America Makes Announces Winners of Open Project Call Totaling $1.2 Million
The open project call topics were initiated at the America Makes’ Additive Manufacturing Technology Roadmap workshops in 2021 and 2022.
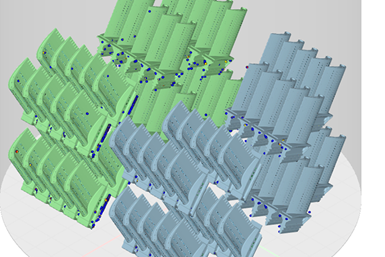
Layer height data projected onto a 3D model reveals the points at which the incomplete part distorted as it was being 3D printed. This is potentially useful insight for improving the design of the part. Source: Velo3D
The National Center for Defense Manufacturing and Machining (NCDMM) and America Makes (the National Additive Manufacturing Innovation Institute) have announced the winners of the $1.2 million Open Project Call funded by the Office of the Under Secretary of Defense, Research and Engineering Manufacturing Technology Office (OSD(R&E)) and the Air Force Research Laboratory (AFRL).
Additive manufacturing (AM) technologies offer a range of benefits including unique product geometries, fewer tooling requirements and relatively shorter lead times in comparison to other manufacturing methods. The industrialization of AM represents an opportunity to convert demonstrated manufacturing capability into capable manufacturing capacity.
America Makes facilitated workshops in 2021 and 2022, convening leaders in the AM industry, along with Institute members and advisory group participants, that ultimately resulted in the continued curation of the Additive Manufacturing Technology Roadmap. The roadmap was used to identify and formulate the topical areas for the project call.
“The continuous progress made in research, development and implementation of AM innovations in the areas of design, materials, processes, genome and value chain that result from these funded projects is paramount to our nation’s competitive advantage,” says Brandon Ribic, technology director at America Makes. “Forecasts suggest a continued surge in AM in the coming years as more traditional manufacturing industries are expected to shift toward 3D printing for production, due to its ability to create complex, high-performance parts at lower costs and faster speeds. The work currently being facilitated by these awardees is instrumental to the technological advancements of tomorrow and can be integrated across diverse industries, including those still utilizing traditional manufacturing.”
Award winners and related topic areas:
Topic 1: Design for Dimensional Inspection of Internal Features via In-Situ Process Monitoring
- Project 1: Inspection Using In-Situ Height Mapping Data
- Team Lead: RTX Technology Research Center (RTRC)
- Project Team: Velo3D
Topic 2: Thermal Manipulations for Processing Improvements
- Project 1: Fast Scanning Mirror Wobble Enabled Build Schema (Fast-WEBS)
- Team Lead: GE Research
- Project Team: Johns Hopkins University
Topic 4: Frameworks for Utilizing Process Monitoring in Conjunction with Ex-Situ Inspection for Qualification
- Lead: R3 Digital Science
- Project Team: Macy Consulting; The Ohio State University Center for Design and Manufacturing Excellence; and University of Louisville Additive Manufacturing Institute of Science & Technology Team
Topic 6: “Should vs. Could” Tool and Training
- Project 1: America Makes Methods and Approaches for Sustainable Operations
- Team Lead: Deloitte Consulting
- Project Team: N/A
Project teams will report on their progress at the America Makes Technical Review and Exchange, and other industry events during the execution phase of the program.
America Makes is a public-private partnership for AM technology and education. Its members from industry, academia, government, workforce and economic development organizations work together to accelerate the adoption of AM and the nation’s global manufacturing competitiveness. It was founded in 2012 as the Department of Defense’s national manufacturing innovation institute for AM and first of the Manufacturing USA network. It is managed by the not-for-profit NCDMM.
Related Content
“Mantis” AM System for Spacecraft Uses Induction for Deposition
The metal 3D printing system melts wire without lasers. 30-foot-diameter parts are built on a rotary-feed system that eliminates the need for a large machine frame or gantry.
Read MoreAircraft Ducts 3D Printed in Composite Instead of Metal: The Cool Parts Show #68
Eaton’s new reinforced PEKK, tailored to aircraft applications, provides a cheaper and faster way to make ducts compared to formed aluminum.
Read More3D Printed Lattice for Mars Sample Return Crash Landing: The Cool Parts Show Bonus
NASA Jet Propulsion Laboratory employs laser powder bed fusion additive manufacturing plus chemical etching to create strong, lightweight lattice structures optimized to protect rock samples from Mars during their violent arrival on earth.
Read MoreAt General Atomics, Do Unmanned Aerial Systems Reveal the Future of Aircraft Manufacturing?
The maker of the Predator and SkyGuardian remote aircraft can implement additive manufacturing more rapidly and widely than the makers of other types of planes. The role of 3D printing in current and future UAS components hints at how far AM can go to save cost and time in aircraft production and design.
Read MoreRead Next
Alquist 3D Looks Toward a Carbon-Sequestering Future with 3D Printed Infrastructure
The Colorado startup aims to reduce the carbon footprint of new buildings, homes and city infrastructure with robotic 3D printing and a specialized geopolymer material.
Read MoreCrushable Lattices: The Lightweight Structures That Will Protect an Interplanetary Payload
NASA uses laser powder bed fusion plus chemical etching to create the lattice forms engineered to keep Mars rocks safe during a crash landing on Earth.
Read MoreBike Manufacturer Uses Additive Manufacturing to Create Lighter, More Complex, Customized Parts
Titanium bike frame manufacturer Hanglun Technology mixes precision casting with 3D printing to create bikes that offer increased speed and reduced turbulence during long-distance rides, offering a smoother, faster and more efficient cycling experience.
Read More