Essentium Helps Fast-Track COVID-19 Testing Kiosk
Company helps speed the design and production of Worlds Protect kiosks for convenient mass screening of COVID-19 and other infectious diseases.
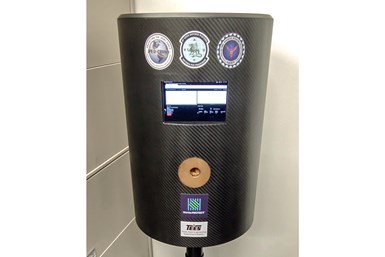
Worlds Protect COVID-19 breathalyzer kiosk. Photo Credit: Essentium
Essentium’s High Speed Extrusion (HSE) 3D printing platform and industrial materials have been used to conceptualize, design, prototype and manufacture 10 functional Worlds Protect COVID-19 breathalyzer kiosks in an accelerated time frame. The Worlds Protect team — a collaboration between The Texas A&M University System, Worlds Inc. and the U.S. Air Force — developed the kiosks to provide quick, convenient and accurate breathalyzer tests suitable for on-site screening of large groups of people for COVID-19 and other infectious diseases.
The kiosk requires a person to use a disposable straw to blow into a copper inlet. In less than a minute, test results with accuracy comparable to a polymerase chain reaction (PCR) test can be sent to the participant’s smartphone, according to ongoing preliminary data testing, the company says.
Due to the tight timeline and an unpredictable supply chain caused by the pandemic, the Worlds Protect team required a solution to manufacture complex part designs and increase prototyping speed without sacrificing mechanical properties. With the military deployed in hot and dry regions, the Worlds Protect kiosk must be robust enough to function in harsh environments.
According to the company, its Essentium’s technology and materials enabled rapid iteration to conceptualize, design and develop in days instead of weeks. Most kiosk parts were printed in less than a day which is said to be 66% faster than the three-day turnaround for traditional subtractive manufacturing methods. The Worlds Protect team was also able to reduce costs by up to 90% in some instances. For example, one of the mountings used in the final product was quoted at $110 for a machined version and cost only $12 to 3D print.
During part design, the team used Essentium PLA to iterate. The final parts needed to withstand temperatures up to 100°C and have sufficient tensile strength. The team chose Essentium PA-CF due to its exceptional strength, temperature resistance and printability.
“Essentium’s High Speed Extrusion 3D Printing Platform is a game changer in fast tracking the design and development of these much-needed COVID-19 breathalyzer kiosks,” says Maulik Kotecha, a doctoral student at Texas A&M University. “We need the ability to rapidly screen large groups of people, with targeted expanse into austere environments. Together with Essentium, we have made this a reality in the fastest time possible.”
Throughout the pandemic, the 3D printing industry has been instrumental in innovating and producing essential medical gear. “Now we are proud to support the Worlds Protect team to speed the development of kiosks that represent a significant leap forward in the COVID-19 fight and tackling other infectious diseases,” says Blake Teipel, Essentium CEO. “3D printing has delivered once again with reliable and repeatable quality at speed.”
Related Content
-
3D Printing with Plastic Pellets – What You Need to Know
A few 3D printers today are capable of working directly with resin pellets for feedstock. That brings extreme flexibility in material options, but also requires greater knowledge of how to best process any given resin. Here’s how FGF machine maker JuggerBot 3D addresses both the printing technology and the process know-how.
-
At General Atomics, Do Unmanned Aerial Systems Reveal the Future of Aircraft Manufacturing?
The maker of the Predator and SkyGuardian remote aircraft can implement additive manufacturing more rapidly and widely than the makers of other types of planes. The role of 3D printing in current and future UAS components hints at how far AM can go to save cost and time in aircraft production and design.
-
How Machining Makes AM Successful for Innovative 3D Manufacturing
Connections between metal 3D printing and CNC machining serve the Indiana manufacturer in many ways. One connection is customer conversations that resemble a machining job shop. Here is a look at a small company that has advanced quickly to become a thriving additive manufacturing part producer.