Optimizing Mass and Material
Most machined parts have more material than necessary. This is true even after all of the cutting is finished.
Share
Read Next
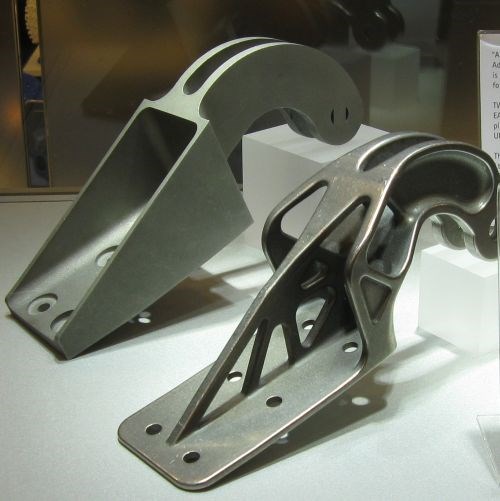
Machined parts often have more material than necessary. This is true even after all of the cutting is finished. In fact, it might be that most machined parts have more material than necessary. This is true because the part, in general, only has to mate with its required connections and carry its required stresses. Any material not necessary for these purposes is superfluous.
Still, we don’t usually know what that unneeded material is. We don’t typically model a part’s precise pattern of stresses to find out, because the information would have no practical use. A part tailored to the stresses it actually carries might look like the nearer of the two parts in this photo. Machining offers no practical way to make such an odd shape. However, additive manufacturing does.
This part, in both of the versions seen here, is a component of a hinge for a maintenance access hatch on an aircraft. The farther version is the traditional form of this part, produced through casting and machining. By contrast, the nearer version was optimized for its function using software from Altair then built additively using a direct metal laser sintering machine from EOS. Producing an optimal design in this way resulted in a part that weighs less and requires less material, even though it is still every bit as functional as the part that was machined. For much more on the redesign of this part for additive manufacturing, see this paper.
Related Content
-
At General Atomics, Do Unmanned Aerial Systems Reveal the Future of Aircraft Manufacturing?
The maker of the Predator and SkyGuardian remote aircraft can implement additive manufacturing more rapidly and widely than the makers of other types of planes. The role of 3D printing in current and future UAS components hints at how far AM can go to save cost and time in aircraft production and design.
-
How Norsk Titanium Is Scaling Up AM Production — and Employment — in New York State
New opportunities for part production via the company’s forging-like additive process are coming from the aerospace industry as well as a different sector, the semiconductor industry.
-
Two 12-Laser AM Machines at Collins Aerospace: Here Is How They Are Being Used
With this additive manufacturing capacity, one room of the Collins Iowa facility performs the work previously requiring a supply chain. Production yield will nearly double, and lead times will be more than 80% shorter.