Conflict spanning the last few decades in Armenia has left many of its citizens sustaining injuries, including the loss of limbs as well as injuries to hands and legs. Due to the difficulty of accessing quality health care, many of its citizens have ill-fitting prosthetics.
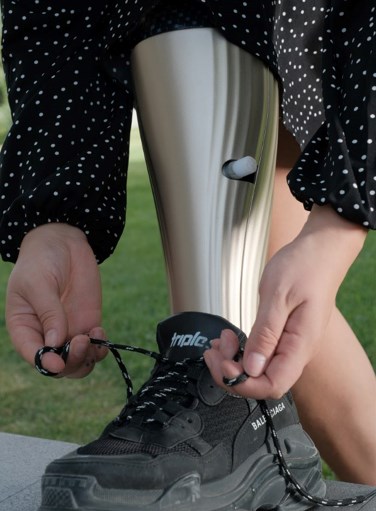
The protective shield (featured in gold) adjoins to the patient’s underlying prosthetic to ensure added protection as well as a personalized aesthetic. Photo Credit: Oqni
Fortunately, 3D scanning and printing serves as an effective solution in supporting the quality of life for citizens in need of proper care. Humanitarian and Armenia-based organization Oqni is working in tandem with scanning manufacturer Artec 3D to provide an accessible solution for war victims and injured citizens alike. Utilizing Artec 3D’s software, Oqni is scanning and printing customizable prosthetic shields for those in need.
The 3D printed shields are fitted onto the patient’s original prosthetic. The shield attaches into place on both the front and back of the prosthesis. The prosthetic shield is made with dimensions identical to the patient's existing limb to both cover and physically protect the prosthetic. These covers also aim to remove the stigma associated with amputation and address the psychological effect as well as the loss of confidence many amputees face. Lastly, the shields offer aesthetic value to reflect the personality and lifestyle of the wearer.
The Challenge
Armenia is home to a multitude of people who have experienced amputation. Combine this with the limited access to health care and it becomes clear that healing outcomes and patient care are not optimal. Add in the military escalation, earthquake activity, common road accidents and health complications and it’s not difficult to see why so many are experiencing injuries leading to amputation.
According to Oqni CEO and co-founder Hajk Bagradjans, safe and lasting solutions for upper limb prostheses are far and few between. While there are companies able to access and import the necessary prosthetics from overseas, these are not made accessible to all in need.
If one is even able to secure a prosthetic, the chance it will be a proper fit and made to last is slim.
An Additive Solution
To address the country’s growing need for properly fitted prosthetics, Oqni formed in 2020 as a response to war-induced amputation. Oqni’s goal was to provide not only comfort but confidence for amputees in Armenia who otherwise would not have access to proper care for living with an amputated limb.
Fortunately, the desire to progress and experiment with new technologies is present among the medical and foreign aid work assisting those in Armenia who need functional prosthetics.
Among these new technologies are 3D printing and scanning.
Originally, these technologies proved useful during the beginning of the COVID-19 pandemic in 2020. All over the world, shortages of medical supplies became an immense problem. In Paris, the number of COVID-19 cases climbed exponentially. Fortunately, French surgeon Dr. Roman Khonsari made the decision to deploy his Artec 3D scanner as a solution.
Khonsari utilized a 3D scanner and additive equipment to provide quality control for 3D printed emergency medical supplies in high demand and difficult to obtain.
Dr. Khonsari is a member of the Armenian community and therefore recommended Artec 3D technology to his colleagues who were in the process of forming a nonprofit to help injured citizens (Oqni).
This inspiration led to leveraging 3D printing and scanning for another feat in the medical field, assisting with the fitting, quality and availability of prosthetics.
The Technical Side
Artec 3D partnered with Oqni to reimagine the best way to support prosthetics for everyday use for patients. These factors include: protection, durability, strength, comfort and aesthetics.
The process begins with additive scanning technology. In order to accurately scan body parts, it was obvious a software solution was necessary. Artec Eva is the flagship scanner of Artec 3D and proved extremely successful in scanning medium-sized objects (such as hands, arms and feet). Light, portable and easy to maneuver, the 3D scanner can quickly generate textured and accurate 3D models.
