How to Build 10,000+ Shot Molds in Hours
Sponsored ContentRapid tooling isn’t so rapid when it takes days to 3D print a metal mold, and then you still must machine it to reach the necessary tolerances. With Nexa3D’s polymer process you can print a mold in hours that is prototype or production ready and can last for more than 10,000 shots.
Share
Read Next
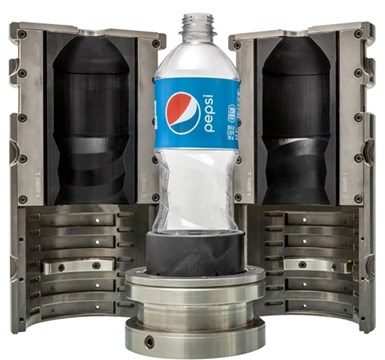
Rapid tooling was one of the first applications of 3D printing. Early on, while print times were very long and materials were very limited, prototype tooling could nonetheless be created more quickly than by using conventional mold machining methods. But the 3D printers were expensive, the molds weren’t terribly accurate, and they only lasted long enough to produce a handful of parts. While this was certainly an improvement by enabling greater use of molded prototypes, it didn’t reduce time-to-market cycles as much as proponents had hoped. When it came time to build production tooling you had to start all over again and that still took weeks or months as it always had.
Nexa3D’s liquid polymer additive manufacturing process is changing all that. Capable of printing a range of more durable materials in much shorter cycle times, the company’s LSPc® 3D printing process can generate complex mold cores and cavities in under a day. Depending on the material, these molds can last up to 10,000 shots or more. That enables plastic molders to move from prototype immediately into production. For small to medium runs, that may be the only tool you’ll need. For longer runs, it buys time to build permanent tooling while production continues with the 3D-printed mold. Another option is printing multiple mold inserts which can be done on demand.
Building a Better Moldmaking Process
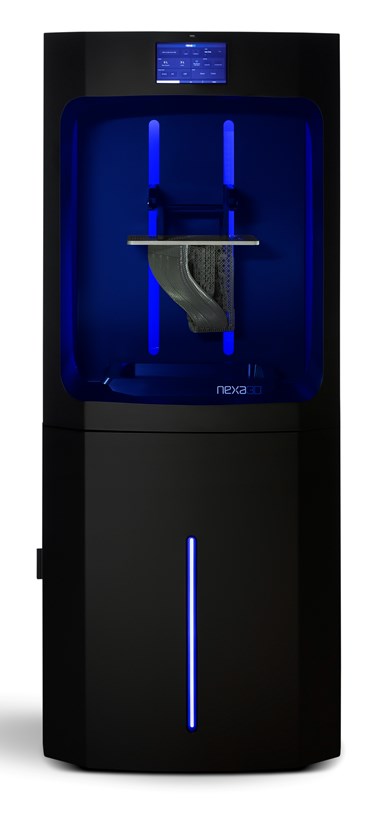
Nexa3D’s 400 model printer features a 17-liter build chamber.
The first rapid molds were largely made of silicone rubber and still required a pattern as the tool itself was molded around the pattern form. Then came metal molds made directly with a powder metal deposition and sintering process. These molds were stronger, but still only suitable for limited runs because the materials were relatively soft compared to tool steels. Perhaps a larger issue was that the molds weren’t very accurate due to a coarse deposition process by today’s standards, and the sintering process induced unpredictable shrinkage in the tool. Moreover, surface finishes typically were not sufficient for injection molding, so the tool still had to be machined to reach final form and finish. But this basic process did enable the ability to generate mold features previously impossible to make with conventional methods, such as conformal cooling channels, that improved the molding process itself.
Metal additive manufacturing processes have greatly improved since, but they still can be very slow and haven’t eliminated the need to machine most 3D printed molds for the same old reasons – to achieve the required accuracy and surface finish. This is where Nexa3D’s LSPc process comes in.
If you haven’t seen it, Nexa3D’s photopolymerization process is remarkably fast. It is based on LSPc technology (lubricant sublayer photo curing) which dramatically speeds the time it takes to move from layer to layer. Most modern resin 3D printers (including SLA and DLP) are “inverted,” meaning they print upside down, and they cure against a vat bottom or vat membrane. In the case of Nexa3D printers, light is projected up with channels and light guides to assure uniformity across build area. The light travels through an LED light mask where it gets finely pixilated to assure edge-to-edge part consistency and accuracy. Normally care must be taken to peel the part away from the vat, typically a slow and delicate operation. LSPc technology leverages a self-lubricated, flexible membrane that resists sticking to both the printed part and the underlying screen, which enables much faster printing speeds (not to mention a more dynamic range of printable geometries with fewer supports).
