A Circular Economy for 3D Printed Plastics Starts with Material
When the greatest share of a product’s environmental impact comes from producing its feedstock, selecting the right material is critical. For 3D printing and manufacturing in plastic, biopolymer could be the first step toward a more sustainable model.
The New Plastics Economy project of the Ellen MacArthur Foundation has three tenets: One, plastics in use should stay in use. Two, plastic should be prevented from leaking into the environment, and existing litter should be recovered. And three, manufacturers should decouple from fossil fuel feedstock whenever possible.
The goal of this project is to establish a circular economy, or one which avoids waste and limits resource consumption by recirculating existing materials. In the case of plastics, a circular economy means recapturing and reusing existing plastics however possible, as well as limiting the creation of new, virgin materials made from nonrenewable fossil fuels.
“A single-use model where you extract fossil resources to make plastic, use it once, and landfill it — that’s the worst-case scenario,” says Dan Sawyer, business development leader at NatureWorks. The material manufacturer (jointly owned by Cargill and PTT Global Chemical) has been a collaborator with the Ellen MacArthur Foundation for the past eight years, helping to advance its vision of a sustainable, circular economy for plastics.
Additive manufacturing (AM) has a role to play in that vision. 3D printing is one possible method for reusing plastic material and feeding it back into the economy in a new form. But the disruption AM brings provides an opening for more sustainable manufacturing far earlier in the product lifecycle. Each new part or product made possible by AM, and every existing part or product that moves to this workflow, presents an opportunity to evaluate material choice — and, potentially, choose to manufacture with a sustainable polymer.
Manufacturing Plastics from Renewable Resources
“Sustainable polymer” could be interpreted in several ways, but for NatureWorks it means plastic made from renewable plant matter rather than nonrenewable petroleum. The company’s materials for 3D printing, thermoforming, injection molding and other industrial processes are all based on polylactic acid (PLA). This biopolymer is made by fermenting plant sugars into lactic acid, transforming it into lactide, and then polymerizing the lactide. This production method can result in a smaller carbon footprint, requiring less nonrenewable energy to manufacture than petroleum-based plastics.
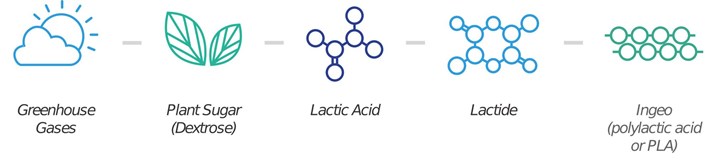
The Ingeo production process involves fermenting plant sugars into lactic acid, which can then be converted into lactide and polymerized into PLA. This biopolymer can generally be manufactured with a lower carbon footprint compared to petroleum-based plastics, the company says. Image: NatureWorks
Ingeo, the brand name for NatureWorks’ PLA material, is currently manufactured from corn in the U.S., but the feedstock could be any crop available in abundance provided it is responsibly sourced. “As we bring in new types of plastics decoupled from fossil fuels, we want to make sure we don’t create more problems,” says Leah Ford, global marketing communications manager. “Through the Ellen MacArthur Foundation’s New Plastics Economy Global Commitment, we’ve committed to make sure that 100% of the feedstocks we’re using will be certified as environmentally and socially sustainable.”
Filament producers convert the Ingeo PLA resin into 3D printing filament ready for use. During printing, the products offer good interlayer fusion and build platform adhesion; low shrinkage; and reduced emissions and particulate count compared to materials like ABS. (ABS offers better mechanical properties, an advantage that may or may not be valuable — see below.) Ingeo PLA is available in both build and support material grades, and the material has been used in 3D printing applications ranging from healthcare to industrial manufacturing.