- First, initial scanning is done. The patient stands or sits in the middle of the room while a member Oqni utilizes Artec 3D’s Eva scanning technology (an average scan takes no more than a minute). Both the healthy limb and amputated limb are scanned. Or in the case of a double amputation, both limbs are scanned to provide the most accurate data.
- Next up, the mirror feature of Artec 3D’s professional data processing
- The 3D modeling process then begins. Information collected via the initial patient interview (such as the patient’s favorite color, design or style) is what brings the 3D model to life. These details serve as the building block for the finalized prosthetic cover. After the design is selected, the number of holes needed to fit the cover onto the prosthetic are calculated.
- The prosthetic cover is printed and fitted to the patient. Oqni is currently using fused filament fabrication as the printer technology of choice and is opting for materials such as: PETG and TPU for flexible yet robust prosthetic covers. All 3D printing is done in-house but the team is currently searching for a 3D printing partner to provide selective laser sintering as another printer option.

The customized shields are currently being 3D printed via fused filament fabrication (FFF) technology, as depicted by the printers above. Oqni would like to explore other 3D printing avenues such as selective lasering sintering (SLS) for the creation of the covers in the near future. Photo Credit: Oqni
The finished covers provide a layer of protection that current prosthetics do not. The covers offer accommodation of any size, any design preferences or anything else a patient might require.
Added Additive Benefits
With Eva scanning, another benefit is the optimization of workflow, from scanning to printing. The process is drastically shortened for a quicker turnaround. Before Eva, measurements for prosthetics and protective covers were taken manually, a far more time-consuming process that left more room for error.
Without 3D scanning and printing, medical professionals would have to rely on more archaic methods of measurement (such as using measuring tape or calipers). While these methods might provide acceptable results, they still lack the accuracy needed for symmetry and the ability to capture harder-to-reach areas on the body.
Utilizing other Artec 3D technology, such as Artec Cloud and 3D modeling, quick feedback improves data that is then implemented for each and every fitting.
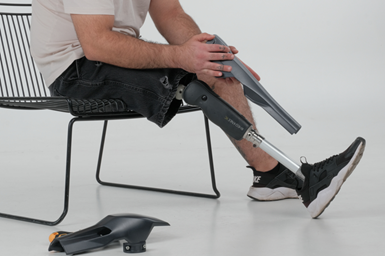
The above image depicts an amputee fitting the 3D printed protective shield into place to cover his prosthetic. The shield can be personalized to user preferance. Photo Credit: Oqni
To streamline the process and help more patients, Oqni has created a large database of 3D scans for different prosthetic types. In other words, 3D scans of the more common above-knee prosthetics are readily available.
If a 3D printed model does not fit a patient, the team can check existing covers to see where the issue within the 3D scan occurred. The team analyzes the scan to determine what changes need to be made to fit the cover onto the prosthetic. This saves valuable time in making amends to existing covers instead of creating completely new ones from scratch.
Oqni and Artec 3D have fitted over 120 amputees in Armenia with protective prosthetic covers and look forward to improving the process to offer its citizens a better quality of life via 3D printing technology solutions.
Related Content
MedCAD Titanium Facial Reconstruction Plates Now 3D Printed
MedCAD, creators of AccuPlate patient-matched titanium implants, has announced that AccuPlate 3DTi reconstruction plates for the mandible and midface are now 3D printed.
Read MoreRead Next
Alquist 3D Looks Toward a Carbon-Sequestering Future with 3D Printed Infrastructure
The Colorado startup aims to reduce the carbon footprint of new buildings, homes and city infrastructure with robotic 3D printing and a specialized geopolymer material.
Read More3D Printed Polymer EOAT Increases Safety of Cobots
Contract manufacturer Anubis 3D applies polymer 3D printing processes to manufacture cobot tooling that is lightweight, smooth and safer for human interaction.
Read MoreCrushable Lattices: The Lightweight Structures That Will Protect an Interplanetary Payload
NASA uses laser powder bed fusion plus chemical etching to create the lattice forms engineered to keep Mars rocks safe during a crash landing on Earth.
Read More