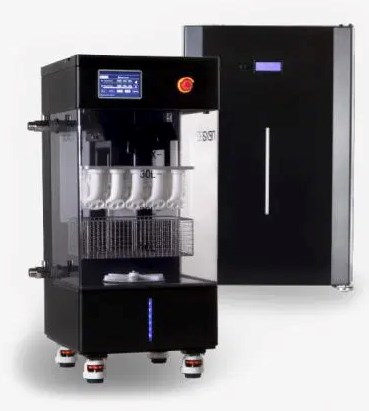
Nexa3D has developed integrated stations for washing and curing printed parts, with the ability to accomplish both on the same baseplate platform.
The technique enables vast improvements in cycle time and throughput. Since the speed of output is based solely on vertical height of the build, the total print time will be the same regardless of the number of parts you are printing across the build plate. Even at high printing speeds the printer can achieve injection molded quality with sharp angles, smooth surfaces and perfectly round holes. Overall, the LSPc process enables production speeds that are up to 6.5x faster than other 3D printers from the same class.
Moreover, the Nexa3D 400 model includes a 17-liter build volume which is 2.5x greater than other comparable SLA and DLP-based technologies. This allows for much larger parts, or more parts per build, with higher throughput, and ultimately lower part cost — all with higher-resolution pixels (76.5 µm) and isotropic prints. Bottom line, Nexa3D printers can produce complicated polymer tools in as little as 12 hours with very little post-processing required, and no machining at all.
With this capability, innovative manufacturers are finding new ways to accelerate their product development cycles. Here are two great examples.
CAD to Blow Molded Part in 48 Hours
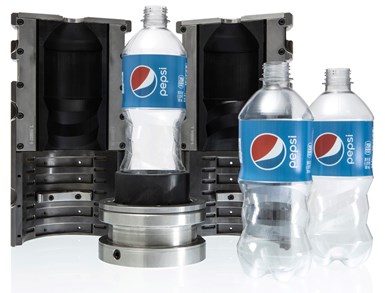
PepsiCo’s blow molding process uses a standard shell that is customized with 3D printed inserts.
PepsiCo was no stranger to using rapid tooling to produce its soda bottles. But the company’s approach still would take two to three days to 3D print a single blow mold first with Digital ABS (an expensive material) on a $250,000 3D printer, then using the faster but equally expensive 3D printer. In both cases, the resulting tool lacked durability and could produce only about 100 bottles.
This prompted Pepsi’s Senior Manager of Global Packaging, Max, Rodriguez, and his team to explore developing a hybrid approach, combining parts of a conventional metal mold with 3D printed inserts. This patented method involves using a universal metal outer mold shell that fits into most commercial blow molding machines. PepsiCo then explored using additive manufacturing to print only the essential internal parts of the mold that yield the final product’s geometry.
PepsiCo chose Nexa3D’s xPEEK147 from Henkel Loctite for the 3D-printed tool inserts due to the material’s strength and high-performance factors, including its very high heat-deflection temperature. The inserts would be printed on a Nexa3D NXE 400 printer.
A complete mold set can now be made in 12 hours, with 8 hours of 3D printing time and 4 hours of curing. These hybrid-made molds can then be used for more than 10,000 bottles (in Pepsi’s latest run they achieved over 14,000 shots and still haven’t reached the limit). The team at Pepsi also noted that the NXE 400 is about 1/3 the price of their previous 3D printer, with a larger build volume. All told, this new rapid tooling approach has reduced cost by up to 96% in comparison to traditional metal tooling.
While cost reduction is certainly welcomed, Rodriguez says an even bigger benefit is the flexibility the new process brings to their blow molding operation. “More important is to have the flexibility to run through a number of different design iterations at a record pace so that we can evaluate performance in all of the downstream activities,” he says. This approach “also facilitates our capability of validating our virtual tools because we are now able to pair them up with physical results,” he adds. This capability assists PepsiCo in its material characterization work, performance analysis, and physical testing. Overall, Rodriguez expects their development cycle to be reduced by 30 percent.
The “Fail Fast” Approach to Reducing Time to Market
The Wilson Sporting Goods R&D team was looking for a more effective means to produce prototype injection mold tooling for youth baseball bat handles. Wilson wanted to reduce time to market for these products, and the key was to find a faster way to produce functional and testable prototypes.
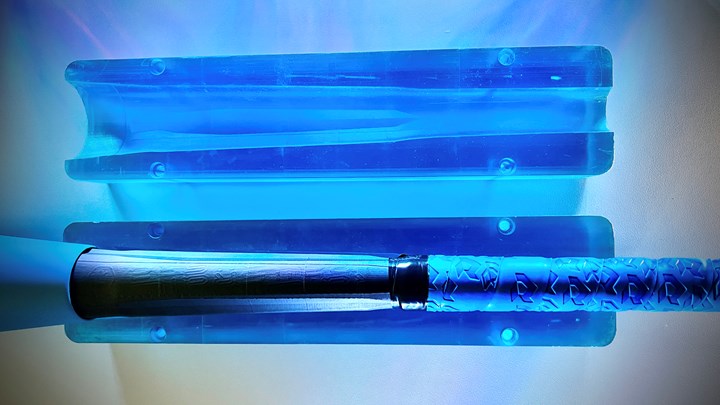
Wilson Sporting Goods can typically produce a bat handle prototype in a day.