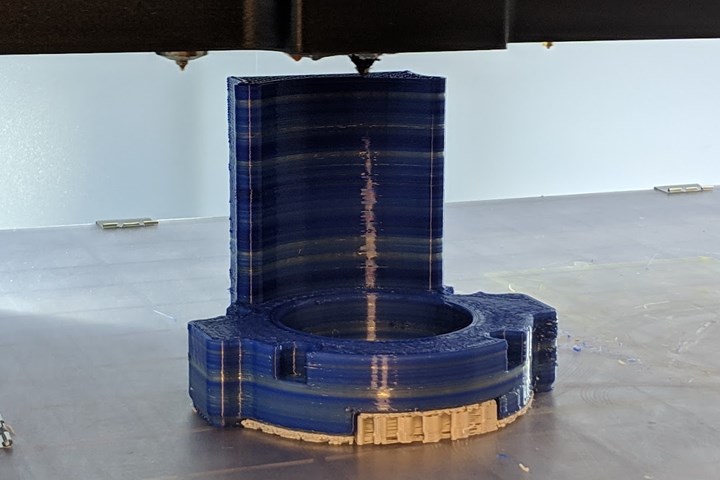
This part designed for investment casting demonstrates the use of Ingeo-based print material and support structures (the beige portion). Image: NatureWorks
Dealing with Biopolymers at End of Life
“The vast majority of the impact of a polymer product comes from producing the polymer itself,” Sawyer says. “If you compare, say, a recycled product made from a traditional polymer with one made from a biopolymer, the biopolymer almost certainly has a lower carbon footprint.”
Bio-based materials like Ingeo are an important development for helping manufacturers shift away from plastics based on fossil fuels. But material sourcing is only one part of a sustainable circular economy for plastics. There’s still the question of what will happen at the end of the product’s life, and how the material will be recovered and fed back into that economy. For plastics, an end-of-life scenario in the circular economy may mean reusing the material as-is, recycling it into something new, or returning it to its natural elements.
Often, what people mean by “biodegradable” is actually “compostable.”
“When you are producing and selling a biopolymer into the market, people jump to the assumption that it’s ‘biodegradable’ without even really understanding what that means,” Sawyer says. Technically, the term specifies that the object can be broken down by microorganisms, but there is no implied time frame — this process may take hundreds of months to thousands of years. Often, what people mean is actually “compostable,” describing a material that can be broken down into natural elements by first disintegrating the materials with water and heat, then biodegrading it with microorganisms. In a commercial composting environment, this process can be accomplished within weeks or months. Compostable is a regulated term that applies only to products that have obtained the necessary certification.
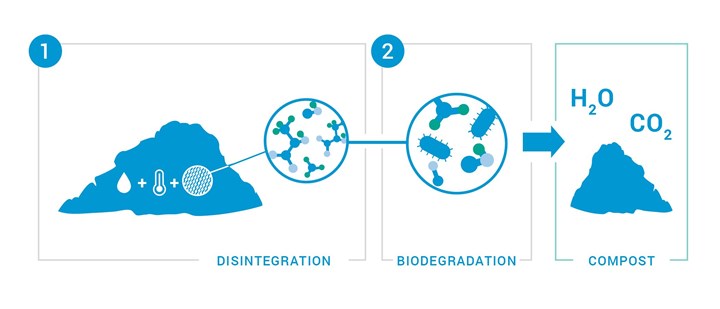
Ingeo biopolymer can be broken down in a two-step composting process. First, moisture and heat in the pile split the polymer chains and produce lactic acid. Then, microorganisms consume the smaller polymer fragments and lactic acid. The end products are carbon dioxide, water and humus, a soil nutrient. Image: NatureWorks
“In additive manufacturing, I think people would like composting to be an answer,” Sawyer says, “but to us, it isn’t a fit. The composting industry’s business is to produce useful compost, and plastic doesn’t bring the nutrients that come with food waste that they want.” An added challenge is that material thickness is a major factor in how quickly an item can be composted, and so part designs must be certified individually. For the kind of high-mix, low-volume production that AM promises, certification becomes an added barrier to composting.
