Tritone Technologies Forges US Strategic Alliance With Adia
Tritone’s technology enables quick and easy switching between a wide variety of metals and ceramics, making it possible to simultaneously manufacture parts of different sizes, shapes and applications.
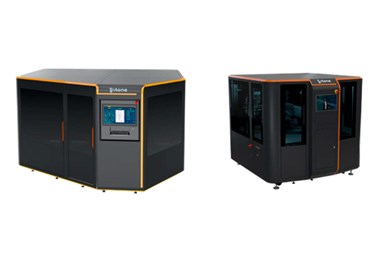
(Left to right) Tritone Dominant and Dim AM Systems now available from Adia. Source:
Tritone Technologies, a provider of metal and ceramic additive manufacturing (AM) technology for industrial production, has created a strategic partnership with Adia Inc. to enhance its presence, technical support and integration expertise in the New England region. The company says this collaboration is an important milestone in Tritone’s North American expansion strategy as it aims to strengthen ties with established 3D experts at a regional level.
“We actively investigate new technologies and pursue partnerships that enhance customer value,” says Nick Gondek, Adia principal/director of additive manufacturing. “Our collaborative approach aims to empower customers to maintain competitiveness. Tritone’s MoldJet technology and experienced business team align perfectly with our model, and we’re excited to represent them in our region."
Tritone’s expanding presence in North America includes key machine installations and AM integration partnerships. Collaborating with Adia reinforces Tritone’s position as a key player in the US AM market, offering comprehensive solutions for streamlining metal and ceramic component manufacturing.
“I have known the Adia leadership for over a decade as competitors and am definitely happy to now be working on the same team with them,” says Ben Arnold, Tritone Technologies vice president of business development NA. “They have the technical experience and business credibility we seek in partners.”
Tritone offers two AM systems which utilize Tritone’s proprietary MoldJet technology. This powder-free AM technology enables industrial production of high-quality metal and ceramic parts at industrial speed. MoldJet is specifically designed to produce large quantities of parts with complex geometries. The technology enables quick and easy switching between a wide variety of metals and ceramics, making it possible to simultaneously manufacture parts of different sizes, shapes and applications.
Related Content
-
Cranial Implant 3D Printed From Hydroxyapatite Ceramic: The Cool Parts Show #76
Cranial implants are typically made from titanium or PEEK; in this episode of The Cool Parts Show, we look at how implants made from a bioceramic can improve osseointegration and healing.
-
Horizon Expands Services With Subcontract Micro AM Production, Design Support
Horizon also offers a suite of proprietary coating processes that enable customers to successfully expand the functionality of parts which are typically produced in plastics on commercially available micro additive manufacturing platforms.
-
Formlabs Expands SLA/SLS Ecosystem With New Materials, Postprocessing Tools
The new hardware, software and materials are designed to streamline postprocessing and unlock new workflows.