Dyndrite, Novanta Collaborate to Enhance Laser-Based AM Metal Printing Machine Capabilities
The companies are working to create proof-of-concept, enabling Dyndrite software to directly generate low-level scanning trajectories for use with Novanta hardware.
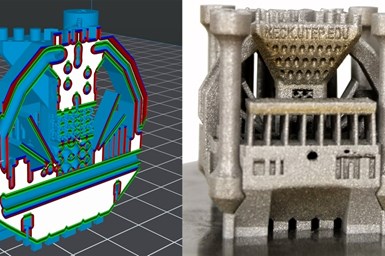
Dyndrite's software is said to give LPBF materials, part/process and applications engineers power and control over their geometry, build specific toolpathing and laser parameters. Photo Credit: Dyndrite
Dyndrite is collaborating with Novanta Corp. in support of its Firefly 3D and Lightning II laser beam steering solutions. Dyndrite is a provider of a GPU-accelerated computation engine which is used to create digital manufacturing hardware and software.
The companies will work together on a proof-of-concept that will enable Dyndrite software to directly generate low-level scanning trajectories for Novanta hardware. This will provide users of Dyndrite Additive CAM software the ability to generate very fine resolution scanner trajectories, which makes full use of the advanced functions and underlying power of the laser scanner hardware.
Novanta says its high-precision scanning solutions are used in a variety of laser powder bed fusion (LPBF) machines, but are often not fully utilized by standard trajectory strategies. It is said the company’s scanning solutions are often capable of being operated at much higher levels of performance with a wider range of scan strategies than often made available to the open market today.
Engineered as an enclosed, compact solution to enable multiheaded machine architectures with up to 100% overlap, Firefly 3D is well suited for today’s serial production high throughput additive manufacturing (AM) machines. Incorporated within the design are features to simplify installation and operation, including features such as precise monitoring of the AM process, and synchronised process and motion data.
“High-performance scanners such as Novanta’s Firefly 3D and Lightning II are designed with smart technology to predict their own capabilities and limits,” says Simon Matthias, Novanta technical business development manager. “This informs the controlling hardware how best they can be driven to allow full use of the scanners’ complete bandwidth. We’ve seen what is possible from a materials and process standpoint with Dyndrite and knew working with them would unlock the full potential of our scanners.”
Parameter and scanning pattern development is a massive undertaking when qualifying new materials and machines. For this reason, there is often a conservatism that leads users and developers of machines, and the software that drive them, to stay within traditional approaches, relying on standardized scanning patterns such as checkerboard or similar hatch-based approaches. The result is often a reduction in efficiency and the missed potential of realizing improvements in material microstructures.
Dyndrite aims to disrupt this traditional model of parameter development by providing unprecedented software power, freedom and control over the scanner. These controls and algorithms can leverage the power of the underlying hardware to deliver more efficient, less costly machine design and better process interactions which can lead to better material properties and accelerated build rate.
“Dyndrite was formed as we saw that the manufacturing hardware had outpaced the software,” says Harshil Goel, Dyndrite CEO. “Our work with Novanta is one step closer to reversing this industry-stifling trend. We look forward to working with the Novanta team and showcasing the combined power of our solutions.”
- Learn how Dyndrite end-user software expands development for LPBF machines, supporting multioptic build strategy operations and laser parameter control limited only by vendor openness.
- Read about how Dyndrite and SLM Solutions are working together to enable users to fully create SLM parameters and tool paths to fit their individual needs, maximizing materials development and application or part-specific build rate strategies.
- Check out this article about HP choosing Dyndrite Kernel to help power its next-generation, cloud- and edge-based digital manufacturing solutions.
Related Content
3MF File Format for Additive Manufacturing: More Than Geometry
The file format offers a less data-intensive way of recording part geometry, as well as details about build preparation, material, process and more.
Read MoreCopper, New Metal Printing Processes, Upgrades Based on Software and More from Formnext 2023: AM Radio #46
Formnext 2023 showed that additive manufacturing may be maturing, but it is certainly not stagnant. In this episode, we dive into observations around technology enhancements, new processes and materials, robots, sustainability and more trends from the show.
Read MoreSpherene Creates Metamaterial with Geometry Derived from Spheres
An algorithm developed by Spherene Inc. generates Adaptive Density Minimal Surfaces (ADMS) as a self-supporting infill strategy that can be used to reduce mass and manage material properties in 3D printed parts.
Read MoreRobot Vs. Gantry for Large-Format Additive Manufacturing (Includes Video)
Additive Engineering Solutions, specialist at 3D printing very large parts and tools on gantry machines, now also uses a robot for large-format AM. Here is how the robot compares.
Read MoreRead Next
Postprocessing Steps and Costs for Metal 3D Printing
When your metal part is done 3D printing, you just pull it out of the machine and start using it, right? Not exactly.
Read MoreAlquist 3D Looks Toward a Carbon-Sequestering Future with 3D Printed Infrastructure
The Colorado startup aims to reduce the carbon footprint of new buildings, homes and city infrastructure with robotic 3D printing and a specialized geopolymer material.
Read More3D Printed Polymer EOAT Increases Safety of Cobots
Contract manufacturer Anubis 3D applies polymer 3D printing processes to manufacture cobot tooling that is lightweight, smooth and safer for human interaction.
Read More