Sandvik’s Osprey Metal Powders for Increased Manufacturing Capacity
Rapid + TCT 2022: Range of Osprey metal powders includes premium titanium alloys and copper powder, as well as nickel-based superalloys, cobalt-chrome and ultra-hard maraging steels.
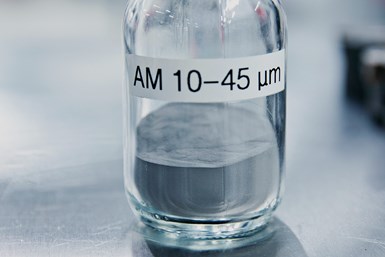
Sandvik’s Osprey metal powder. Photo Credit: Sandvik
Sandvik says its ever-evolving range of Osprey metal powders offers increased production capacity for additive manufacturing (AM) with a portfolio that includes premium titanium alloys and copper powder, as well as nickel-based superalloys, cobalt-chrome and ultra-hard maraging steels.
The powders are produced in state-of-the-art and highly automated powder manufacturing facilities in-house at Sandvik and are able to provide unsurpassed levels of consistency and traceability, the company says. It is said that due to the materials authority controlling the entire additive value chain — from powder to finished component — the Osprey metal powders are well suited for industries where reliability is key.
In 2021, Sandvik announced it was continuing to invest in metal powder capacity for AM by installing two additional atomization towers at its production site in Neath, UK. This expansion followed investments in manufacturing capacity for titanium and nickel-based superalloys in Sandviken, Sweden.
The company says it offers extensive capabilities in terms of providing high-quality and consistent metal powders to customers engaged in a variety of AM processes such as laser powder bed fusion, electron beam melting and binder jetting. By installing these additional atomizing towers, the company says it is set to significantly increase its production capacity for premium metal powders, and is even better positioned to meet the increased demand for metal powders for AM.
Related Content
-
This Year I Have Seen a Lot of AM for the Military — What Is Going On?
Audience members have similar questions. What is the Department of Defense’s interest in making hardware via 3D printing over conventional methods? Here are three manufacturing concerns that are particular to the military.
-
3D Printed NASA Thrust Chamber Assembly Combines Two Metal Processes: The Cool Parts Show #71
Laser powder bed fusion and directed energy deposition combine for an integrated multimetal rocket propulsion system that will save cost and time for NASA. The Cool Parts Show visits NASA’s Marshall Space Flight Center.
-
Video: 5" Diameter Navy Artillery Rounds Made Through Robot Directed Energy Deposition (DED) Instead of Forging
Big Metal Additive conceives additive manufacturing production factory making hundreds of Navy projectile housings per day.