Aconity3D, Equispheres Achieve Productivity Gains for Metal 3D Printing
The companies say they have achieved remarkable productivity improvements using laser beam shaping and NExP-1 high-performance AM powder.
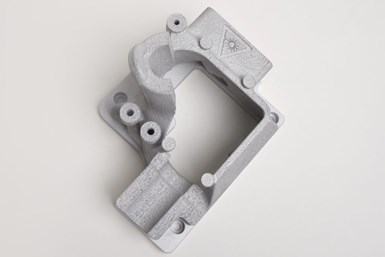
An Aconity3D part printed with Equispheres powder as part of case study. Source: Equispheres
Equispheres and Aconity3D say they are again breaking new ground in metal additive manufacturing (AM), achieving build rates about 9 times greater than industry norms for aluminum powder and laser powder bed fusion (LPBF). Aconity3D is known for manufacturing custom, precise metal AM printers, while Equispheres produces specialized powders with unique attributes specifically designed for AM.
Building on previous production speed improvements, Aconity3D and Equispheres have continued to push the limits of their machine and materials technologies. Using Aconity3D printing equipment with laser beam shaping and Equispheres’ NExP-1 AM powder, the two companies have achieved production speeds in excess of 430 cm3/hr for a single laser.
“There are three pillars supporting this remarkable achievement,” says Evan Butler-Jones, vice-president – Product and Strategy at Equispheres. “The leading-edge capabilities of Aconity3D’s printing technology, the novel application of beam shaping and the unique powder properties of Equispheres' NExP-1 printing material. This powerful combination allowed us to achieve outstanding results."
Laser beam shaping is used in other industries and has gained attention in AM due to its potential to improve processing speeds. In LPBF, beam shaping modifies how energy is deposited on the powder bed, altering the power density and thermal gradient.
To fully explore the potential of beam shaping, the two partners selected a material with stable melting behavior and a tightly controlled printing process. NExP-1 is a best-in-class AlSi10Mg powder tailored for high performance by Equispheres’ production process. It provides consistent, repeatable melting properties. The AconityMIDI+ was modified with an IPG YLR 3000/1000-AM with beam-shaping capabilities, enabling 3 kW of maximum power for this project. Instead of a zoomed gaussian beam, the shaped beam reduces overheating and spatter formation in high-productivity processing. Aconity3D’s printing systems are modular, enabling maximum functionality through tailor-made AM solutions.
“Aconity3D’s printing technology and the team’s expertise were crucial to this project's success. We’re working with extremely high-powered lasers, testing additive manufacturing process parameters far beyond previous capabilities,” Butler-Jones says. “It was necessary to have the precise control and monitoring capabilities of Aconity3D printers.”
The resulting build speed outpaces current production rates for aluminum additive manufacturing by a large margin. “NExP-1 powder is vital to achieve these remarkable speeds,” explains Martin Buscher, Aconity3D head of testing facilities. “It has exceptional properties that make it ideal for high-speed work. The powder characteristics enable optimal melting behavior, which is required to achieve consistent printing with high-powered lasers at these extraordinary speeds.”
Related Content
-
Preassembled Turbojet Engine, 3D Printed in One Build: The Cool Parts Show #75
Turbojet engines typically consist of hundreds or thousands of parts, but this engine — 2023 winner of The Cool Parts Showcase for Best Proof of Concept — was 3D printed as just two pieces, with the monolithic rotor embedded inside the stationary engine shell.
-
Quadrus: Powder Management Tactics for Tungsten Rhenium and Other AM Alloys
The expert in additive manufacturing of high-value parts for the Defense Department often must change from one exotic material to another in its powder bed machines. Cleaning is a core competency. Here are lessons of this company’s system for working with an ever-changing mix of 3D printed alloys.
-
3D Printed Lattice for Mars Sample Return Crash Landing: The Cool Parts Show Bonus
NASA Jet Propulsion Laboratory employs laser powder bed fusion additive manufacturing plus chemical etching to create strong, lightweight lattice structures optimized to protect rock samples from Mars during their violent arrival on earth.