NatureWorks therefore sees reuse and recycling as the best-case scenarios for its 3D printing material. If a printed product can’t be reused in its existing form, there are two options for recycling the PLA. The used plastic can be ground, melted, and pelletized or extruded into new feedstock with a mechanical recycling process. PLA can also be chemically recycled, which entails breaking the material down into lactide or lactic acid, or converting it into an industrial solvent.
A Circular Economy for Plastic 3D Printing
In short, a circular economy for plastics involves plastics producers, plastics reclaimers, and the choices made in between. But what does the aim of circularity mean for additive manufacturers in particular? Here are two implications to consider:
1. Carefully consider material choice in the design stage.
Companies that are at the beginning of the product life cycle and developing new products to be made additively should take care not to overengineer with material. The most advanced 3D printing polymer could have high-performance properties, but might also carry a higher environmental impact to produce and may be harder to reprocess. Instead, choose the plastic with the lowest impact that still offers the needed performance, and have a plan for its end of life. These considerations are especially important when the intended material contains fillers like glass and carbon fibers, which are energy-intensive to produce and difficult to recover from used material.
“Everyone thinks that they need carbon fiber reinforced ABS or nylon, without realizing that those compounds might be over-engineered for what the application requires.”
“Everyone thinks that they need carbon fiber reinforced ABS or nylon, without realizing that those compounds might be over-engineered for what the application requires,” Sawyer says. He points to precast concrete molds as one example; recently, we’ve seen greater use of 3D printed forms for pouring concrete as a replacement for forms built from plywood. The carbon fiber-filled ABS most commonly used is far more durable than plywood — ideal for a high-volume application, but overkill on a form that will only be used a few times.
For applications where a reinforced material is needed, however, there are more sustainable options. For example, Oak Ridge National Laboratory (ORNL) and the University of Maine have demonstrated 3D printing with a bio-based composite using fiber made from wood pulp to reinforce Ingeo polymer. This material could provide a low carbon footprint option for 3D printing tooling such as that used for marine composites, and would also be easier to reprocess, as the fiber could go through an extrusion process without having to be separated out.
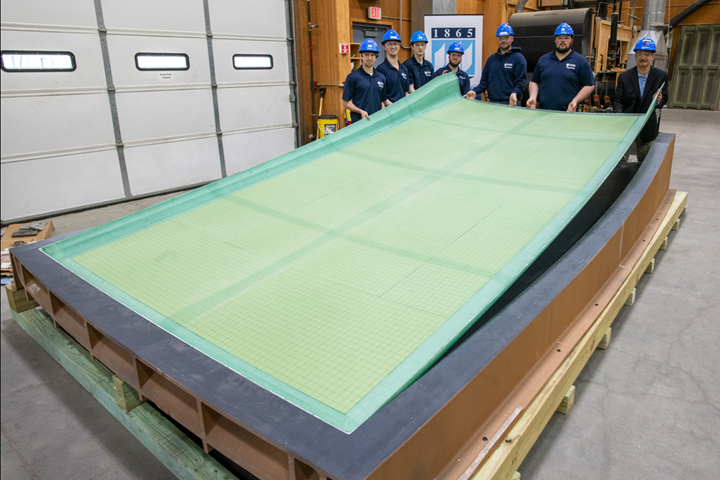
This boat hull section was printed at the University of Maine as part of a project with ORNL, demonstrating that fiber from wood pulp can be used to reinforce Ingeo biopolymer, forming a bio-based composite. Image: University of Maine
2. Look for new opportunities in waste streams.
The circular economy may also hold new opportunities for additive manufacturers and companies who are not yet 3D printing, by encouraging organizations to reconsider waste. “Part of the reason single-use plastics struggle in traditional recycling markets is because the end-user market is not there,” Ford says. 3D printing could offer new uses for material at the end of its lifecycle, if those end markets can be identified.
