Building The Future Workforce of Additive Manufacturing
Sponsored ContentAs additive manufacturing (AM) processes for metals evolve each day, educators and specialists are racing to standardize best practices across the industry. Tim Simpson—one of the leading experts in the field—has partnered with ASME to create a new framework in his Designing for AM With Metals course.

With vigorous growth projected well into the future of metal additive technologies, how are businesses and specialists keeping up to speed with rapid advancements in AM training and education?
Setting new methodologies in the AM eLearning space is no simple task. One way to achieve progress has been through partnerships across engineering communities, businesses, and organizations. These collaborations provide exciting opportunities to combine forces and innovate—establishing new industry standards and best practices as a result. In 2020, ASME is partnering with Siemens to further develop additive training services such as innovation in design, material development, and functional applications.
Projected Growth, Future Opportunity
Imagine the year is 2030, additive manufacturing revenues have doubled, and demand for specialists and experts in the field has opened doors to new and dynamic opportunities. Today, we are on track for this to become a reality. The mechanical engineers of tomorrow are now entering the AM workforce with diverse and varied skill sets. Exponential growth year over year—paired with the evolution of new technologies for additive manufacturing with metals—has created new challenges across the industry, and this ever-changing landscape has become commonplace.

With so many new materials, processes, and in-demand skill sets, there is a need for standardization and best practices. On a larger-scale, stronger regulation and oversight is still in development to ensure production quality standards and prevent counterfeiting. The standardization and best practice work is primarily being done in the e-learning space, and it's just beginning to gain traction with small and large businesses—and across the engineering communities.
What impact could setting new standards for AM processes have across industries? How could current and future workforces benefit from a stronger foundational knowledge of AM with standardized best practices?
AM experts like Tim Simpson—a professor of Engineering Design and Manufacturing at Penn State University—are working hard to standardize these new knowledge areas. eLearning courses, certifications, and degrees are becoming more common in the field, helping to equip the next generation of mechanical engineers with the base-knowledge that is necessary to succeed.
The Emergence of Laser Powder Bed Fusion
Laser-based powder bed fusion (LBFP) has rapidly increased in popularity amongst engineers, additive specialists, and manufacturers. Though 2017-18 had seen some unexpected short-term challenges, the current state of LPBF has a projected positive growth of 880M in hardware sales—slated for the end of 2019.

Powder Bed Fusion Hardware Market Performance
Source: SmarTech Markets Publishing
How does laser-based powder bed fusion work? Check out the video below to hear Tim Simpson explain the process.
Tim Simpson explains the powder bed fusion process.
With Growth Comes New Demand
With today’s laser-based powder bed fusion industry, there is an ever-expanding need for process-specific knowledge and skills across the AM workforce. In addition to this, business-case developers are also in high demand. Lack of education in these areas could slow market growth in the short term, but despite a turbulent market there are still many opportunities for businesses to adapt new technologies, scale-up, and recognize the potential of LPBF.
Defining Your AM Process
As a specialist in the workforce, or a stakeholder of a manufacturing company, which processes do you use to design or replicate parts?
There can be a number of challenges when it comes to process time, cost, and quality, like:
- Understanding resources needed to start a design from scratch
- How to modify and improve an existing part as an alternative
- Identifying when an existing part needs a complete overhaul
Identifying these variables and others can help you anticipate the challenges before they turn critical. For those exploring AM applications for the first time, defining your process is especially key to pursuing new and profitable opportunities.
Replicate, Adapt, Optimize: A New Approach to AM

