Stratasys Expands Material Options for New Manufacturing Systems
RAPID 2021: New materials offer solutions for advancing additive manufacturing at production scale.
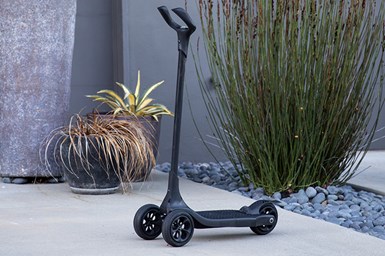
Stratasys continues to expand its ecosystem of materials to offer customers a variety of options across 3D printing technologies and solutions, including new materials for the Stratasys H350 and Stratasys Origin One 3D printers.
The SAF-powered Stratasys H350 3D printer is specifically designed for the mass production of end-use parts with consistency, and the ability to customize and control the production workflow. The H350 will initially utilize High-Yield PA11, a sustainable material derived from 100% bio-based castor beans. In addition, in 2022, PA12 (also known as Nylon 12) will be available for the H350. PA12 provides dimensional stability, chemical resistance and impact strength, and has been used across various additive manufacturing (AM) printing technologies for creating jigs and fixtures, tooling and functional end-use parts.
Stratasys has further expanded its ecosystem of materials with two new materials by Henkel for the Stratasys Origin One. Stratasys Dura56 by Loctite is said to be a durable, impact-resistant photopolymer with exceptional surface finish and a low cost per kilo. The material was created to address applications with high material consumption and for functional applications where aesthetics and robustness are critical. Dura56 is said to be well suited for end-use parts such as housings, parts with mating features or class A surfaces. The Dura56 material is formulated to meet the specific needs of Stratasys’ customers and provide print technicians with greater efficiency.
The second material for the Origin One printer is Loctite 3D IND405 Clear, a one-part, semirigid 3D-printable clear photopolymer resin that is said to provide smooth surface finish, good impact resistance and elongation. Parts printed in IND405 can be polished to an optically clear finish. The material can be machined, tapped and polished, and is well suited for microfluidic devices as well as guide overlays. Its qualities are most comparable to unfilled polypropylene, the company says.
Related Content
-
3D Printing with Plastic Pellets – What You Need to Know
A few 3D printers today are capable of working directly with resin pellets for feedstock. That brings extreme flexibility in material options, but also requires greater knowledge of how to best process any given resin. Here’s how FGF machine maker JuggerBot 3D addresses both the printing technology and the process know-how.
-
Video: 5" Diameter Navy Artillery Rounds Made Through Robot Directed Energy Deposition (DED) Instead of Forging
Big Metal Additive conceives additive manufacturing production factory making hundreds of Navy projectile housings per day.
-
Additive Manufacturing Is Subtractive, Too: How CNC Machining Integrates With AM (Includes Video)
For Keselowski Advanced Manufacturing, succeeding with laser powder bed fusion as a production process means developing a machine shop that is responsive to, and moves at the pacing of, metal 3D printing.