the 12 metal 3D printing systems in the lab, from eight different AM technology providers, all came via donation, consignment or grant — but the university did invest in the staff and facility sufficient to receive a donated or consigned machine without any added expense for the originating company. Thus, standing in the lab and describing the range of machines, he was able to say, “You’re looking at about $11 million worth of equipment from outside and seven figures of facility investment from us.”
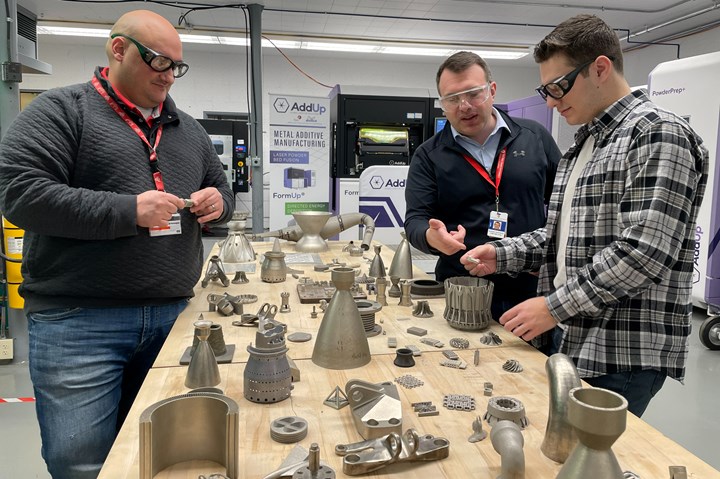
AM Technology Leader Ben DiMarco and former Director of Additive Manufacturing Ed Herderick (left and center, respectively) speak with mechanical engineering undergraduate student Justin Levy. Twenty undergrads gain valuable experience in AM by serving as part-time employees in the lab.
The lab performs research focused on production and industrialization of metal 3D printing capabilities. AM Technology Leader Ben DiMarco oversees this work and the operation of the equipment. He says the combination of major funding via grants aimed at defense and energy-sector research, plus smaller grants from companies, means there is about $100,000 worth of active projects in work within the lab at any given time.
The undergraduate students staffing the lab each work 15 hours per week. The employment is paid, and where degrees in AM tend to be at the graduate level, the work in the OSU lab gives undergrads more direct practical experience with metal AM than many graduate students studying the technology.
During my visit, the work I was able to see involved ultrasonic AM and laser powder bed fusion in combination, the application of annulus-shaped rather than spot-focused lasers, and test specimens for comparing the mechanical properties of various lattice designs. The work done with and for individual companies tends to be proprietary, but this work also represents an important value of the lab.
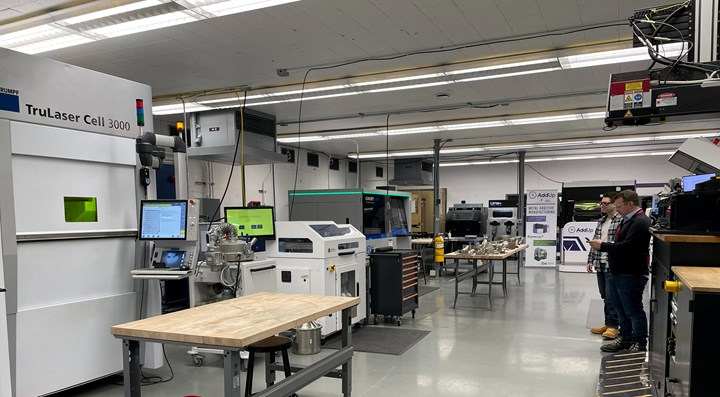
All the lab’s metal AM machines came via donation or grant, or are here on consignment. Machines visible in this photo come from Trumpf, ExOne (now Desktop Metal), GE Additive, Open Additive, Addup and (both just barely visible at extreme right) EOS and Aconity3D. Another OSU metal AM machine not visible here comes from Fabrisonic. In addition, a wire-arc additive manufacturing system using an industrial robot was built in-house.
Herderick gives an example of a company that saw the value of additive for its production, but was challenged with getting started. He says, “They worked with us initially just by coming here, standing beside Ben, and watching what he was doing. Then they rented time on a machine. Now, they are in the process of buying their own machine.”
DiMarco adds, “They did crawl-walk-run really well.” The first step is often what is missing. With facilities like the OSU lab offering a way for manufacturers to attain a low-stakes entry to additive, he says, “We can make it so the way forward can start with crawl and doesn’t have to be just walk-run.”
Related Content
DMG MORI, Illinois Tech to Establish National Center for Advanced Manufacturing in Chicago
The center will focus on workforce training for additive manufacturing and related advanced manufacturing industries.
Read MoreEOS Additive Minds Academy Opens Space for Hands-On AM Training
The engineering, consulting and education arm of EOS has offered training in various capacities before now, but a new physical footprint at the company’s Novi, Michigan, facility will make AM training more accessible and affordable.
Read MoreASTM and EOS Expand AM Machine Operator Certification Program
The ASTM International Powder Bed Fusion – Laser Beam (PBF-LB) Machine Operator Certification program now includes both the EOS M 290 and EOS M 400 platforms.
Read MoreRenishaw Joins Additive Manufacturing Coalition to Support Advocacy for US Policymakers
As a member, Renishaw will help educate policy leaders across the federal government to emphasize the benefits of additive manufacturing for national security, health, information security, manufacturing and more.
Read MoreRead Next
Building The Future Workforce of Additive Manufacturing
As additive manufacturing (AM) processes for metals evolve each day, educators and specialists are racing to standardize best practices across the industry. Tim Simpson—one of the leading experts in the field—has partnered with ASME to create a new framework in his Designing for AM With Metals course.
Read MoreAlquist 3D Looks Toward a Carbon-Sequestering Future with 3D Printed Infrastructure
The Colorado startup aims to reduce the carbon footprint of new buildings, homes and city infrastructure with robotic 3D printing and a specialized geopolymer material.
Read MorePostprocessing Steps and Costs for Metal 3D Printing
When your metal part is done 3D printing, you just pull it out of the machine and start using it, right? Not exactly.
Read More