Freeformer Enables Tailored Pharmaceutical Production
A 3D printer for polymer part production has enabled researchers from the University of East Anglia to develop individually tailored pharmaceuticals that better support patient needs and outcomes.
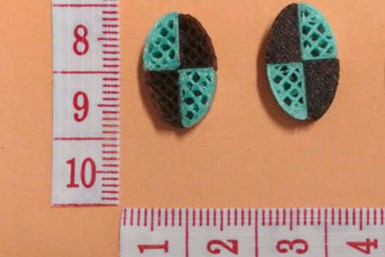
A research group at the University of East Anglia developed 3D-printed tablets that incorporate multiple active ingredients. The release rate increases as the filling level decreases, resulting in personalized dosages.
Photo Credit: Arburg
While medical devices, implants and custom-made prostheses have already given additive manufacturing a vital place in healthcare manufacturing, pharmaceuticals have historically lagged behind. Sheng Qi, a pharmaceutical engineer at the School of Pharmacy at the University of East Anglia (UEA), has recently made breakthroughs to change this, opening new possibilities in the delivery of patient-specific therapeutic and drug delivery.
With a 2019 report discovering that 44% of men and 57% of women over 65 take five or more drugs every week — with 12% of respondents in the group taking at least ten — proper delivery of pharmaceuticals is more important than ever. As most pharmaceuticals are composed of generic dosages of active ingredients, with generalized release patterns that may or may not meet a patient’s needs, overmedication and unwanted side effects are a recurring problem.
Qi’s research group means to eliminate this problem with personalized medicine. “By working alongside colleagues in hospitals and pharmacies, I have seen first-hand that customized tablets could be a solution for pediatric and geriatric patients, as well as those with complex chronic conditions,” she says.
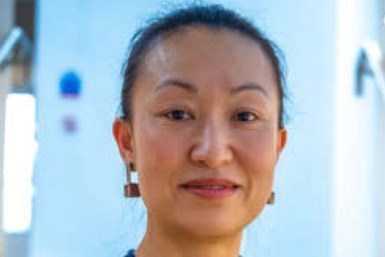
Dr. Sheng Qi, pharmaceutical engineer and scientist at UEA’s School of Pharmacy, headed the research project into 3D-printed pharmaceuticals.
Photo Credit: University of East Anglia
Solving Material Issues
In 2015, Qi’s research group began investigating 3D printing pharmaceuticals through fused deposition modeling (FDM). She quickly discovered that this printing method would prove unsuited to her goals — many manufacturers only supply their own consumables, and the remaining platforms did not offer the medical-grade reproducibility she required.
FDM also proved a poor fit for the low thermal stability of pharmaceuticals, as the materials required thermal loading during both their extrusion into filaments and their discharge through a hot nozzle during the additive manufacturing process.
In 2019, Qi conducted trials with Arburg’s Freeformer printer, which uses the company’s proprietary Arburg plastic freeforming (APF) method and prints with granules rather than filaments. This industrial 3D system offers a higher level of material freedom, and especially suits pharmaceuticals, as the system is compatible with granules produced through traditional pharmaceutical granulation processes. The increased precision, flexibility and process stability of APF convinced Qi to focus her research group’s efforts on production with the Freeformer.
Freedom to Experiment
APF technology and the Freeformer are open systems that Arburg says are flexible to adaptation, including to the specialized requirements of this use case. Compatibility with standard granulates from common pharmaceutical polymers and active ingredients enabled Qi’s research group to proceed without additional plasticizers, instead discharging plastic melt as tiny droplets to additively manufacture individually tailored drugs. The group was also able to create and test a wide range of filling-level variants and experiment with the porosity of the tablet to regulate the active ingredient’s release rate. “The Freeformer offered our team the flexibility to optimize various densities and adjust them precisely,” Qi says. “The reproducibility of results was steady and robust.”
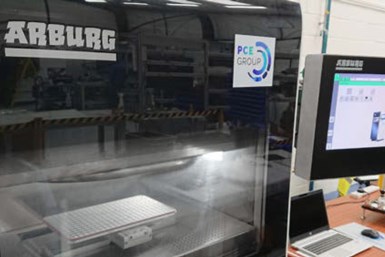
Arburg’s Freeformer works precisely with granule material, offering repeatability that made it suitable for AM pharmaceutical production.
Photo Credit: Arburg
Slicing software and material discharge as droplets support the deposition of fixed volumes. “This high level of precision is hugely important as it enables us to obtain uniform results,” Qi emphasizes. “With other technologies, we struggled to achieve consistent print results, and these are a prerequisite for targeted active ingredient release.” The APF process, by contrast, facilitated testing and evaluating various active ingredient combinations and their release rates. Qi’s research group could even explore the possibility of blending several drugs with specific dosages and packaging them in a 3D-printed tablet with sophisticated functional micro-structures designed to speed up patient recovery.
Personalized Results
To date, personalized pharmaceuticals have only been available to patients undergoing cancer treatment. Yet Qi believes personalized medicine for other diseases could improve therapeutic outcomes and enhance the patient experience. Faster patient recovery from individualized pharmaceuticals could also shorten stays in hospitals, saving money for both the healthcare facility and the patient.
An AM approach to pharmaceuticals also supports flexibility in treatment — other industries have seen lead times decrease from weeks to days with the transition to AM, and healthcare providers and pharmaceutical manufacturers could see this benefit as well.
Related Content
8 Cool Parts From Formnext 2023: The Cool Parts Show #65
New additive manufacturing technologies on display at Formnext were in many cases producing notable end-use components. Here are some of the coolest parts we found at this year’s show.
Read More3D Printed Lattices Replace Foam for Customized Helmet Padding: The Cool Parts Show #62
“Digital materials” resulting from engineered flexible polymer structures made through additive manufacturing are tunable to the application and can be tailored to the head of the wearer.
Read MoreBauer Hockey Uses EOS 3D Printed Digital Foam for Customizing Helmets
The new in-store experience, combined with proprietary 3D printing technology, opens the door for personalized hockey products.
Read MoreNMPA Certifies Farsoon 3D Printed Tantalum Interspinal Fusion Cage
The company says the additively manufactured implants can be fully customized according to patients’ conditions, and the trabecular microstructure can achieve a high porosity of 68-78% to promote bone tissue and vessel fusion.
Read MoreRead Next
3D Printed Polymer EOAT Increases Safety of Cobots
Contract manufacturer Anubis 3D applies polymer 3D printing processes to manufacture cobot tooling that is lightweight, smooth and safer for human interaction.
Read MoreBike Manufacturer Uses Additive Manufacturing to Create Lighter, More Complex, Customized Parts
Titanium bike frame manufacturer Hanglun Technology mixes precision casting with 3D printing to create bikes that offer increased speed and reduced turbulence during long-distance rides, offering a smoother, faster and more efficient cycling experience.
Read MoreProfilometry-Based Indentation Plastometry (PIP) as an Alternative to Standard Tensile Testing
UK-based Plastometrex offers a benchtop testing device utilizing PIP to quickly and easily analyze the yield strength, tensile strength and uniform elongation of samples and even printed parts. The solution is particularly useful for additive manufacturing.
Read More