Desktop Metal’s Robotic Additive Manufacturing System for Sand Printing
The ExOne S-Max Flex system use single-pass jetting technology to deliver 3D printing at high speeds for low-cost parts.
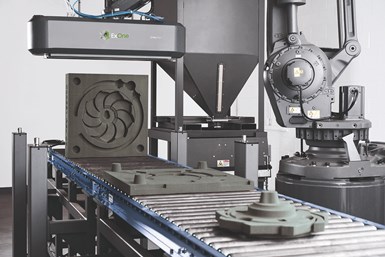
Desktop Metal’s ExOne S-Max Flex is said to offer an affordable, precise and robust tool for sand 3D printing. Photo Credit: Desktop Metal
Desktop Metal’s ExOne S-Max Flex is a scalable, large-format binder jetting system that 3D prints sand tooling. Foundries can use the system to quickly cast complex metal designs for the aerospace, automotive, energy industries and more.
The Flex is said to combine ExOne’s sand printing expertise in process and materials with proprietary Desktop Metal single-pass jetting (SPJ) technology to offer an affordable, precise and robust tool for foundries stepping into the next era of digital casting
According to the company, the system pairs an affordable industrial robot with an all-new end effector printhead design which deposits binder into a 1900 × 1,000 × 1,000 mm (74 × 39 × 39 in) telescoping build box that grows as the parts are built layer by layer. Additional build box sizes are available up to 4,700 × 1,000 × 1,000 mm (185 × 39 × 39"), with taller versions available up to 1,000 × 2,500 × 2,400 mm (39 × 98 × 94").
Desktop Metal says its high-throughput SPJ technology can deliver a build rate up to 115 L/hr. which offers foundries quick and reliable production to operate more efficiently in times of ongoing labor shortages, as well as a faster return on investment. The system is said to print standard silica sand with furan binders and delivers final parts with dimensional accuracy of ± 0.5 mm. The system also comes with several accessories and safety features that are configurable to fit a variety of spaces.
Other industries can also take advantage of the system’s large form and ability to binder jet a variety of powders. Infiltrated sand tooling for plastic thermoforming, composite layup and sacrificial tooling applications can be printed, along with infiltrated sand consumer products. Desktop Metal’s Forust brand, which upcycles byproducts of the wood waste stream into consumer designs, will also leverage the system to cost-effectively print large-form factor wood parts at scale. Additional projects are underway printing reclaimed concrete and other materials.
Related Content
-
3D Printing Solutions to Support Investment, Sand Casting
3D Systems is highlighting a design strategy for better investment casting patterns, as well as a new machine suitable for the production of patterns for sand casting.
-
Intrepid Automation: How Investment Casting Benefits From High Speed DLP
Vat polymerization 3D printing for investment casting patterns offers a way to deliver design freedom at production speed.
-
Additive Enhances Lost Foam Casting Process for Metal Manufacturing
Skuld LLC brings a new, 3D printing-enabled version of lost foam casting to market via its turnkey package for metal manufacturers. Additive Manufacturing Evaporative Casting (AMEC) enables metal parts made with sustainability and efficiency in mind.