8 Transformations 3D Printing Is Making Possible
Additive manufacturing changes every space it touches; progress can be tracked by looking for moments of transformation. Here are 8 places where 3D printing is enabling transformative change.
Share
It’s difficult to take the pulse of additive manufacturing at any particular point in time, because AM is not unified by any one market it serves, the materials it uses or even any specific process. But the use of 3D printing technology to build parts layer by layer does leave a trail. In any of the businesses and markets where AM is successfully adopted, it inevitably disrupts — and its progress can be tracked by looking for those moments of transformation. In my keynote address at this year’s Women in 3D Printing TIPE Conference, I chose to highlight eight places where additive is currently transforming how, when, where and why production happens. Watch the recording below, or scroll on for a recap of eight transformations that 3D printing is making possible.
1. 3D Printing Is Supporting Better Healthcare Outcomes
Medical implants are arguably one of the most mature applications for 3D printing currently, but the technology is continuing to deliver new possibilities in healthcare. Providers of external devices such as hearing aids, mouth guards, splints, prosthetics and orthotics are taking advantage of 3D scanning technology to quickly design and manufacture custom, better-fitting and functioning items, sometimes even at the point of care. And 3D printed medical items are even beginning to reduce the price of healthcare — by limiting return visits and even in some cases lowering the cost of devices.
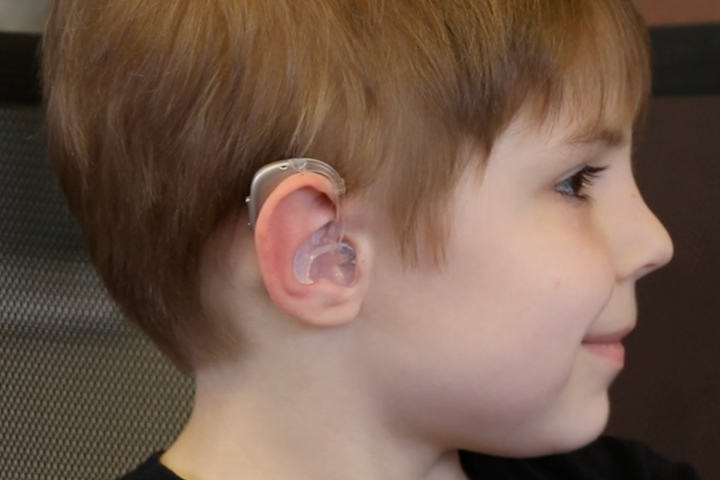
3D printing coupled with 3D scanning allows for a fully digital process to take the place of manual work like fitting medical devices. Nonprofit 3DP4ME is using the combination to make hearing aids more accessible to people with hearing loss in the Middle East. Photo Credit: Microsonic Inc.
2. 3D Printing Is Enabling the Next Wave of Space Exploration
Recent commercial and research space missions have taken advantage of 3D printing to produce complex, lightweight parts — weight being a key consideration for anything that has to reach Earth’s atmosphere or get beyond it. 3D printed parts have been successfully used in space for years (see the Perseverance Mars rover for instance) but are becoming critical to advancing space exploration. The Artemis I mission launched in 2022 relied on multiple 3D printed components, like pogo accumulator assemblies within the Space Launch System (SLS) and ESD-safe parts used in the Orion space capsule. Going forward, AM may be the manufacturing method best suited to off-planet production of tools, replacement parts and even habitats for astronauts.
3. 3D Printing Is Accelerating Electrification
Electrification is touching many markets including drones, vertical takeoff and landing (VTOL) aircraft, scooters, and even dirt bikes, but the rise of electric vehicles (EVs) is enabling AM to make inroads into automotive never before possible. New EV startups and electrification efforts from established automakers, coupled with the supply chain disruptions of the last few years, have made 3D printing an attractive option for obtaining parts quickly and often locally. 3D printing is being applied to rapidly prototype new vehicles; for bridge production as manufacturing ramps up; and increasingly for production at scale. A greater variety of vehicles is possible through AM as well; PixMoving, for instance, uses a skateboard-style chassis made with 3D printed components that can be easily resized to suit whatever type of EV body is needed.
