Velo3D’S Sapphire XC 1MZ EnableS Large-format Metal 3D Printing
The printer is designed to significantly increase throughput up to 400% and lower costs by up to 75% compared to the original Sapphire.
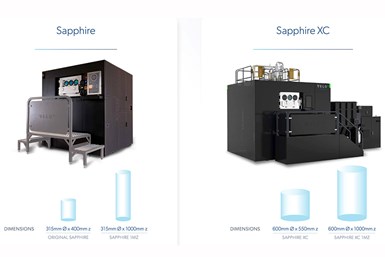
Photo Credit: Velo3D
Velo3D Inc., a metal additive manufacturing (AM) technology company for mission-critical parts, has added the Sapphire XC 1MZ to its Sapphire family of printers. The printer enables customers to print parts one meter in height — with a total build volume that is twice that of the Sapphire XC and nine times larger than the original Sapphire, thereby increasing the addressable use cases of Velo3D’s end-to-end metal AM solution.
Sapphire XC 1MZ is said to have the largest laser powder bed fusion (LPBF) print volume from a leading manufacturer. The Sapphire XC 1 MZ system combines Velo3D’s geometric capabilities with the repeatable, standardized processes and validated material properties necessary to achieve distributed manufacturing in a larger format.
The Sapphire XC 1MZ was designed based on feedback from customers in the aerospace, energy and defense industries, with the first systems expected to be delivered to several aerospace companies in late Q3 2022. The system is designed to significantly increase throughput up to 400% and lower costs by up to 75% compared to the original Sapphire, the company says.
Features of the Sapphire XC 1MZ include a large build volume of 600 mm × 1,000 mm, which the company says is 30% larger than printers from other leading manufacturers, and eight 1-kilowatt lasers. It also includes an integrated, end-to-end manufacturing solution with Flow print preparation software and Assure quality assurance software.
The company says the Intelligent Fusion manufacturing process that has been proven in production on the Sapphire and Sapphire XC offers consistent, repeatable results across different printers. It is also said to feature a faster, noncontact recoater to decrease the time required between build layers.
The Sapphire family of printers is comprised of four unique system variations that are fully compatible with one another, running the same processes across all printers in a way that delivers consistent results on any machine. This means that as customers validate one printer for production use, it is simple to add additional printers to increase productivity.
Related Content
-
8 Cool Parts From Formnext 2023: The Cool Parts Show #65
New additive manufacturing technologies on display at Formnext were in many cases producing notable end-use components. Here are some of the coolest parts we found at this year’s show.
-
Next-Gen Horse Trailers to Be Built With Robotic 3D Printing
Double D Trailers is currently developing a prototype horse trailer that will be made with large-format additive manufacturing. The technology brings potential benefits for labor, weight and design features to this subset of recreational vehicles.
-
Evaluating the Printability and Mechanical Properties of LFAM Regrind
A study conducted by SABIC and Local Motors identified potential for the reuse of scrap reinforced polymer from large-format additive manufacturing. As this method increases in popularity, sustainable practices for recycling excess materials is a burgeoning concern.