Updated Definition Makes Way for AM Part Production
Additive manufacturing is finding its footing, and a new standard definition in ISO/ASTM 52900:2021 shows that AM is for more than prototyping.
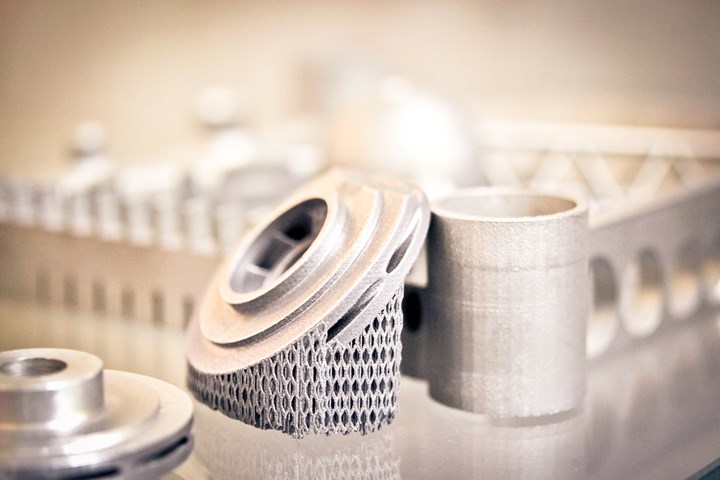
The industrialization of additive manufacturing (AM) has been a long time coming, or so it seems given the rapid pace of digitalization and technological change these days. Consider the time it took casting, machining and other manufacturing processes to gain widespread use and contribute effectively to production. In that context, the 30 or so years that AM has been around isn’t actually all that long. In fact, AM is still very much in its infancy when you compare it other, more established (that is, mature) manufacturing processes that are traditionally used for part production.
Despite its relative infancy, AM has made major strides, particularly over the past decade, that have enabled it to be used for part production in several industries, including highly regulated ones like aerospace and medical. If you stop and search for a minute, you can easily find a dozen or so companies across a variety of industries that now employ AM for part production, not just prototypes, spares or one-offs. I can offer a list of names, but I challenge you to search and find 8-10 on your own if you can’t think of any off hand. (If you aren’t having any luck, feel free to send me an email or connect with me on LinkedIn, and I’ll share the growing list that I keep.)
Searching should reveal that part production quantities in the tens and hundreds are easy to achieve, thousands and tens of thousands are within earshot and even hundreds of thousands can be made if things align (puns intended). Even the automotive industry is investing heavily in metal AM for part production, thanks to lower costs, more reliable AM systems and, of course, continued bottlenecks in the supply chain. Granted, getting to millions of metal parts with AM will take a while, but the signs (and continued advancements) are there. AM is finding inroads on luxury and high-end vehicles, which enjoy higher margins to begin with — much like racecars, which will spare no expense to shave a second or two off each lap.
If you’re of the mindset that AM is only for prototyping, think again. The standard definition of AM was recently updated in ISO/ASTM 52900:2021.
AM Is Defined as:
- a process, just like machining, casting, forging, and injection molding are processes;
- of joining materials, be they polymers, metals, ceramics, other materials or combinations thereof, provided in powder, liquid, wire or some other solid form;
- to make parts, which are defined as “functional element[s] that can constitute all or a section of an intended product”;
- from 3D model data, be it a 3D solid (for example, CAD) model, STL or AMF file, DICOM file, 3D point cloud or other;
- usually layer upon layer, which leads to seven different types of AM processes based on how material(s) is/are added and joined together
- as opposed to subtractive and formative manufacturing technologies, which are two other prominent and well-established manufacturing processes for production
Vortic Watch Co. uses the laser powder bed fusion AM process (b) to join material (titanium powder, c) to make parts (in this case, watch cases to convert antique pocket watches into wrist watches, d) from 3D model data (CAD, STL, and build file, e, f and g) layer upon layer (which are oriented to create the bezel, h) as opposed to subtractive manufacturing (avoiding material waste if machined) and formative technologies (avoiding high costs of tooling). Photo Credit: Tim Simpson
It is telling that this new definition replaces “objects” with “parts,” stressing the functional nature of what is being additively manufactured, be it “all or a section of an intended product.” This is also new to the definition, recognizing the shift to part production that is occurring in industry. Meanwhile, the updated definition still leaves room for prototyping a “functional element” that represents all or a section of an intended product. This is actually where many companies are finding a strong case for metal AM, using functional prototyping to rapidly iterate on design alternatives and shorten development lead-times, regardless of whether they will shift to production with AM.
Additive part production capitalizes on the unique aspects of AM processes, which arise mainly from the “layer upon layer” terminology in the definition; however, the flexibility associated with “joining materials… from 3D model data” is equally advantageous. In fact, making parts from 3D model data gives rise to fundamentally different economic drivers with AM, the biggest of which was summed up by Patrick Dunne, VP of advanced application development at 3D Systems, as “the data is the tooling.” In other words, the high costs of tooling, fixtures, jigs and so on is not what drives the cost of AM as it does in other formative processes. Moreover, joining material(s) layer upon layer to make a part leads to less scrap and waste compared to subtractive processes, leading to additional economic benefits for AM.
In short, AM is starting to “grow up” as it enjoys more and more success on the production floor. As it matures, though, AM is unlikely to replace its older manufacturing siblings; AM will simply be more advantageous in some part production scenarios, “as opposed to subtractive and formative manufacturing technologies,” as the updated definition applies. The challenge, then, lies in finding and knowing those scenarios, which we will dive deeper into next month.
Related Content
With Electrochemical Additive Manufacturing (ECAM), Cooling Technology Is Advancing by Degrees
San Diego-based Fabric8Labs is applying electroplating chemistries and DLP-style machines to 3D print cold plates for the semiconductor industry in pure copper. These complex geometries combined with the rise of liquid cooling systems promise significant improvements for thermal management.
Read MoreThis Drone Bird with 3D Printed Parts Mimics a Peregrine Falcon: The Cool Parts Show #66
The Drone Bird Company has developed aircraft that mimic birds of prey to scare off problem birds. The drones feature 3D printed fuselages made by Parts on Demand from ALM materials.
Read MoreVulcanForms Is Forging a New Model for Large-Scale Production (and It's More Than 3D Printing)
The MIT spinout leverages proprietary high-power laser powder bed fusion alongside machining in the context of digitized, cost-effective and “maniacally focused” production.
Read MoreHow Machining Makes AM Successful for Innovative 3D Manufacturing
Connections between metal 3D printing and CNC machining serve the Indiana manufacturer in many ways. One connection is customer conversations that resemble a machining job shop. Here is a look at a small company that has advanced quickly to become a thriving additive manufacturing part producer.
Read MoreRead Next
Smart, Fast Prototyping Informs Redesign for AM
Rapid intelligent prototyping can reveal how best to proceed when developing design guidelines for additive manufacturing.
Read MoreHow Prototyping Addresses Unknowns and Reduces Risks
One benefit of metal AM is the capability to create functional prototypes in less time, enabling you to rapidly iterate on design alternatives during development.
Read MoreA Machine Shop Poised for Additive Production
By laying the groundwork now, Able Tool will be prepared for the day when machine shops are commonly called to produce metal parts via additive manufacturing.
Read More