USAF, GE Additive 3D Print Out-of-Production Metal Parts
The upcoming final phase of the Pacer Edge program is to establish the USAF’s own metal additive production infrastructure initially at Tinker Air Force Base in Oklahoma.
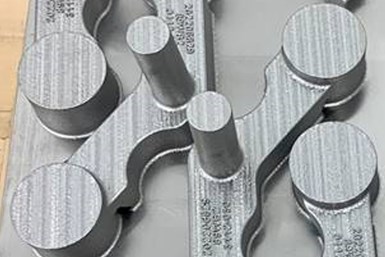
Metal 3D printed production parts for the Pacer Edge program (printed in cobalt-chrome and nickel alloy 718 on a GE Additive Concept Laser M2) nine months after requirement flow down. Photo: GE Additive
The U.S. Air Force (USAF) and GE Additive recently entered the third phase of its ‘Pacer Edge’ pathfinder program. Phase III has focused on 3D printing for four parts that are currently obsolete — a bell crank, gearbox seat, anti-icing valve body and a cross shaft arm. The first two parts (the cross shaft arm and the bell crank) have been successfully printed in cobalt-chrome on a fleet of M2 Series 5 system at GE Additive’s Cincinnati facility.
The final phase of the program over the coming years is to establish the USAF’s own metal additive production infrastructure initially at Tinker Air Force Base in Oklahoma. This capability will alleviate long lead timetables that currently plague the casting and forging industries.
“Pacer Edge represents a monumental step forward in innovative partnership with industry,” says John Sneden, director of propulsion, USAF. “Through this program, our enterprise team will deliver safe and timely propulsion readiness in support of the United States warfighter.”
It is said the USAF is not the only entity struggling to receive their castings and forgings in a timely manner. It remains a choke point for many industries and has only been exacerbated by the COVID-19 pandemic.
“Public-private initiatives like the recently announced ‘AM Forward’ initiative will also help to address DoD’s sustainment and readiness challenges head on,” said Lauren Tubesing, director of operations, Military Programs at GE Additive. “Strengthening U.S. supply chains, by encouraging small- and medium-sized manufacturers across the United States to adopt metal additive technology, will create a nationwide network of a qualified additive manufacturing suppliers.”
Related Content
-
Two 12-Laser AM Machines at Collins Aerospace: Here Is How They Are Being Used
With this additive manufacturing capacity, one room of the Collins Iowa facility performs the work previously requiring a supply chain. Production yield will nearly double, and lead times will be more than 80% shorter.
-
Additive Manufacturing Is Subtractive, Too: How CNC Machining Integrates With AM (Includes Video)
For Keselowski Advanced Manufacturing, succeeding with laser powder bed fusion as a production process means developing a machine shop that is responsive to, and moves at the pacing of, metal 3D printing.
-
3D Printed Titanium Replaces Aluminum for Unmanned Aircraft Wing Splice: The Cool Parts Show #72
Rapid Plasma Deposition produces the near-net-shape preform for a newly designed wing splice for remotely piloted aircraft from General Atomics. The Cool Parts Show visits Norsk Titanium, where this part is made.