A critical enabler to this process was provided by Nexa3D partner Addifab, developer of “Freeform Injection Molding.” Freeform is an innovative approach to prototyping where a disposable mold is 3D printed, filled with resin on a standard injection molding machine, and then the mold can be dissolved to release the part. For complex parts, the mold is dissolved by soaking in an alkaline water solution for 12-48 hours. In Wilson’s application, however, the molds are made in a more traditional fashion and can be reused for multiple shots.
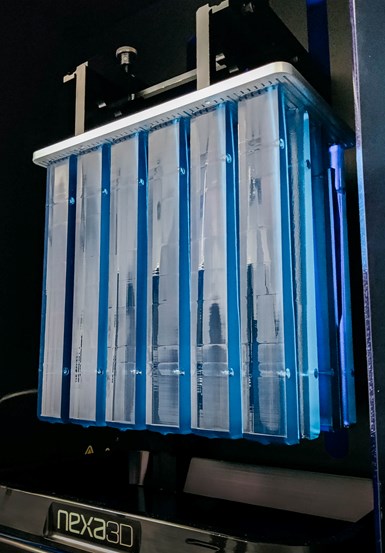
Wilson can print multiple molds in a single build.
According to Glen Mason. Manager of Advanced Innovation/Industrialization at DeMarini (a division of Wilson Sporting Goods), “With Nexa3D’s large print envelope and ultrafast LSPc process, the Wilson R&D group can now produce multiple parts at once, in a rapid manner, allowing for multiple design iterations in a single print batch. In addition, what were previously several components assembled together can now be printed into one singular part, reducing assembly time and increasing durability for a given part.”
With Addifab, the R&D designers also have much more design and material flexibility compared to using traditional metal tooling for plastic injection molding. “Our designers can afford to be off in their tolerancing for these tools now, whereas with metal tooling, even a few microns off can make or break the initial design. Additionally, with Addifab’s proprietary resin material, there is no concern over adhesion or bonding of the plastic materials during the injection molding process.” After drafting an initial concept, the R&D team can typically produce a prototype in a single working day – a process that would have taken months to create previously.
“Because we can iterate so much quicker, print tools faster than we can machine, and eliminate a couple of the steps in the process, our R&D team can afford to be wrong. This helps us to greatly improve our time-to-market, allowing us to be quick and nimble with our design decision-making process. We also no longer have to worry about traditional design-for-manufacturing constraints such as where to place the gate, how material will flow through the part, part warpage/deviation, or even strict tolerancing, compared to our previous tooling manufacturing,” says Mason.
Compressing the Entire 3D Printing Process
While a fast cycle time is critical to efficient 3D printing, it’s not the only thing. How you choose the right parts for AM, prepare jobs for production, and manage post processing will have just as big an impact on total 3D printing throughput. It all needs to work together to achieve maximum productivity.
Nexa3D has made this factor a priority in its own product development and offers a suite of technology that addresses every phase of the photopolymer additive manufacturing process. It all begins with the AM software. Through the interplay of hardware, software and chemistry, NexaX 2.0 is an AI-based software application that offers print preparation and 3D printer management. Along with API integration to other software, NexaX enables the realization of new properties for printed parts while enabling process stability, production scaling, consistent product quality, higher yields and excellent mechanical performance. It provides a variety of tools to aid total process efficiency such as quick file preparation, how to stack parts for maximum throughput, even how to place supports for easy removal. The software also includes seamless integration with Nexa3D’s large and growing materials portfolio and can even suggest material alternatives for any given part.
On the back end, Nexa3D has developed integrated stations for washing and curing printed parts, with the ability to accomplish both on the same baseplate platform. xWASH is a washing station designed to work with Nexa3D printers that uses a proprietary washing agent optimized for 3D printing and sustainability. xCURE is designed to consistently and rapidly assure desired photopolymer part properties at production quantities. It also comes with prescribed part processing menus that apply consistent process controls to achieve high dimensional accuracy and structural integrity regardless of part size or complexity.
By combining faster printing with these pre- and post-production technologies, Nexa3D says it can compress the total art-to-part cycle time as much as 20 times compared to many 3D printing processes used today. For companies like PepsiCo and Wilson that want development cycles measured in days, this total systems approach to additive manufacturing is the key enabler to make it happen.
Please visit Nexa3D.com for more information on Nexa3D printers and software.