One example comes from Flo, a thermoforming company that makes plastic cups and cutlery. The company worked with a lab to find a way of using its trim scraps from manufacturing a line of coffee capsules. The solution it came to was to grind up those scraps and feed them through a robotic 3D printing system to build furniture for its trade show booths. While the furniture is currently just for the company’s own use, it could represent a new business opportunity.
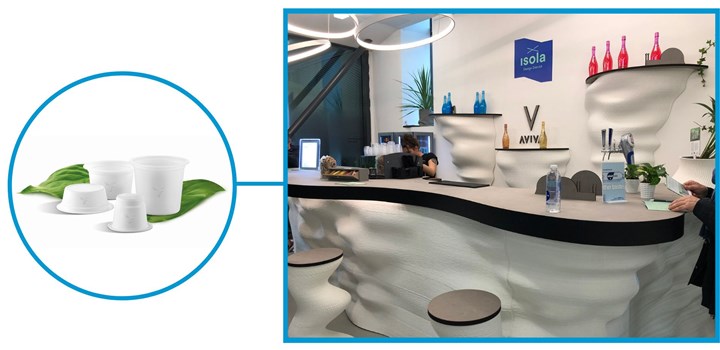
Flo utilized trimmings from manufacturing its Ingeo-based compostable coffee capsules (left) to 3D print furniture for its trade show exhibits. Images: NatureWorks
“Flo is an example of a company looking outside its own industry to take advantage of the scrap they had available and finding new, value-added uses for it,” Sawyer says. Traditional plastics manufacturers and other companies can potentially find new revenue streams like this while creating an end market for recycled material.
“There are multiple ways to enact the circular economy and sustainability right now, from sourcing your raw material to looking at those recovery, reuse and recycling pathways,” Ford says. “What are the new technologies that will allow us to recycle things better? How do we design materials from the get-go knowing they need to be recovered and recycled? How do we work as an industry to support the infrastructure we need to collect and recycle material with a value-added end market for those recycled materials? I think that’s really where the opportunity lies.”
Related Content
3D Printed Spine Implants Made From PEEK Now in Production
Medical device manufacturer Curiteva is producing two families of spinal implants using a proprietary process for 3D printing porous polyether ether ketone (PEEK).
Read MorePossibilities From Electroplating 3D Printed Plastic Parts
Adding layers of nickel or copper to 3D printed polymer can impart desired properties such as electrical conductivity, EMI shielding, abrasion resistance and improved strength — approaching and even exceeding 3D printed metal, according to RePliForm.
Read More3D Printing with Plastic Pellets – What You Need to Know
A few 3D printers today are capable of working directly with resin pellets for feedstock. That brings extreme flexibility in material options, but also requires greater knowledge of how to best process any given resin. Here’s how FGF machine maker JuggerBot 3D addresses both the printing technology and the process know-how.
Read More3D Printed Lattices Replace Foam for Customized Helmet Padding: The Cool Parts Show #62
“Digital materials” resulting from engineered flexible polymer structures made through additive manufacturing are tunable to the application and can be tailored to the head of the wearer.
Read MoreRead Next
Large-Scale 3D Printing Supports Innovation in Construction
Branch Technology’s robot-based Cellular Fabrication (C-Fab) 3D printing technology builds open matrices in high-performance polymers. These structures could be the framework for better, more sustainable building practices.
Read MoreHow 3D Printing Enables Sustainability in a High-Turnover Consumer Market
Pengraff UK built its business initially providing mounting solutions for routers and telecommunications equipment, hardware with built-in obsolescence. 3D printing and sustainable materials enable the company to live its values while manufacturing products with a limited lifespan.
Read MoreAdditive Manufacturing Will Aid And Accelerate The Circular Economy
A circular economy links material, design, manufacturing, product and end-of-life in a continuous, sustainable loop. This special report illustrates the roles for 3D printing every step of the way.
Read More