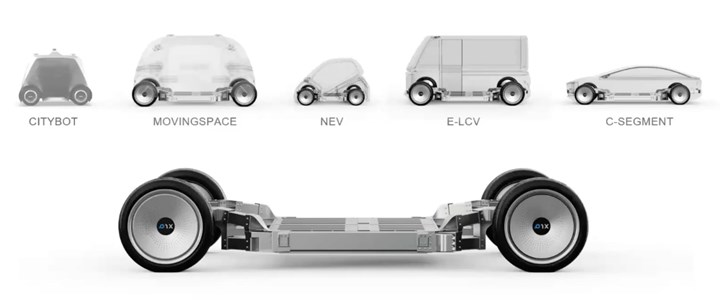
AM is making it economical for one company to produce a greater variety of vehicles. PixMoving has developed a skateboard chassis made with 3D printed parts that can be easily scaled to whatever size is needed by the customer. Photo Credit: PixMoving
4. 3D Printing Is Bringing New Material Possibilities
Materials that are difficult to cut or form, like ceramics and Inconel, are finding expanded opportunities through 3D printing where the change in process also removes these hurdles. 3D printing also makes it possible to use materials more frugally, in multiple senses. Reinforcing fibers can be placed with greater precision, and rare or expensive materials applied judiciously. Multimaterial capabilities make it possible to apply high-value substances like rare earth magnetic materials just where they are needed, reducing waste and cost. Material suppliers are also bringing brand-new polymers, alloys and composites to market tailored just for additive, such as resins with electro-static dissipative properties. And, the ease of 3D printing with alternative materials is challenging assumptions about which parts must be metal; in many cases, a 3D printed polymer or composite might be the better choice for cost or weight savings.
5. 3D Printing Is Keeping Systems In Service Longer
Here again, recent supply chain disruptions have spurred AM into new applications for what might be very old parts. 3D printing is increasingly being applied to upgrade systems for efficiency and to produce legacy items that are no longer available. Additive is not necessarily winning here because it is the cheapest option, but it is likely to be the fastest option. Compared to waiting for a casting, OEMs are finding it more expedient to reimagine components for 3D printing. The parts pictured below are part of a Siemens Energy generator cover ring that would have taken up to a year to receive as a bronze casting; the company redesigned the ring to be 3D printed in pieces, producing the complete component in just 18 weeks. Legacy replacement parts are also important for establishing the viability of additive parts in various verticals; if replacement parts are successful, the case for 3D printed parts in new products advances.
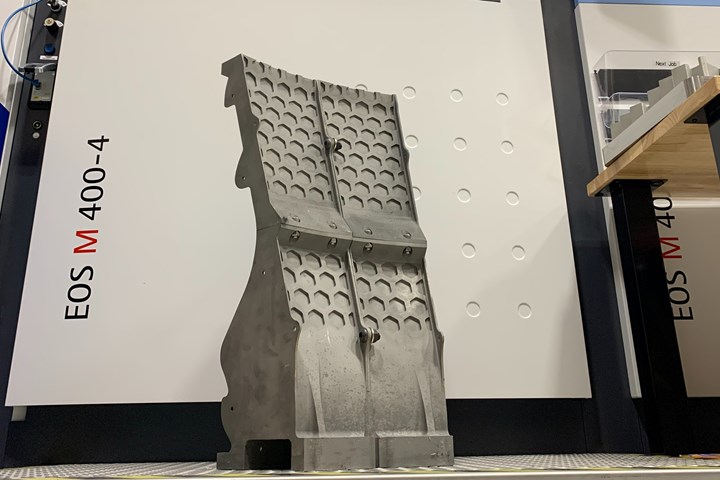
These 3D printed components are part of a large ring for a Siemens Energy generator cover. The components were produced in about 18 weeks, replacing a bronze casting with lead time approaching 12 months. Photo Credit: Siemens Energy
6. 3D Printing Is Altering Consumer Goods
There are a growing selection of 3D printed consumer products already available in markets like footwear, sporting equipment, jewelry and even furniture. Additive manufacturing has found footing here as a means of producing custom items, as well as increasingly mass-produced goods. But the transformation on the horizon now for 3D printed consumer goods has more to do with end-of-life plans for these items; AM can deliver products that use fewer materials and less material overall, potentially offering a path to goods that are easier to recycle when they are no longer needed.