How can Replicate, Adapt, Optimize™ become a standard solution? What does it mean?
These definitive terminologies are becoming part of the additive manufacturing lexicon across engineering communities and businesses alike. Companies have already been using the Replicate, Adapt, and Optimize™ steps in their manufacturing process, but due to a lack of formal naming conventions in the field, they are often not aware of this particular methodology.
Replicate is about time. Adapt is about cost. Optimize is about quality.
That doesn't necessarily mean they aren’t ready for it. Businesses are beginning to adopt similar methodologies—like Replicate, Adapt, Optimize™—to adjust their workflow and have a clearer understanding of what’s possible given their specific use case. In turn, stakeholders are sharing information across AM communities to communicate best practices, saving both time and money.
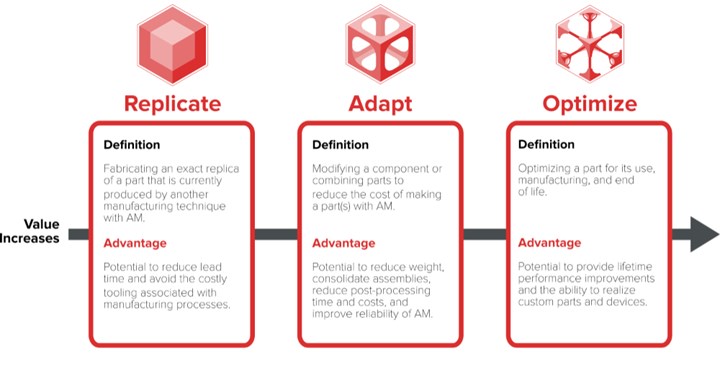
Use cases mapped to the value progression of additive manufacturing. Source: ASME.
View full size
Replicate
How can your business benefit from replicating an existing part? Is it a simple process? When a part is replicated using AM, both designers and business owners need to be cognizant of the manufacturing limitations and challenges associated with the adaptation of any additive process.
Tim Simpson explains when to replicate an existing part with additive manufacturing.

Replicating with AM helped NASA significantly reduce manufacturing time on this engine component. Source: NASA
When it comes to laser-based powder bed fusion systems for example, various design limitations need to be considered—such as overhangs, orientation, thin walls, and thick cross sections—all of which can pose unique challenges. Precise knowledge, skills, and tools are needed to reduce manufacturing time and cost, and stakeholders need to rely on informed decision-making by AM specialists.
Adapt
Modification poses significant challenges across the field of AM. Business owners can find themselves using it when they aren’t able to start completely fresh with a new design. Specialists can take certain aspects of an existing design and geometry and improve on it. As a result, a better case can be built for adapting designs for AM, such as:
- The cost of a part
- Optimization of a specific part for LBPF
- Enhanced performance of the part
- Avoiding constraints of traditional manufacturing processes
- Improved value proposition (making a better business case)
- Reduced post-processing needs

Adapt for AM tends to take more time, is more cost efficient, and has some improvement in quality. Source: ASME
When adapting a design for LPBF, it is important for the stakeholder and specialist to remember that the process isn’t linear. Several iterations of the part design will likely be required during build planning, and different modifications and refinements will likely take place. Each change that is introduced to the part design will affect its overall function, and may introduce a new set of challenges.
With the adapt use case the part may be modified for better use of AM but it is not completely redesigned.
Optimize
Whether you are an AM specialist starting from scratch, or a business owner reimagining an existing design, optimization provides the most freedom to change the geometry of any given part. As a specialist, optimizing a part allows a “clean sheet” approach—and utilizes both skill, knowledge, and innovation to generate new designs that leverage AM’s unique capabilities.
Computer programs and software are critical components of this step, and allow AM specialists to completely reimagine what parts and assemblies (even entire systems) look like in a variety of industries.

Optimization software will generate several design alternatives for a given set of part specifications. Source: Generative Design: The Road To Production” 2018. Engineering.Com.
Design optimization ensures that the part will print more quickly, provide a cost-effective solution for businesses, and be the most efficient use of metal materials. Benefits of an optimized design include:
- Achieving the lightest weight possible for the part, without compromising function
- The most efficient use of materials by placing it only where it is needed
- Reduced build time and cost
- Generating an optimal design that can withstand specified internal or external forces (loading, pressure, torque, vibration, etc.)
- Optimal design for thermal management
- Minimal post-processing
The optimize use case allows you to completely redesign the part.
ASME and Siemens Energy Join Forces
Siemens Energy and ASME are partnering to work towards scaling workforce development across the field of engineering. ASME’s agile course development, educational technology and learning science expertise—combined with Siemens broad AM know-how and experience—will enhance ASME’s Learning & Development course offerings.
As a result, the engineering community will benefit from an expansive body of subject-matter expertise, rooted in more than 10 years of scalable serial production experience in AM. All aspects of AM design, materials, and processes will be covered while connecting the AM ecosystem via Siemens to simplify the collaboration process, and streamline new production processes.
Interested in learning more? Check out ASME's course on Designing for AM With Metals.