Araqev’s QC Software Helps Limit Design Iterations
The company says the software’s machine-learning models enable it to derive modifications to the nominal designs, so when the modified designs are printed, they will exhibit fewer shape deviations compared to when original designs are printed.
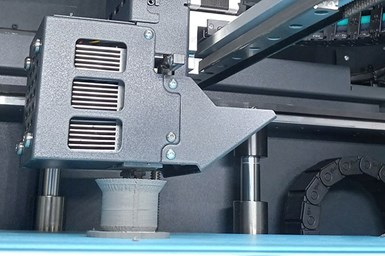
A Markforged Metal X 3D printer creates a stainless-steel tool in Purdue University’s Herbert C. Brown Laboratory of Chemistry. Photo Credit:Purdue Research Foundation/Steve Martin
Araqev, a Purdue University-related company, has developed a quality control software for additive manufacturing (AM) and 3D printing that is said to help end users print products in only a few design iterations, leading to less scrap material and machining time.
The company estimates that quality control issues with AM can lead to nearly $2 billion in global losses annually, based on a model for the production costs of metal AM systems that was developed by Baumers, Dickens, Tuck and Hague in their 2016 paper published in the peer-reviewed journal Technological Forecasting and Social Change.
To use Araqev’s software, customers upload their nominal design files and scanned point cloud data from their printed products. The software uses these inputs to fit machine-learning models that can simulate shape deviations for future printed products. Those models enable the software to derive modifications to the nominal designs, known as compensation plans, so that when the modified designs are printed, they will exhibit fewer shape deviations compared to when the original designs are printed.
Araqev’s algorithms are also said enable the transfer of knowledge encoded via machine learning models across different materials, printers and shapes in an AM system. According to the company, this means that the software enables a comprehensive platform for a customer to improve quality for its entire system.
The company says a variety of companies could benefit from this type of quality control software, including aerospace, automotive, consumer products, medical devices, national defense and other sectors that use AM and 3D printing technologies.
Araqev licensed the software from the Purdue Research Foundation Office of Technology Commercialization. The research to create the software received funding from the NSF’s Cyber-Physical Systems program and CMMI EAGER program, and the Purdue Research Foundation Office of Technology Commercialization’s Trask Innovation Fund. Araqev received funds from Elevate Ventures’ Regional Pre-Seed Competition, Purdue’s Regional NSF I-Corps program, the MKE Tech Hub Coalition Challenge and the Purdue Foundry Boost program.
Related Content
-
3D Printed "Evolved Structures" for NASA Exoplanet Balloon Mission: The Cool Parts Show #61
Generative design creates stiff, lightweight brackets for EXCITE mission monitoring planets orbiting other stars. The Cool Parts Show visits Goddard Space Flight Center.
-
3MF File Format for Additive Manufacturing: More Than Geometry
The file format offers a less data-intensive way of recording part geometry, as well as details about build preparation, material, process and more.
-
7 Things We Saw at Formnext 2024 — Video Playlist
There were countless processes, applications and announcements at Formnext 2024. Here are seven standouts Peter Zelinski and Stephanie Hendrixson caught on film.