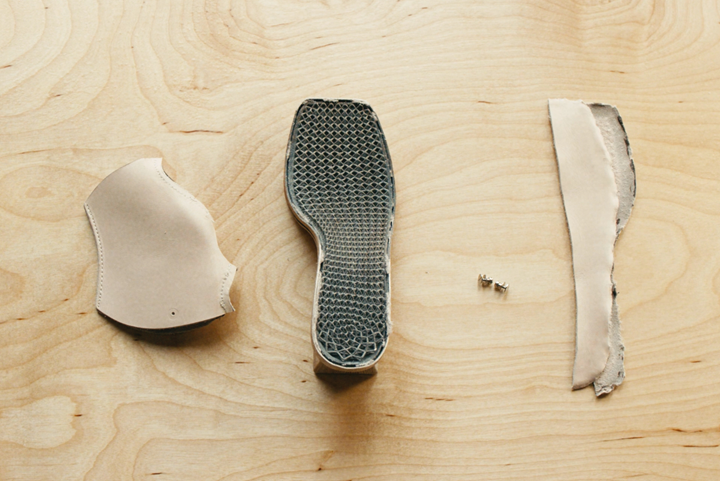
Hilos shoes are produced on demand and customized to the wearer, but the real innovation might be how they are designed to be taken apart. Each shoe consists of a 3D printed platform, a few pieces of leather and a couple of fasteners that can be easily separated for recycling. Photo Credit: Hilos
7. 3D Printing Is Changing What "Production" Means
Traditionally production has meant manufacturing thousands or millions of identical parts at large, centralized factories, but with 3D printing, that model no longer applies. Additive manufacturing makes variety possible; rather than millions of identical parts, production can look like batches of similar parts tailored to specific applications or users. Production doesn’t have to happen all at once, either; products and parts can live in a digital warehouse rather than a physical one, to be produced only when they are needed. Manufacturing can be decentralized and distributed across multiple production sites, with technologies such as biometrics and blockchain being deployed to protect files. Through 3D printer networks and other distributed manufacturing models, production can become “glocal,” with goods available globally but manufactured locally.
8. 3D Printing Is Changing Who Can Be A Manufacturer
With additive manufacturing, barriers to entry are falling away. It is no longer the case that it requires large amounts of capital and equipment to develop a product and launch it into the market; an individual can get started with just an idea and an affordable desktop printer. Products can be produced as they are sold, on demand, removing the need to make and store excess inventory and allowing the inventor to continue to iterate. It is not even necessary to own or operate the 3D printer anymore, with the advent of manufacturing networks that will handle production and pay out royalties to designers who list their products through these services. The reductions in startup challenges have helped manufacturing reshore in some cases, and enter locations where it has never been done in others. Designers, students, inventors, creators and companies that have not previously made their own products are becoming manufacturers through 3D printing.
This collection represents how 3D printing allows manufacturing to be reshored; to enter places it has never been before; and puts production in the hands of creators. Top row: Elias Stahl and Gaia Giladi, cofounders of sustainable shoe company Hilos; Spencer Loveless, who reshored production of Dustless products using 3D printing; Casey Melvin, a former law school student who founded The Future of Jewelry with her sister. Bottom row: Sarah Wells, COO of Spectrum Dental Printing, which started as an in-practice dental lab; Heidi Hertel, founder, and Gabe Schlumberger, CEO, of custom glasses company Fitz Frames; and an employee at Slant3D demonstrating how the company’s Angled.io platform makes it easy for a designer to launch a product digitally.
Related Content
8 Cool Parts From Formnext 2023: The Cool Parts Show #65
New additive manufacturing technologies on display at Formnext were in many cases producing notable end-use components. Here are some of the coolest parts we found at this year’s show.
Read MoreWhat Does Additive Manufacturing Readiness Look Like?
The promise of distributed manufacturing is alluring, but to get there AM first needs to master scale production. GKN Additive’s Michigan facility illustrates what the journey might look like.
Read MoreRead Next
Reshoring Manufacturing With 3D Printing: The Cool Parts Show #34
Wet-dry vacuum maker shifts to additive manufacturing for first entirely U.S.-made product, a jackhammer accessory. More U.S. production to come via 3D printing.
Read MoreHow Additive Manufacturing Is Transforming EVs and Transportation: AM Radio #23
As 3D printing is adopted into the electric vehicle (EV) market, it is not just vehicles that are being reshaped. In this episode of the AM Radio podcast, we discuss additive manufacturing and the future of transportation.
Read More6 Reasons Space Exploration Will Need Additive Manufacturing
There are at least half a dozen ways 3D printing will contribute to space travel, research and habitation — and in some cases it already is. Insights from seminar focused on manufacturing challenges for the space sector.
Read More