Mantle, Wepco Plastics Partner on 3D Printed Tooling Case Study
Collaboration with Wepco plastics is said to demonstrate surface finish superior to aluminum tooling.
Share
Read Next
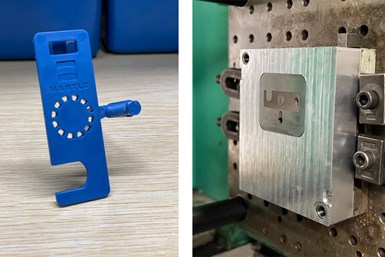
In case study, Wepco Plastics was able to go from concept to parts in just a few weeks using Mantle inserts and minimal machining with the surface finish on the ABS cellphone holders smoother using the lightly polished inserts than it would have been with lightly polished aluminum tooling. Photo Credit: Wepco Plastics
Mantle Inc. — developer of precise, efficient metal 3D printing technology for the tooling industry — collaborated with Wepco Plastics on a case study to print tool components with its H13 Flowable Metal Paste material. The results showed equivalent performance to conventional H13 tool steel, the companies say.
The study is said to demonstrate the benefits of Mantle’s TrueShape technology in quickly printing precision components for prototype and production tools, molds and dies, and going from designs to molded parts in weeks.
Mantle’s TrueShape technology is said to produce inserts with a smooth matte surface finish suitable for molding, with a mere 1-3 µm Ra surface roughness. The collaboration with Wepco Plastics sought to evaluate the technology when molding a cellphone stand, which is representative of the consumer market, in which surface finish is often critical to quality.
Wepco Mold Designer Steven Kronenberger worked closely with Mantle’s Senior Application Engineer Scott Kraemer to design the inserts and conformal cooling channels. Mantle then printed them in about 80 hours.
The processing setup was swift, and molding the parts in both blue and black ABS plastic produced smooth surface finishes without the time required for polished aluminum, according to Amanda Wiriya, Wepco manufacturing support director. Not only that, but the machine operators were impressed with how easily parts came off the tool. “We’ve had issues in the past demolding parts from 3D printed plastic inserts,” Wiriya says. “This was a totally different experience.”
Related Content
-
In Casting and Molding, AM Simplifies Conventional Manufacturing
In new ways, additive processes are streamlining and enabling metal casting and plastic injection molding.
-
Video: Hybrid Manufacturing Without Melting: Hermle’s Metal Powder Application (MPA) Process
The Metal Powder Application (MPA) process uses cold spray to apply metal to an existing workpiece. Because the material deforms rather than melts, MPA opens new possibilities for functional grading and other multimaterial applications.
-
3D Printed Mold Tooling Advances in Performance With Proprietary Resin
Material improvements offer turnkey production and cost trimming with 3D printed mold tooling. A new, proprietary resin addresses the current limitations associated with 3D printing in polymer.